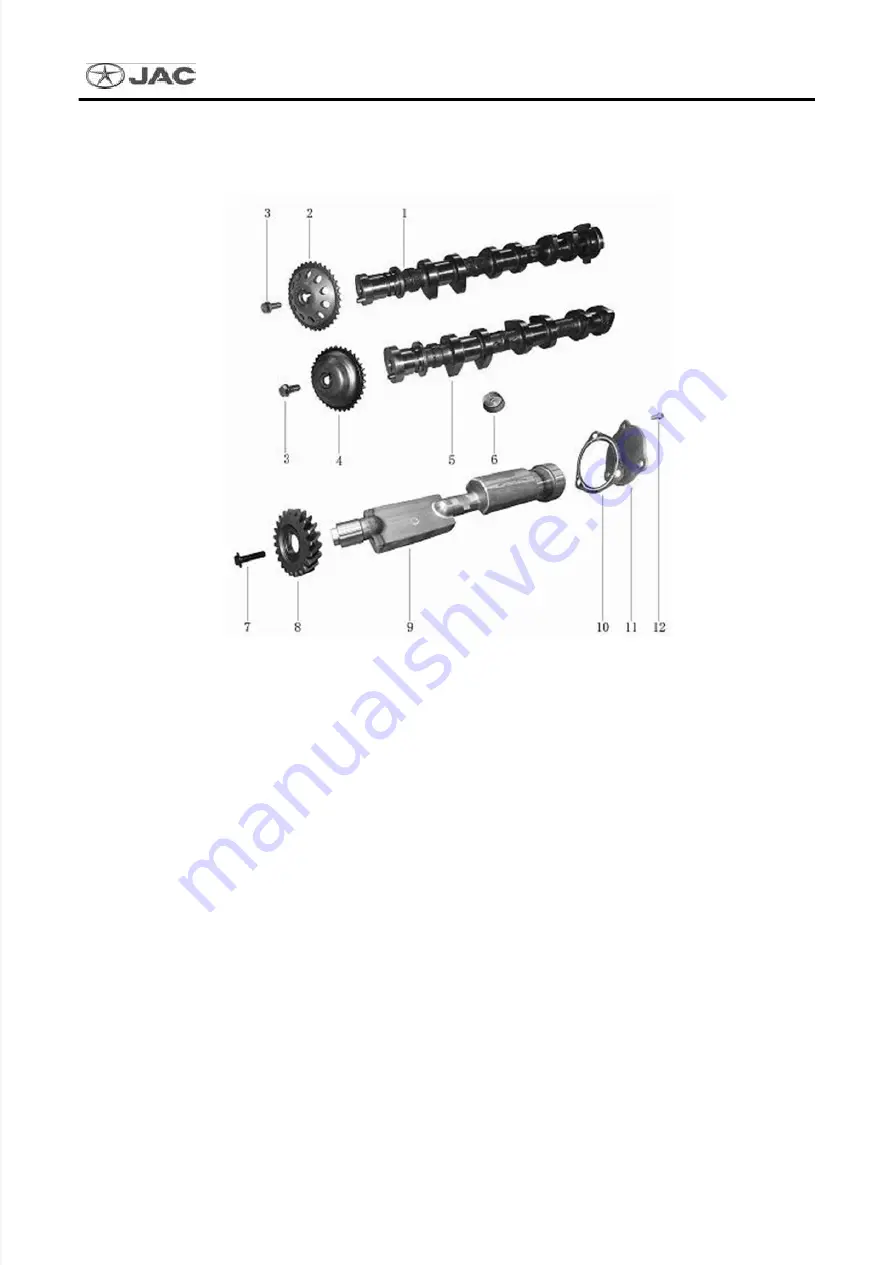
Maintenance Manual for J2 Sedan
Mechanical Part of Engine
58
X. Camshaft and balance shaft assembly
1. Parts
Breakdown diagram for camshaft and balance shaft
1 – Intake camshaft subassembly 2 – Intake camshaft chain wheel 3 – Chain wheel bolts
4 – Exhaust camshaft chain wheel 5 – Exhaust camshaft subassembly 6 – Mechanical tappet
7 – Balance shaft retaining bolt 8 – Balance shaft gear 9 – Balance shaft
10 – Balance shaft rear end cap gasket 11 – Balance shaft rear end cap
12 – Balance shaft rear end cap bolts
2. Disassembly and installation
1
)
Disassembly of camshaft
①
Remove cylinder cover. See "Intake Manifold."
②
Remove high-voltage ignition coil. See "Ignition Coil."
③
Disconnect PCV hose and air hose of respirator.
④
Remove the cylinder head cover from the cylinder head.
⑤
Remove camshaft timing sprocket. Seethe "timing sprocket body."
⑥
Remove camshaft position sensor from rear end of the cylinder head.
Tightening torque: 9 - 11 N • m