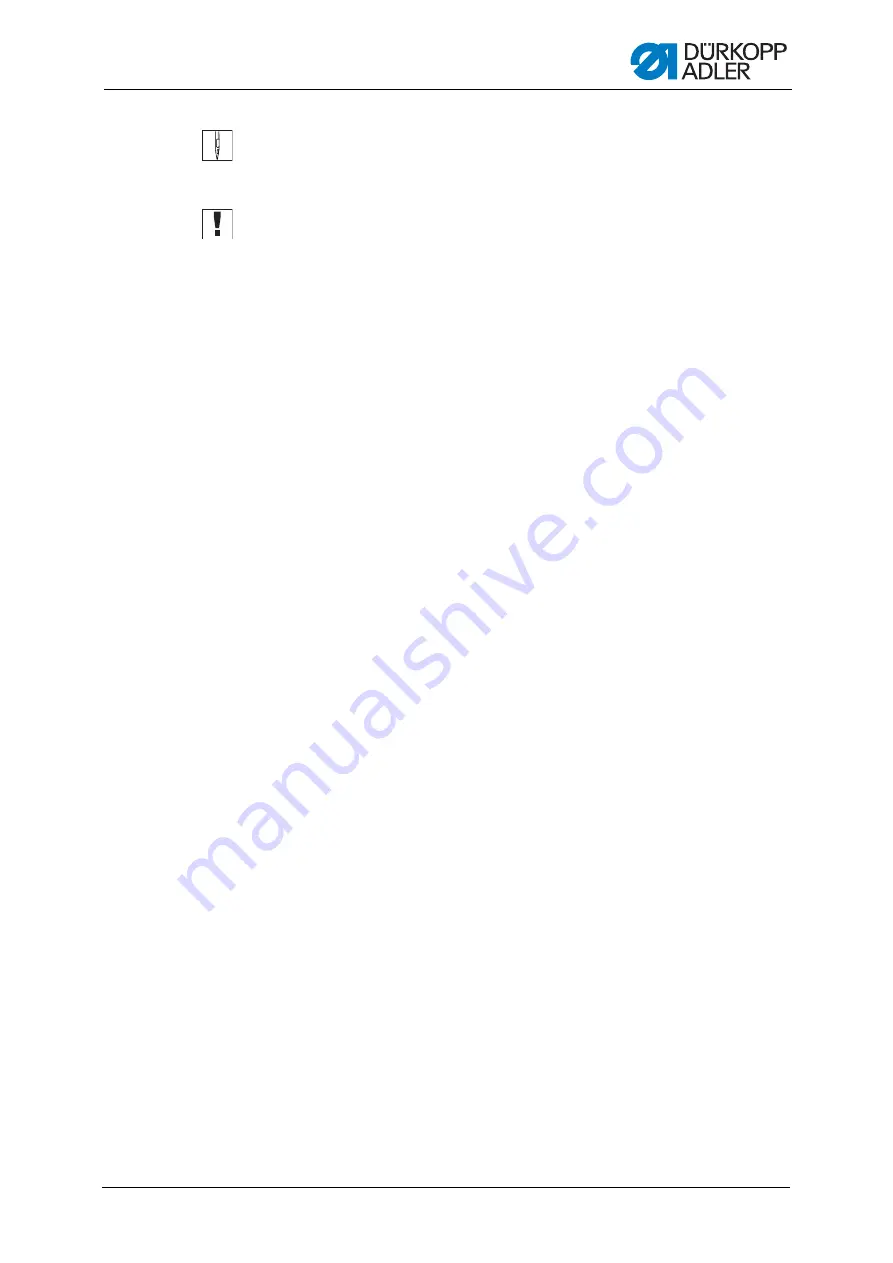
Operation
Operating Instructions 911-211-10 - 00.0 - 10/2020
21
To thread the needle thread:
1.
Place the thread reel on the reel stand and guide the needle thread
through the hole in the guide on the thread guide.
Important
The thread guide must be parallel to the reel stand.
2.
Use compressed air to blow the needle thread through the hose
guide (17).
3.
Feed the needle thread through the guide (16).
4.
Guide the needle thread counterclockwise around the tension (15).
5.
Guide the needle thread clockwise around the tension (14).
6.
Feed the needle thread through guides (13) and (12).
7.
Guide the needle thread clockwise around the deflection (11).
8.
Feed the needle thread under the thread tensioning spring (10), through
the guide (3) and through the needle thread regulator (2) to the thread
lever (1).
9.
Feed the needle thread through the thread lever (1) and the guide (4).
10. Insert the needle thread through the needle thread monitor (5) and,
on a machine with a thread trimmer, through the thread clamp (6).
11. Feed the needle thread through guides (7) and (8).
12. Thread the needle thread through the needle eye (9) in such a way
that the loose thread end faces the hook.
Summary of Contents for 911-211-10
Page 1: ...911 211 10 Operating Instructions...
Page 6: ...Table of Contents 4 Operating Instructions 911 211 10 00 0 10 2020...
Page 10: ...About these instructions 8 Operating Instructions 911 211 10 00 0 10 2020...
Page 34: ...Operation 32 Operating Instructions 911 211 10 00 0 10 2020...
Page 88: ...Programming 86 Operating Instructions 911 211 10 00 0 10 2020...
Page 108: ...Setup 106 Operating Instructions 911 211 10 00 0 10 2020...
Page 110: ...Decommissioning 108 Operating Instructions 911 211 10 00 0 10 2020...
Page 112: ...Disposal 110 Operating Instructions 911 211 10 00 0 10 2020...
Page 133: ......