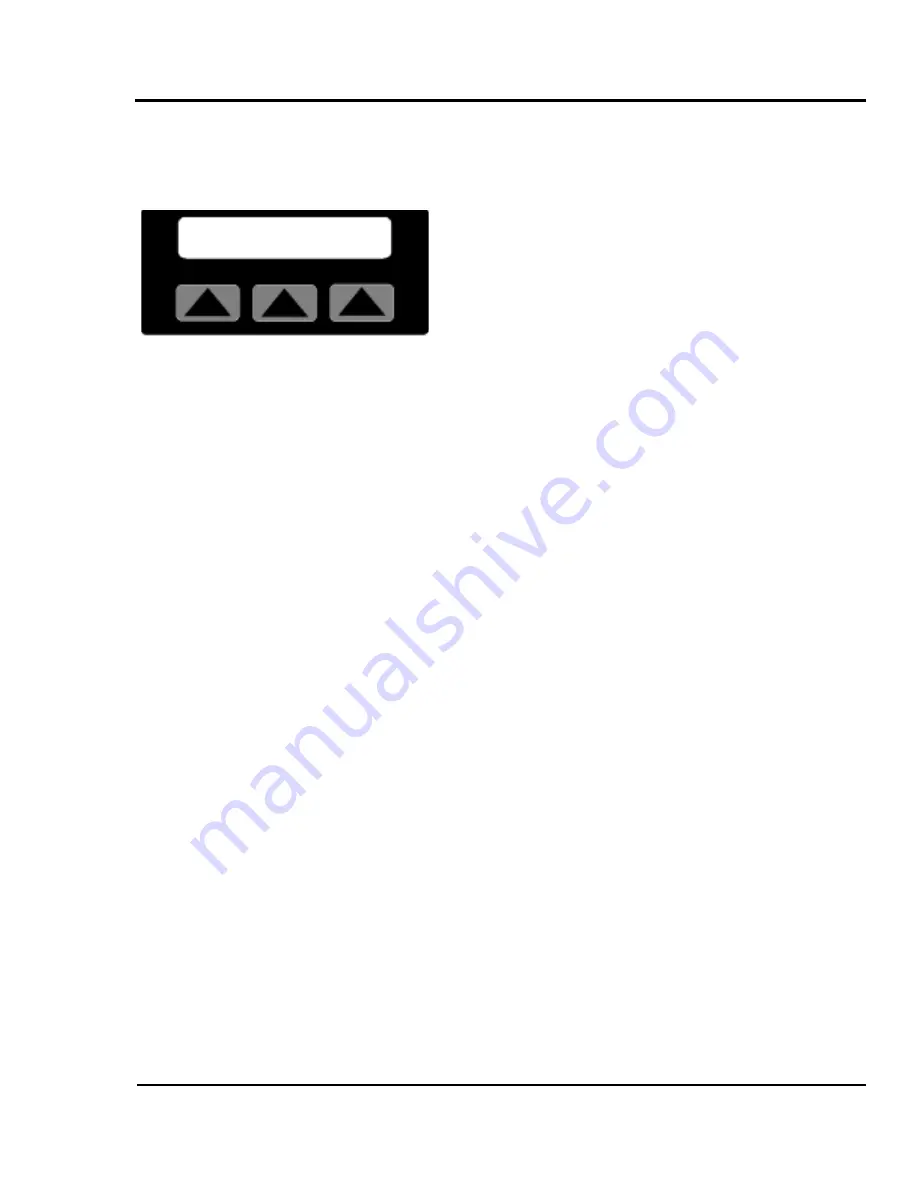
O
PERATION
4-3
UGE048/1103
CSC Combination Puller/Cutter
C
UTTER
O
PERATOR
C
ONTROL
I
NSTRUCTIONS
M
AIN
S
CREEN
MAIN SCREEN
There are two types of main screens, length or time measure-
ment and cuts per minute measurement. The type displayed
varies depending on the current cut mode setting.
See the mode operator display overviews.
The Main Screen has seven features. The top line displays the
active preset (only with multi preset option), cut mode, active
measurement and the unit of measure. The bottom line con-
tains three soft key functions, softkey1/Parts, softkey2/cut
On/Off and softkey3, which varies depending on the current
cut mode setting.
Active Preset
With the multi preset option in on-demand modes the active
preset value changes upon batch completion. As the cutter
sequences through multiple presets, the operator always knows
which preset is being processed.
Active Measurement
The measurement value displayed will be the active length or
time preset or cuts per minute depending on the active cut
mode. It displays the value only when the machine is started
and softkey2 On/Off is on. If the machine is stopped or soft-
key2 On/Off is off, this counter will be forced to zero.
If a negative symbol is shown to the left of the measurement
value, the encoder signal is reversed, i.e. rotating in the wrong
direction. The Cutter will not function while the encoder is
going negative. It is possible to correct this by using the
encoder direction function located in the encoder area of the
maintenance area. See the maintenance area display overview.
Length, Time or Blade Softkey
This key is mode dependent see the mode operator display
overview for the current cut mode.
On/Off Softkey
Under the active measurement in the center of the bottom line
of the display is a soft key labeled On or Off. Pressing this
key while On is displayed will disable the cutter. Likewise
pressing this key while Off is displayed enables the cutter.
Pressing the stop button forces the cut enable off.
Manual cuts can still be made while the cut enable is off.
1 ENC 00000.000 in.
Parts
Off
Length