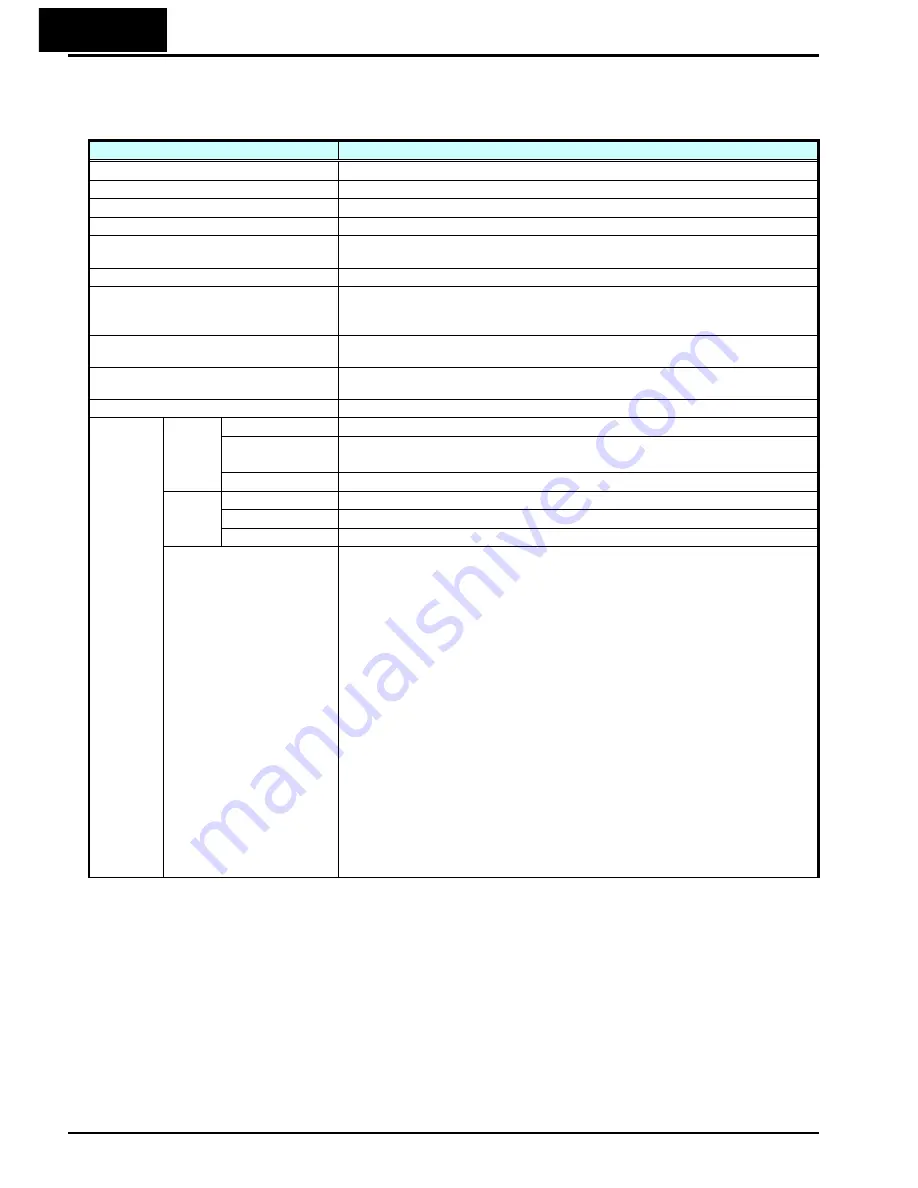
1
−
8
General Specifications
The following table applies to all WJ200 inverters.
Item
General Specifications
Protective housing *1
IP20
Control method
Sinusoidal Pulse Width Modulation (PWM) control
Carrier frequency
2kHz to 15kHz (derating required depending on the model)
Output frequency range *4
0.1 to 400Hz
Frequency accuracy
Digital command:
±
0.01% of the maximum frequency
Analog command:
±
0.2% of the maximum frequency (25
°
C
±
10
°
C)
Frequency setting resolution
Digital: 0.01Hz; Analog: max. frequency/1000
Volt./Freq. characteristic
V/f control (constant torque, reduced torque, free-V/F): base freq.
30Hz~400Hz adjustable,
Sensorless vector control, Closed loop control with motor encoder feedback
Overload capacity
Dual rating:
CT(Heavy duty)
: 60 sec. @150%
VT(Normal duty)
: 60 sec. @120%
Acceleration/deceleration time
0.01 to 3600 seconds, linear and S-curve accel/decel, second accel/decel
setting available
Starting torque
200% @0.5Hz (sensorless vector control)
Input
signal
Freq.
setting
Operator panel
Up and Down keys / Value settings
External signal
*8
0 to 10 VDC (input impedance 10k Ohms), 4 to 20mA (input impedance 100
Ohms), Potentiometer (1k to 2k Ohms, 2W)
Via network
RS485 ModBus RTU, other network option
FWD/
REV run
Operator panel
Run/Stop (Forward/Reverse run change by command)
External signal
Forward run/stop, Reverse run/stop
Via network
RS485 ModBus RTU, other network option
Intelligent input
terminal
Seven terminals,
sink/source changeable
by a short bar
68 functions assignable
FW (forward run command), RV (reverse run command), CF1~CF4
(multi-stage speed setting), JG (jog command), DB (external braking), SET
(set second motor), 2CH (2-stage accel./decel. command), FRS (free run stop
command), EXT (external trip), USP (startup function), CS (commercial
power switchover), SFT (soft lock), AT (analog input selection), RS (reset),
PTC (thermistor thermal protection), STA (start), STP (stop), F/R
(forward/reverse), PID (PID disable), PIDC (PID reset), UP (remote control
up function), DWN (remote control down function), UDC (remote control
data clear), OPE (operator control), SF1~SF7 (multi-stage speed setting; bit
operation), OLR (overload restriction), TL (torque limit enable), TRQ1
(torque limit changeover1), TRQ2 (torque limit changeover2), BOK (Braking
confirmation), LAC (LAD cancellation), PCLR (position deviation clear),
ADD (add frequency enable), F-TM (force terminal mode), ATR (permission
of torque command input), KHC (Cumulative power clear), MI1~MI7
(general purpose inputs for EzSQ), AHD (analog command hold), CP1~CP3
(multistage-position switches), ORL (limit signal of zero-return), ORC
(trigger signal of zero-return), SPD (speed/position changeover), GS1,GS2
(STO inputs, safety related signals), 485 (Starting communication signal),
PRG (executing EzSQ program), HLD (retain output frequency), ROK
(permission of run command), EB (rotation direction detection of B-phase),
DISP (display limitation), NO (no function)
Summary of Contents for WJ200 Series Software
Page 19: ...xviii Revisions Revision History Table No Revision Comments Date of Issue Operation Manual No ...
Page 295: ...4 92 Safe Stop Function To be finalized after TUV approval ...
Page 296: ...5 1 5 Inverter System Accessories In This Chapter page Introduction 2 Component Description 3 ...
Page 322: ...A 1 A Glossary and Bibliography In This Appendix page Glossary 2 Bibliography 8 ...
Page 378: ...B 49 Note 2 Be sure not to write into above 1F02h to 1F1Dh ...