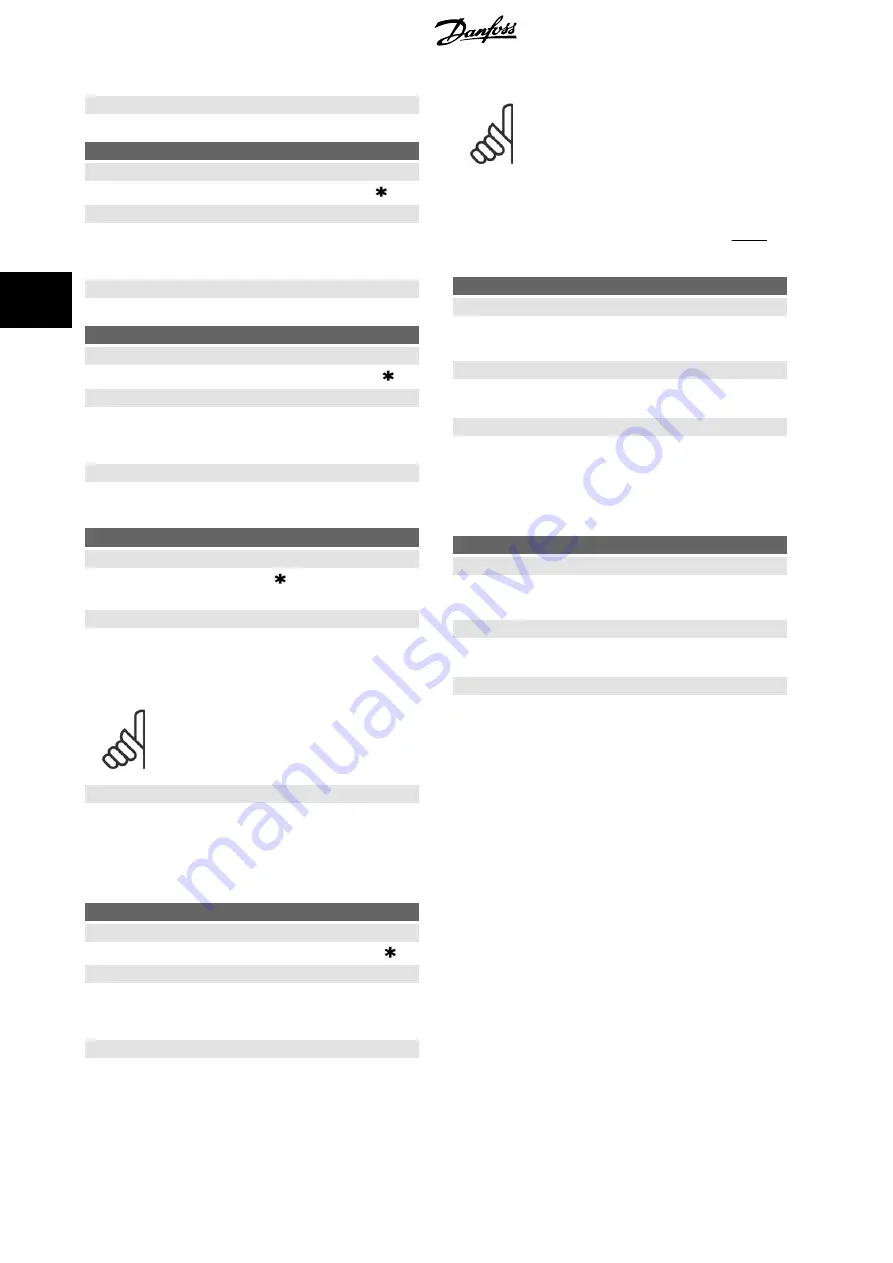
Description of choice:
Set the required frequency.
139
Brake cut in frequency
Value:
0.5 - 132.0/1000.0 Hz
3.0 Hz
Function:
Here you can select the frequency at which the external brake is activa-
ted; this takes place via the output defined in parameter 323
Relay output
1-3
or 341
Digital output terminal 46
(Optionally also 122 and 123).
Description of choice:
Set the required frequency.
140
Current, minimum value
Value:
0 % - 100 % of inverter output current
0 %
Function:
This is where the user selects the minimum motor current running for the
mechanical brake to be released. Current monitoring is only active from
stop until the point when the brake is released.
Description of choice:
This is an extra safety precaution, aimed at guaranteeing that the load is
not lost during start of a lifting/lowering operation.
142
Leakage reactance X
L
Value:
0.000 - XXX,XXX
Ω
Depends on choice of motor
X
L
is sum of rotor and stator leakage reactance.
Function:
After setting of parameters 102-106
Nameplate data
, a number of ad-
justments of various parameter is made automatically, including the
leakage reactance X
L
. The shaft performance can be improved by fine-
tuning the leakage reactance X
L
.
NB!
Parameter 142
The leakage reactance X
L
is normally
not to be changed if the nameplate data have been set,
parameters 102-106.
Description of choice:
X
L
can be set as follows:
1.
The value is stated by the motor supplier.
2.
Use the factory settings of X
L
which the frequency converter it-
self chooses on the basis of the motor nameplate data.
144
Gain AC brake
Value:
1.00 - 1.50
1.30
Function:
This parameter is used to set the AC brake. Using par. 144 it is possible
to adjust the size of the generator torque that can be applied to the motor
without the intermediate circuit voltage exceeding the warning level.
Description of choice:
The value is increased if a greater possible brake torque is required. If
1.0 is selected, this corresponds to the AC brake being inactive.
NB!
If the value in par. 144 is increased, the motor current
will simultaneously increase significantly when gener-
ator loads are applied. The parameter should therefore
only be changed if it is guaranteed during measure-
ment that the motor current in all operating situations
will never exceed the maximum permitted current in
the motor.
Please note
: that the current cannot be
read out from the display.
146
Reset voltage vector
Value:
*Off (OFF)
[0]
Reset (RESET)
[1]
Function:
When the voltage vector is reset it is set to the same starting point each
time a new process commences.
Description of choice:
Select reset (1) when running unique processes each time they arise. This
will enable repetitive precision when stopping to be improved. Select Off
(0) for example for lifting/lowering operations or synchronous motors. It
is an advantage that the motor and the frequency converter are always
synchronized.
147
Motor type
Value:
*General (GENERAL)
[0]
Danfoss Bauer (DANFOSS BAUER)
[1]
Function:
This parameter selects the type of motor connected to the frequency
converter.
Description of choice:
The value can be selected general for most motor brands. Select Danfoss
Bauer for optimal settings for Danfoss Bauer gear motors.
4 Programming
VLT
®
Decentral FCD 300 Design Guide
78
MG.90.S1.02 - VLT
®
is a registered Danfoss trademark
4