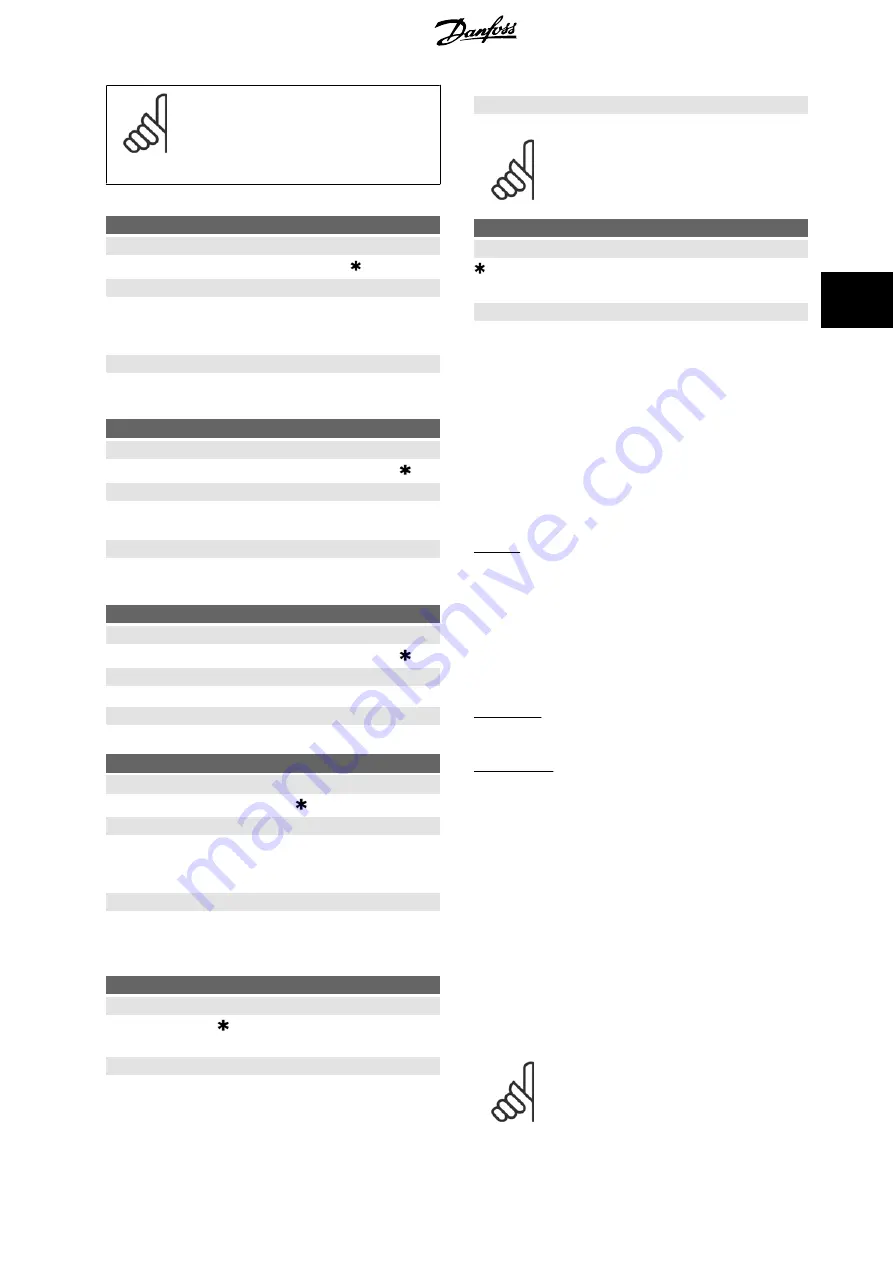
NB!
Please note that if a value set in the nameplate pa-
rameters 102-106 is changed, there will be an auto-
matic change of parameter 108
Stator resistance
and
109
Stator reactance
.
