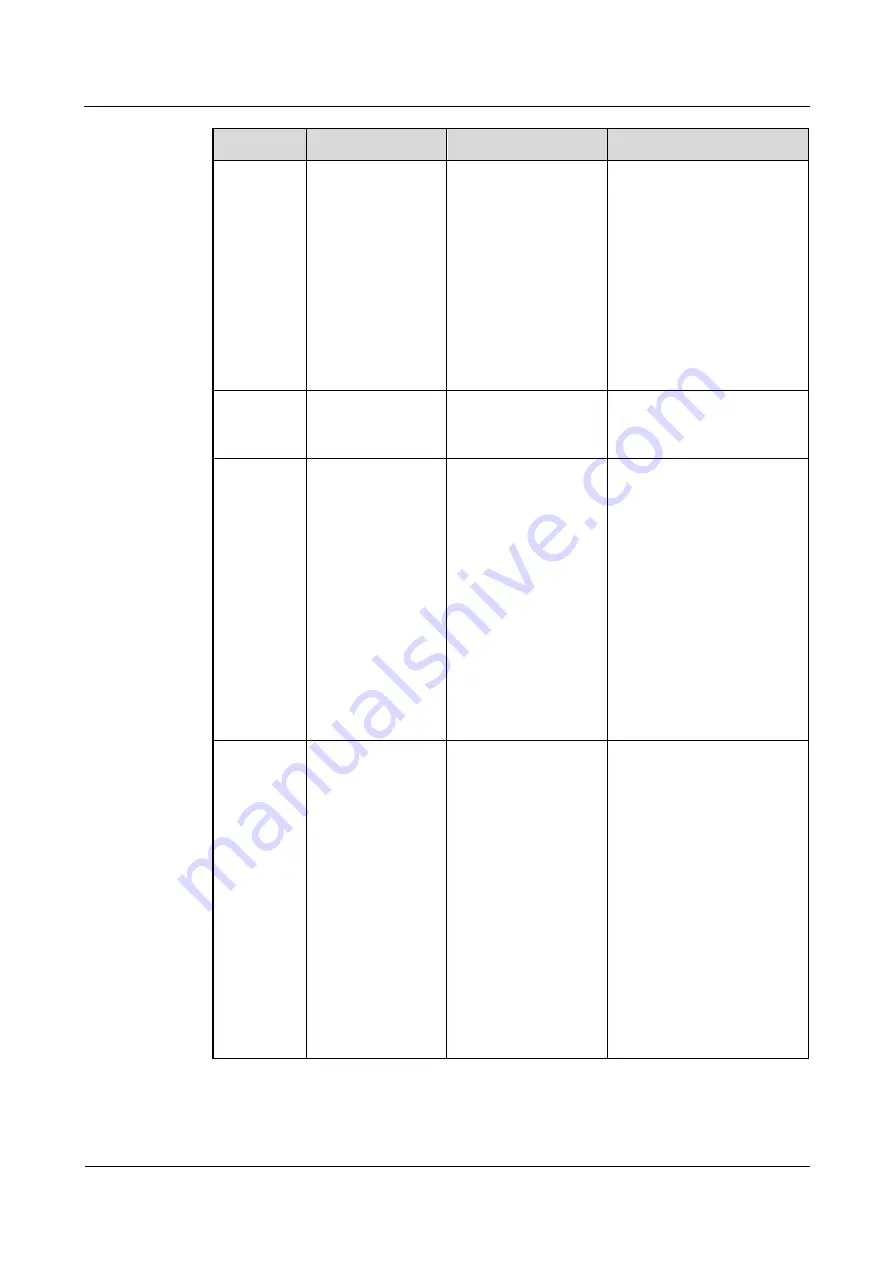
FusionModule1000A40 IT Solution
Maintenance Guide (2016.05, AI Version)
3 Maintenance
Issue 04 (2018-01-05)
Huawei Proprietary and Confidential
Copyright © Huawei Technologies Co., Ltd.
38
Device
Operation
Check Standard
Maintenance Guide
Fire alarm
bell
Flip the key to
Enable Control
on
the extinguishant
control panel
rightward. Press
Silence/Sound
Alarm
to start or
abort the fire alarm
bell. Reset the key
to
Enable Control
by flipping it
leftward.
The alarm bell rings
normally. The alarm
bell rings loud and
clear when it is
started.
1.
Check and reconnect
cables to the fire alarm
bell.
2.
Replace the fire alarm
bell if the fault persists.
Warning
sign
Pull up the reset
button on the
pneumatic switch.
The warning sign
indicator is on.
Replace the warning signs.
Heat
detector
Heat the heat
detector using a
heating device.
1.
If the temperature
is below the alarm
threshold, the
alarm indicator
blinks once every
6s.
2.
If the temperature
is above the alarm
threshold, the
indicator turns on.
The extinguishant
control panel
generates an alarm
and triggers the
fire alarm bell.
Replace the heat detector.
Smoke
detector
Release smoke
onto the smoke
detector using a
smoke pistol.
1.
If the smoke
density is below
the alarm
threshold, the
alarm indicator
blinks once every
6s.
2.
If the smoke
density is above
the alarm
threshold, the
indicator turns on.
The extinguishant
control panel
generates an alarm
and triggers the
fire alarm bell.
Replace the smoke detector.