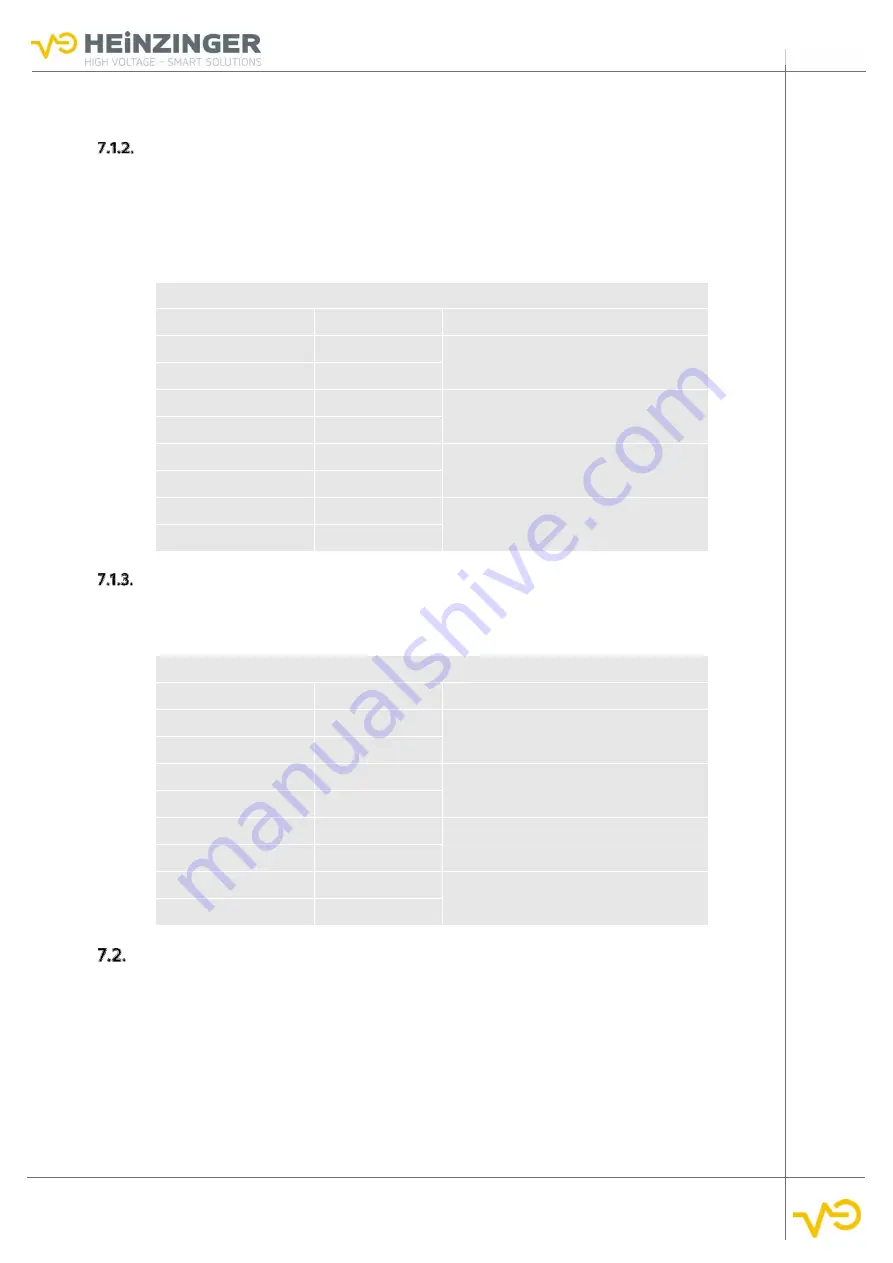
Manual ERS-BIC 160 kW V2.1
67
Channel Stop (optional)
For performance level C and above, there are additional pins for the channel stop. If the channel stop
is triggered by the interruption of the connection between the related contacts, it specifically
switches off the channel in question and the output contactors are opened. However, the other chan-
nel of the system is not affected and can continue to operate. Here, too, there are further potential-
free contacts which output the status of the channel stop independently for both channels.
Table 36 Pin assignment -X4.2 Channel stop
Signal
Pin –X4.2
Description
CHANNEL_STOP-1
1
Channel stop 1:
Loop closed = OK
CHANNEL_STOP-1
2
CHANNEL_STOP-2
3
Channel stop 2:
Loop closed = OK
CHANNEL_STOP-2
4
FB_channel-stop_1
5
Feedback channel stop 1:
Potential free contact, Open = OK
FB_channel-stop_1
6
FB_channel-stop_2
7
Feedback channel stop 2:
Potential free contact, Open = OK
FB_channel-stop_2
8
Feedback Output Contactor (optional)
On -X4.3 there are potential-free contacts from Performance Level C on which output the status of
the output contactors. This allows a safe detection of the status at the output of the ERS and pro-
tection in case of failure to open a contactor.
Table 37 Pin Assignment-X4.3 Feedback output contactors
Signal
Pin –X4.3
Description
FB_contactor CH1_P
1
Feedback Channel 1 pos. contactor(s):
Potential free contact, open = open
FB_contactor CH1_P
2
FB_contactor CH1_N
3
Feedback Channel 1 neg. contactor(s):
Potential free contact, open = open
FB_contactor CH1_N
4
FB_contactor CH2_P
5
Feedback Channel 2 pos. contactor(s):
Potential free contact, open = open
FB_contactor CH2_P
6
FB_contactor CH2_N
7
Feedback Channel 2 neg. contactor(s):
Potential free contact, open = open
FB_contactor CH2_N
8
CAN-Bus
By default the device has a CAN-bus interface. This serves to control the ERS by the process control
system. A list of the transferred parameters is given in the appendix. The connection is made via the
Sub-D connector –A28 (For positioning see
Fig. 30, p. 35
). A list of the possible command words the
ERS can transmit or receive is given in the appendix.