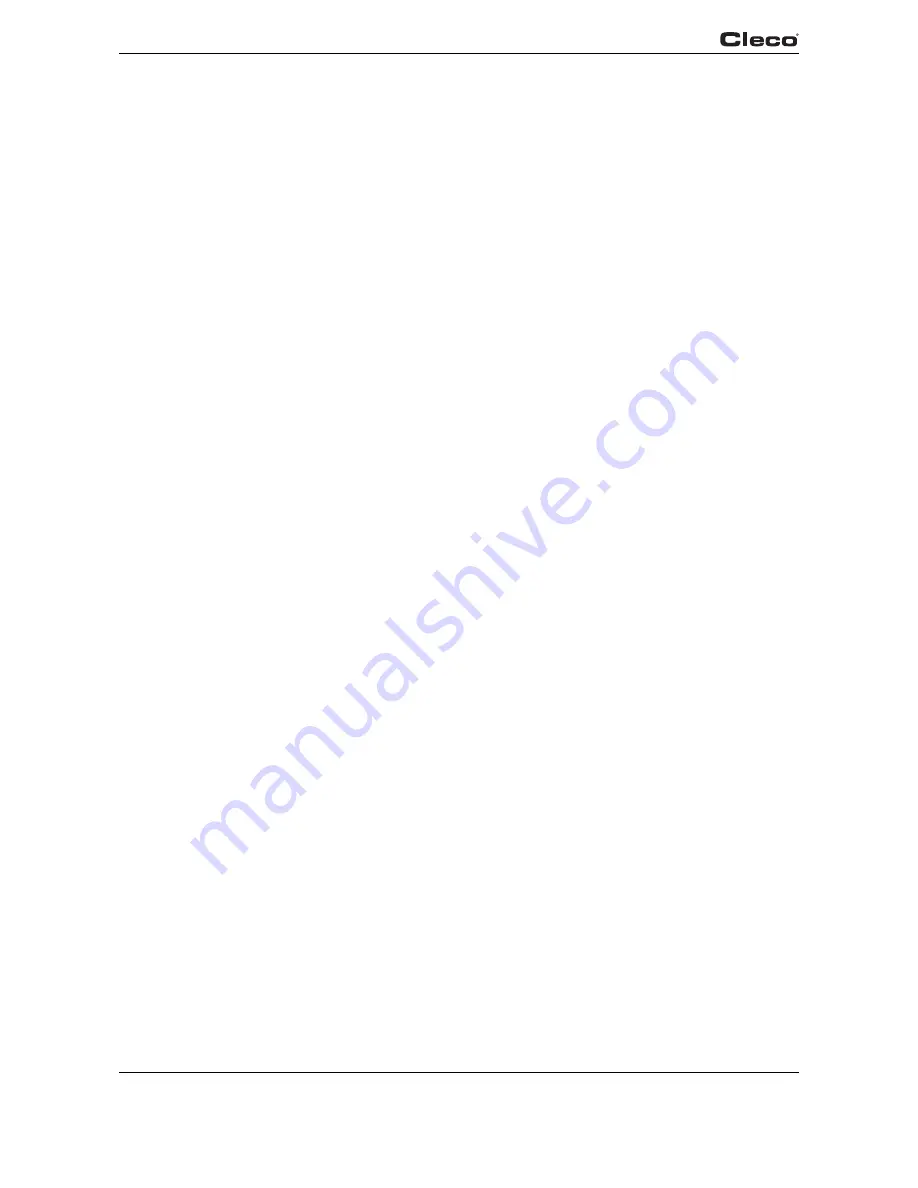
36
PL12EN-1300 2008-03
en03d141.fm, 11.03.2008
Programming
3
Sequence 41
Angle Controlled Back-off with Angle Monitoring
This fastening sequence is generally used to loosen a bolt a specified number of degrees. The
resolver integrated into the nutrunner measures the angle during the untightening. The value is
processed by the control system. When the Turnoff angle is reached the nutrunner is shut off.
Thereafter the final angle is measured during a dwell time and is then processed as the back-off
angle of the bolt together with the evaluation of the untightening in the control system. This value
is displayed on the Run Screen and can be output to a printer or transmitted to other system
components by data communication. In this stage the oscilloscope function is not supported.
The following parameters are programmable in the Standard Application Builder:
• Sequence input value = 41
• Turnoff Angle (deg) = shut-off angle, back-off angle
• Angle High Limit (deg) = maximum angle, high limit for angle reached.
• Angle Low Limit (deg) = minimum angle, low limit for angle reached.
• Speed = max speed of the nutrunner during the back-off stage.
Parameter Name
Range
Typical
Fastening Strategy
Sequence 41
Angle Control in Reverse
Angle Low Limit [Deg]
0 to 9999
90% of Turnoff Angle
Turnoff Angle [Deg]
Low Limit to 9999
As appropriate
Angle High Limit
Turnoff angle to 9999
110% of Turnoff Torque
Speed [RPM]
0 to Tool Max
80% of Tool Max
Backoff Using Reverse Switch (Sequence 41 or Sequence 46)
The Backoff stage is automatically set to Sequence 46 for a tubenut tool and Sequence 41 for all
others. The automatic selection of a tube nut tool depends on a "T" in the tool model number.
That means, if a "T" appears in the model number a tube nut tool is expected. This fastening
sequence is selected when the tool is run in the reverse or untighten direction. It is also automat-
ically used to return a tubenut tool to the home position on every other trigger pull. The resolver
integrated into the nutrunner measures the angle during the untightening. The measured angle
value is processed by the control system. When the Turnoff angle is reached the nutrunner is
shut off. For a tubenut tool, the Turnoff angle is programmed so that the attachment will always
turn far enough to reach the home position and stop based on the torque reaction against the
pawl.
The following parameters are programmable in the Standard Application Builder:
• Speed [rpm] = Max speed of the nutrunner during the backoff stage
Parameter Name
Range
Default
Speed [RPM]
0 to Tool Max
500 or 30% of Tool Max
(tubenut)