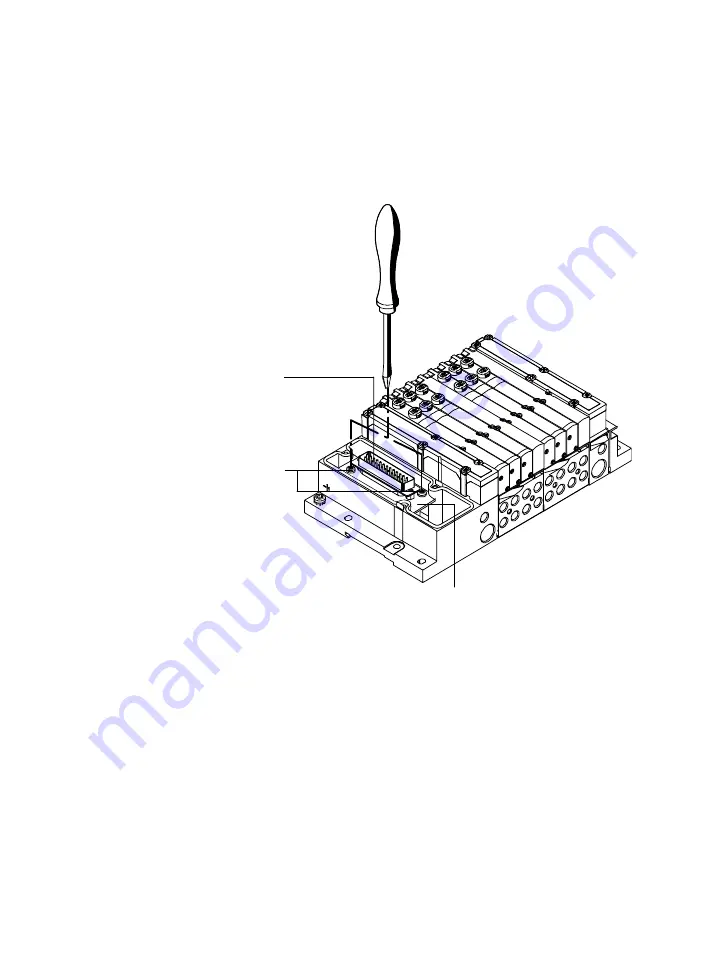
5. Diagnosis and error treatment
5−27
Festo P.BE−MPA−EN en 0502b
1
Multipin plug
2
Board
3
Fastening screws
2
1
3
Fig.5/11: Removing the multipin plug
4. MP connection:
Pull the board with the multipin plug carefully away from
the printed circuit board.
5. Loosen the fastening screws between the MP or MPM
sub−base and the pneumatic sub−bases in the sequence
3 2 1
(see following diagram).
6. Then loosen and remove the fastening screws.
Summary of Contents for MPA-FB Series
Page 2: ......
Page 4: ...Contents and general instructions II Festo P BE MPA EN en 0502b...
Page 8: ...Contents and general instructions VI Festo P BE MPA EN en 0502b...
Page 17: ...Summary of components 1 1 Festo P BE MPA EN en 0502b Chapter 1...
Page 30: ...1 Summary of components 1 14 Festo P BE MPA EN en 0502b...
Page 31: ...Fitting 2 1 Festo P BE MPA EN en 0502b Chapter 2...
Page 47: ...Installation 3 1 Festo P BE MPA EN en 0502b Chapter 3...
Page 55: ...3 Installation 3 9 Festo P BE MPA EN en 0502b 1 2 3 Fig 3 2 Disconnecting the tubing...
Page 79: ...Commissioning 4 1 Festo P BE MPA EN en 0502b Chapter 4...
Page 96: ...4 Commissioning 4 18 Festo P BE MPA EN en 0502b...
Page 97: ...Diagnosis and error treatment 5 1 Festo P BE MPA EN en 0502b Chapter 5...
Page 139: ...Technical appendix A 1 Festo P BE MPA EN en 0502b Appendix A...
Page 151: ...Accessories B 1 Festo P BE MPA EN en 0502b Appendix B...
Page 161: ...Index C 1 Festo P BE MPA EN en 0502b Appendix C...
Page 162: ...C Index C 2 Festo P BE MPA EN en 0502b Contents C Index C 1...