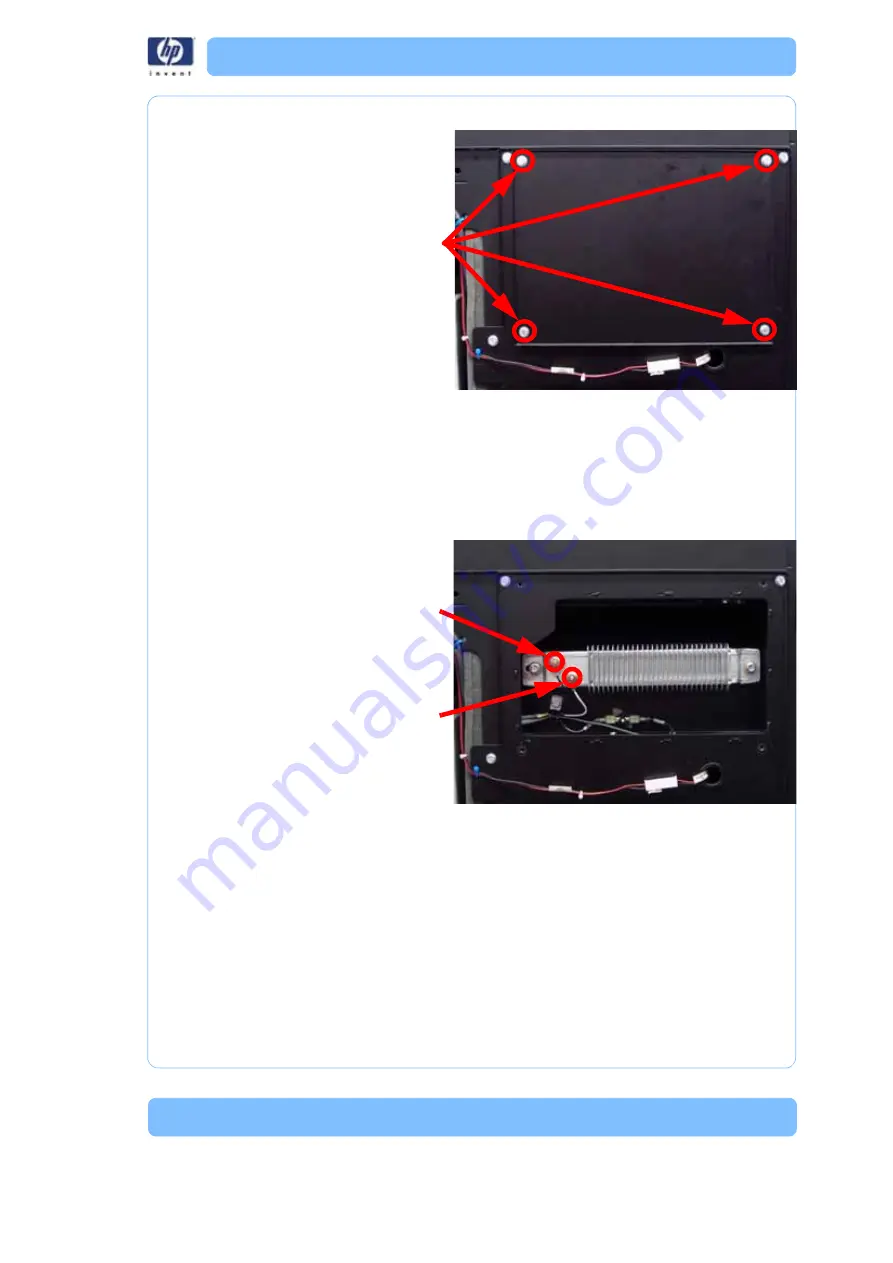
-313
Figure 291: Left side heater panel mounting screw locations
4. Using a
3
⁄
8
” nut driver, remove the white power wire from the right
mounting post. See
5. Using a
3
⁄
8
” nut driver, remove the black power wire from the left mount-
ing post. See
Figure 292: Power wire locations
6. Using a
5
⁄
16
” nut driver or standard screwdriver, remove the left and
right mounting screws. Do not lose the insulating washers as they are
need for reinstallation. See
Remove the 4
mounting screws
Remove the black
power wire
Remove the white
power wire
Summary of Contents for DESIGNJET 3D
Page 1: ...HP Designjet 3D HP Designjet Color 3D Service Guide ...
Page 3: ......
Page 4: ... 3 ...
Page 16: ... 12 ...
Page 40: ... 24 ...
Page 52: ... 36 ...
Page 70: ... 54 ...
Page 74: ... 58 ...
Page 90: ... 74 ...
Page 172: ... 156 ...
Page 314: ... 298 Figure 272 HP Designjet 3D measurement points and worksheet BL FL FR BR ...
Page 315: ... 299 Figure 273 HP Designjet Color 3D measurement points and worksheet BL FL FR BR ...
Page 349: ... 333 Figure 316 HP Designjet 3D measurement points and worksheet BL FL FR BR ...
Page 350: ... 334 Figure 317 HP Designjet Color 3D measurement points and worksheet BL FL FR BR ...
Page 352: ... 336 ...
Page 404: ... 388 Figure 402 HP Designjet 3D measurement points and worksheet BL FL FR BR ...
Page 405: ... 389 Figure 403 HP Designjet Color 3D measurement points and worksheet BL FL FR BR ...
Page 458: ... 442 ...