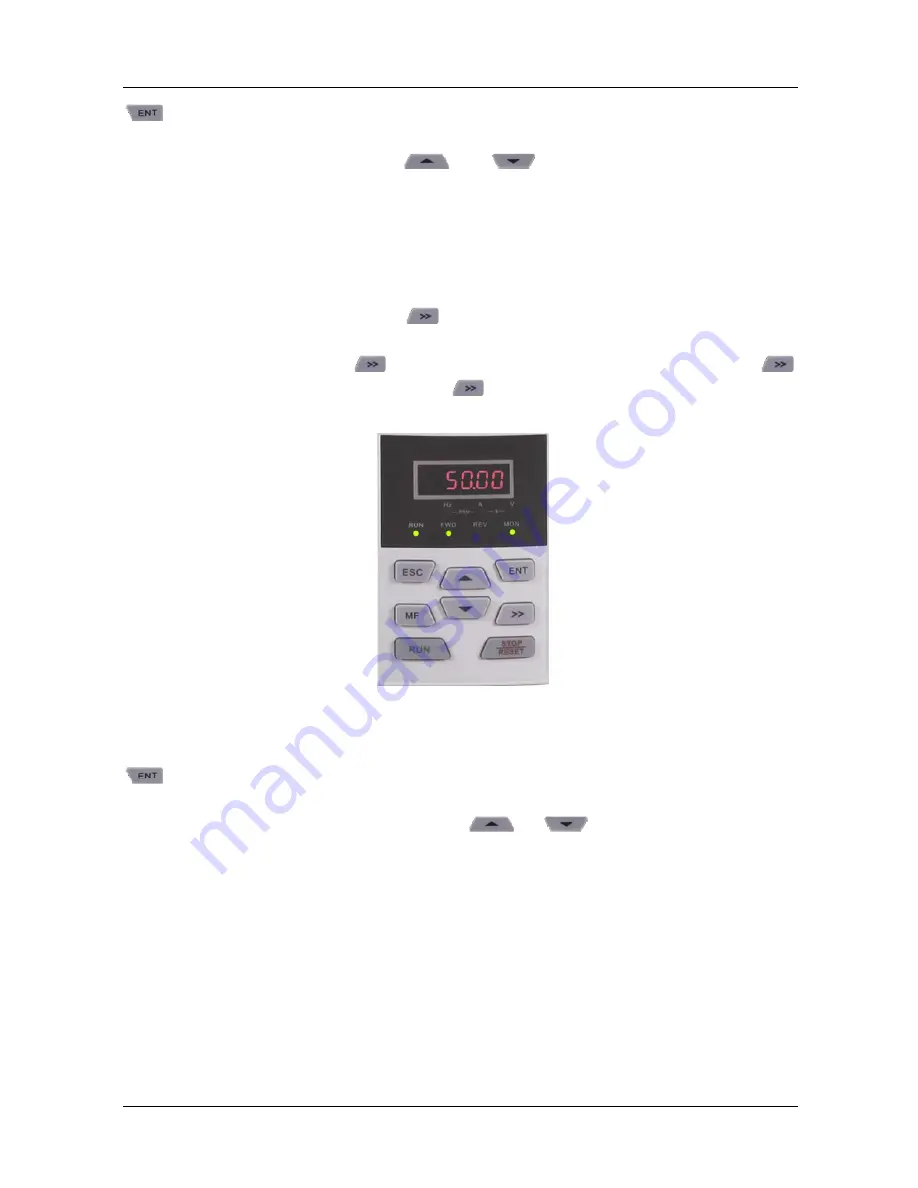
GK600E User Manual
Chapter 4 Operation and Run Instructions
- 43 -
to get into parameter edit status (get into passw ord authentication status if parameter
under passw ord protection). Directly get into frequency modification status w hen receive
UP/DOWN command from terminal, or
and
pressing on control panel. Sw itch to
fault display status once a fault occurs or an alarm is given.
4.1.3.2 Run Parameter Display Status
In case there is no fault, the drive w ill get into run parameters display status upon receipt of run
command. Default display is run frequency, and other parameters can be displayed through
setting of L1-00 and L1-01 and press
to shift. For example, in run status, w hen users
need to check bus voltage, motor speed, and input terminals status, please set L1-00= 0084
and L1-01= 0004, and press
to shift to the display of bus voltage, then press
again to display motor speed, and then press
to display input terminals state value.
Fig. 4-3 Run parameter display status (Displaying run frequency
– 50.00Hz)
Stop status w ill be enabled immediately upon receipt of stop command in such a status. Press
to get into parameter edit status (get into passw ord authentication status if parameter
under passw ord protection). Directly get into frequency modification status w hen receiving
UP/DOWN command from terminal, or pressing
or
. Sw itch to fault alarm display
status once a fault occurs or an alarm is given.
4.1.3.3 Fault Alarm Display Status
In case a fault occurs or an alarm is given, the drive w ill get into fault or alarm display status.