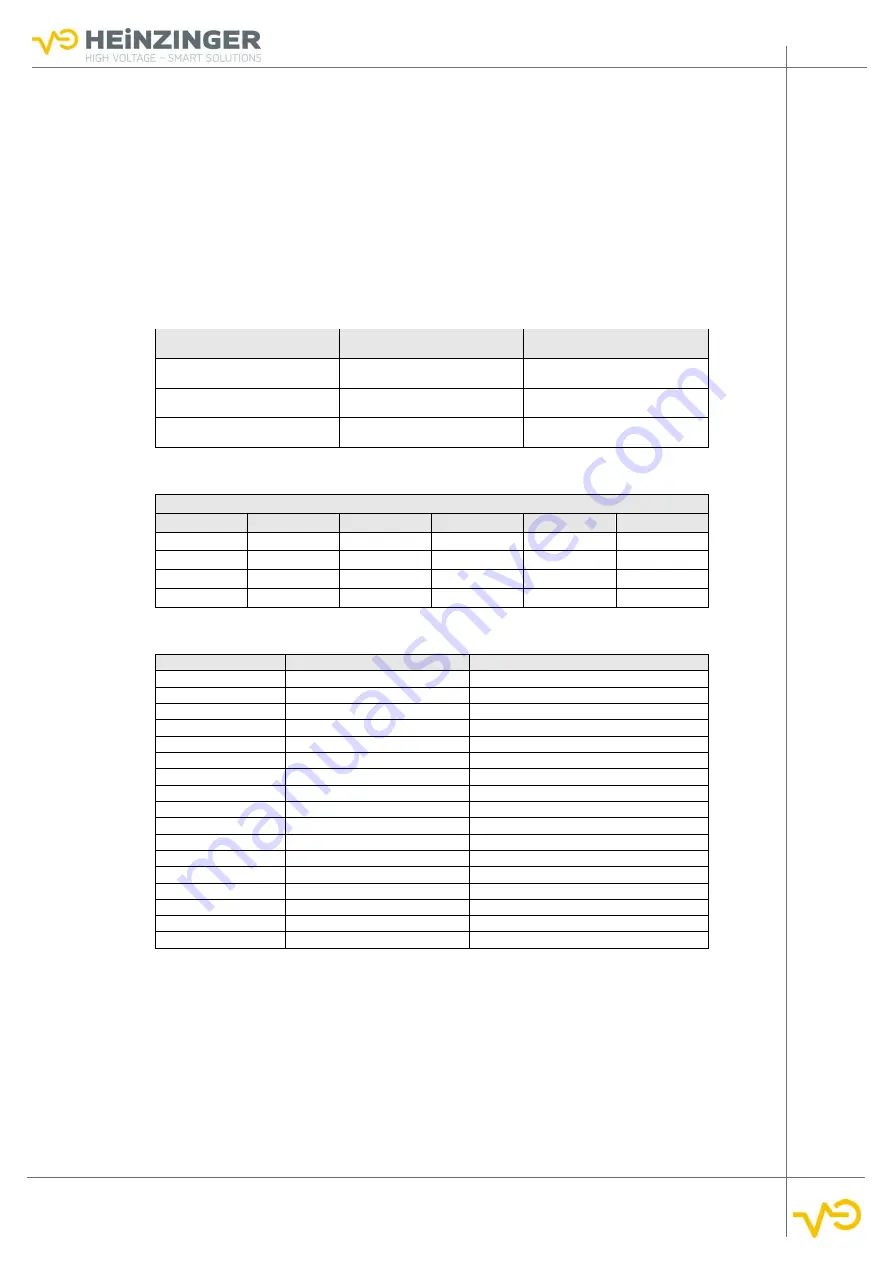
Manual ERS-BIC 160 kW V2.1
99
B . F .
Co nt r o l l e r m o d e “ B a t t e r y T e s t ”
Optimized for voltage-controlled bidirectional operation on inverters, DCDC converters, etc.
Controller is optimized for disturbance variables, i.e. designed for load jumps
E
X A M P L E
B
A T T E R Y
T
E S T
:
Test item:
Battery with 400V
Control mode:
voltage control CV
Operating mode:
bidirectional
Correct
Wrong
Wrong
V
set
= 400 V
V
set
= 440 V
V
set
=
380
V
I
set
= 100 A
I
set
= 100 A
I
set
= 100 A
P
set
= 50 kW
P
set
=
0 kW
P
set
= 50 kW
C.
E L ECTR OC H E MIC A L P O TE NTI A L S
Potentials against hydrogen of selected materials
Material
Potential/V
Material
Potential/V
Material
Potential/V
Aluminum
-1.67
Mangan
-1.05
Zinc
-0.76
Chrome
-0.71
Iron(II)
-0.44
Cobalt
-0.28
Nickel
-0.25
Tin
-0.14
Lead
-0.13
Iron(III)
-0.037
Hydrogen
0
Copper
0.34
D .
RE FE RE N CE L I S T A C CE S S O RI E S
Accessory-Nr.
Heinzinger-Item Number
Designation
1
05.070.308.20
Cage clamp 22-28 VA
4a
05.070.308.39
Cage clamp 22-28
4b
05.070.308.38
Counter trough 22-28
5a
05.070.308.40
Cage clamp 16-22
5b
05.070.308.41
Counter trough 16-22
6a
05.070.308.42
Cage clamp 12-16
6b
05.070.308.43
Counter trough 12-16
7a
05.070.308.44
Cage clamp 34-40
7b
05.070.308.45
Counter trough 34-40
20
06.020.672.02
Cover profile
21
06.030.348.60
Rail for serial connection
22
06.030.354.14
PE-CU-rail
23
06.030.502.00
Hose clamps
30a
06.030.118.50
Bolt M10x40
30b
06.030.122.00
Washer
30c
06.030.124.26
Spring washer
30d
06.030.125.10
Nut M10