102
Motor power P
M,N
Value:
0.18 - 4 kW
Depends on unit
Function:
Here you must set a power value [kW] P
M,N
, corresponding to the motor's
rated power. The factory sets a rated power value [kW] P
M,N
, that de-
pends on the type of unit.
Description of choice:
Set a value that matches the nameplate data on the motor. Settings be-
tween two sizes below and one size over the factory setting are possible.
103
Motor voltage U
M,N
Value:
50 - 999 V
400 V
Function:
This is where to set the rated motor voltage U
M,N
for either star Y or delta
Δ
.
Description of choice:
Select a value that corresponds to the nameplate data on the motor, re-
gardless of the frequency converter's mains voltage.
104
Motor frequency f
M,N
Value:
24-1000 Hz
50 Hz
Function:
This is where to select the rated motor frequency f
M,N
.
Description of choice:
Select a value that corresponds to the nameplate data on the motor.
105
Motor current I
M,N
Value:
0,01 - I
MAX
Depends on choice of motor
Function:
The nominal, rated current of the motor I
M,N
forms part of the frequency
converter calculation of features such as torque and motor thermal pro-
tection.
Description of choice:
Set a value that corresponds to the nameplate data on the motor. Set the
motor current I
M,N
taking into account whether the motor is star-connec-
ted Y or delta-connected
Δ
.
106
Rated motor speed
Value:
100 - f
M,N
x 60
(max. 60000 rpm)
Depends on parameter 104
Motor frequency,
f
M,N
Function:
This is where to set the value that corresponds to the rated motor speed
n
M,N
that can be seen from the nameplate data.
Description of choice:
Select a value that corresponds to the nameplate data on the motor.
NB!
The max. value equals f
M,N
x 60. f
M,N
to be set in pa-
rameter 104
Motor frequency, f
M,N
.
107
Automatic motor tuning, AMT
Value:
Optimisation off (AMT off)
[0]
Optimisation on (AMT start)
[2]
Function:
Automatic motor tuning is an algorithm that measures stator resistance
R
S
without the motor axle turning. This means that the motor is not de-
livering any torque.
AMT can be used with benefit when initialising units where the user wish-
es to optimise adjustment of the frequency converter to the motor being
used. This is used in particular when the factory setting does not suffi-
ciently cover the motor.
For the best possible tuning of the frequency converter it is recommended
that AMT is performed on a cold motor. It should be noted that repeated
AMT runs can cause heating of the motor, resulting in an increase in the
stator resistance R
S
. As a rule, however, this is not critical.
AMT is performed as follows:
Start AMT:
1.
Give a STOP signal.
2.
Parameter 107
Automatic motor tuning
is set at value [2]
Opti-
misation on
.
3.
A START signal is given and parameter 107
Automatic motor
tuning
is reset to [0] when AMT has been completed.
In factory setting START requires terminals 18 and 27 to be connected
to terminal 12.
Complete AMT:
AMT is completed by giving a RESET signal. Parameter 108
Stator re-
sistance, Rs
is updated with the optimised value.
Interrupting AMT:
AMT can be interrupted during the optimisation procedure by giving a
STOP signal.
When using the AMT function the following points should be observed:
-
For AMT to be able to define the motor parameters as well as
possible, the correct type plate data for the motor connected to
the frequency converter must be keyed into parameters 102 to
106.
-
Alarms will appear in the display if faults arise during tuning of
the motor.
-
As a rule the AMT function will be able to measure the R
S
values
for motors that are 1-2 times larger or smaller than the fre-
quency converter's nominal size.
-
If you wish to interrupt automatic motor tuning, press the
[STOP/RESET] key.
NB!
AMT may not be performed on motors connected in
parallel, nor may setup changes be made while AMT is
running.
VLT
®
Decentral FCD 300 Design Guide
4 Programming
MG.90.S1.02 - VLT
®
is a registered Danfoss trademark
73
4