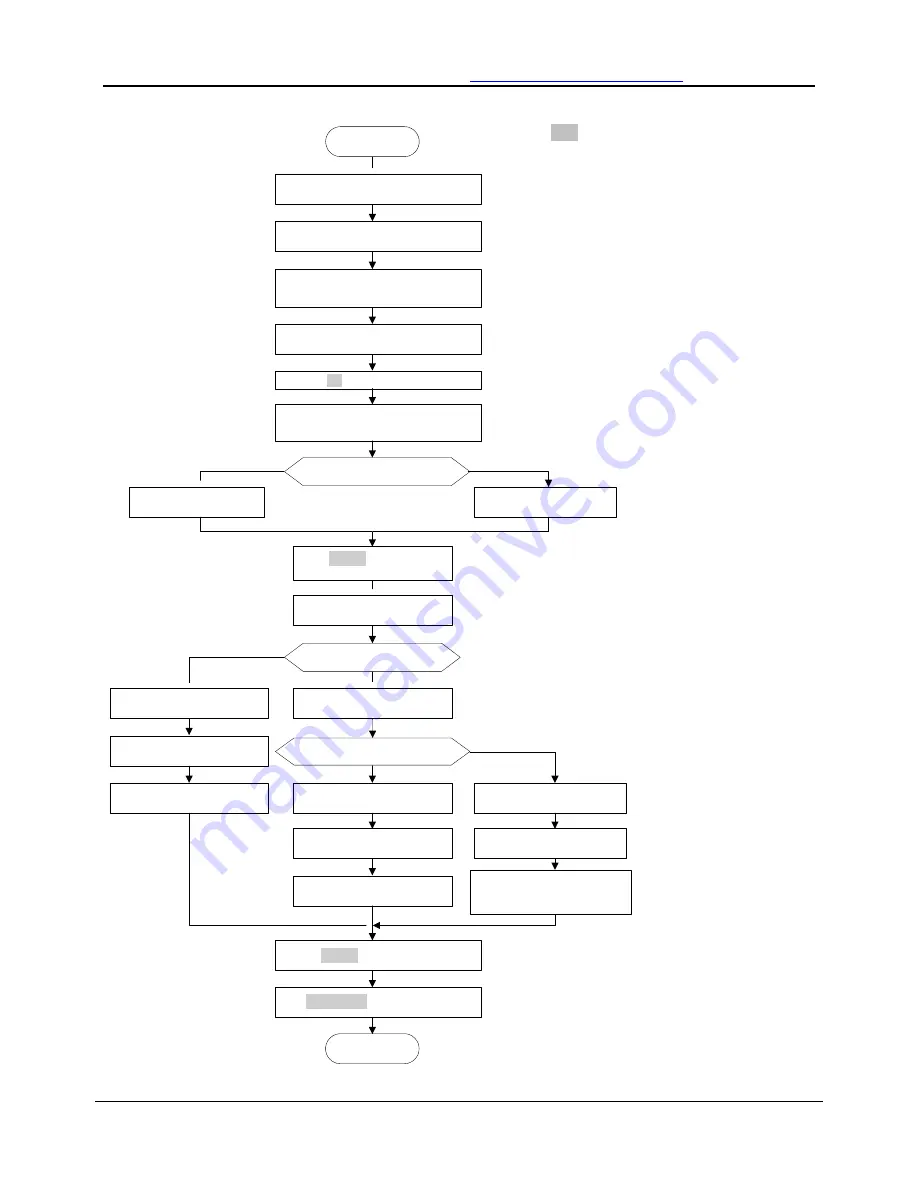
V&T Technologies Co., Ltd.
http://www.ecodrivecn.com
Chapter 4 Using Instructions of Operation Panel
42
Before power up, confirm the
wiring is correct
Setting P0.01=5 restore the
factory setting
Setting max output voltage P0.12 and motor
basic frequency P0.15 according to motor
nameplate
Press
M key for jog operation
If motor running direction is wrong, swap
any two phase wires of motor and then
power up
Press RUN key to run the inverter
Setting motor parameter P9.00 to
P9.04 according to motor nameplate
Press key to stop the inverter
Start
END
STOP/RST
Static tuning or rotating tuning
Setting running frequency P0.05
Vector control 1 or vector
control 2 ?
Setting P0.03 to vector control 1
Setting P0.03 to vector control 2
Setting
V/F curve input P4.00
Speed control or torque control
Setting Pd.00 to 0 speed control
Setting torque limit value Pd.08
and Pd.09
Adjust speed loop parameters
Pd.01 to Pd.05
Setting torque boost P0.16
Setting Pd.00 to 1 torque
control
Refer to P6.21 for torque
input channel selection
Set speed limit Pd.06 and Pd.07
during forward/reverse running
process or limit the speed via
analog channel
RUN
Setting P9.15=2 to
perform rotating auto-tuning
Press RUN key to start auto
tuning, after tuning stop auto
RUN
M
Setting P9.15=1 to
perform static auto-tuning
Note
:
◆
If fault happens, please judge the fault
causes and clear the fault according to
7.1 Fault and alarm information list.
◆
If motor can without connecting the load
rotating auto tuning can be selected
(P9.15=2),otherwise only static auto
tuning can be selected .When enabling
the auto tuning please ensure the motor is
in standstill status .If over voltage or over
current happens in auto tuning process,
you can prolong the acceleration and
deceleration times of P0.08 and P0.09.
◆
Upon vector control 2, the loads must
be detached before the rotating auto
tuning is performed.