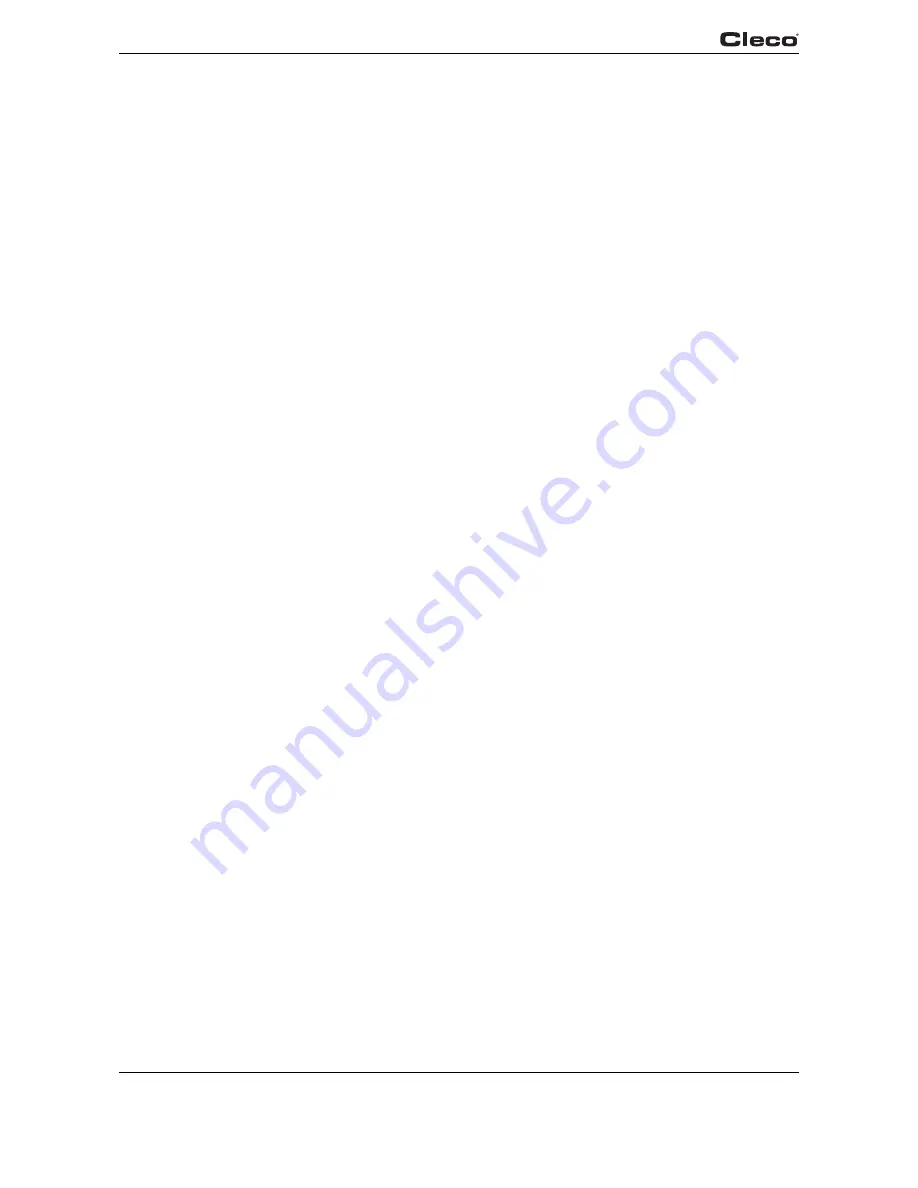
32
PL12EN-1300 2008-03
en03d141.fm, 11.03.2008
Programming
3
The following is a detailed description of each Fastening Sequence:
Sequence 11
High Speed Rundown
This tightening method is generally used as a fast pre-tightening stage. The torque transducer
integrated into the nutrunner measures the torque during the tightening. The value is processed
by the control system. When the defined Turnoff Torque is reached the nutrunner is shut off.
Thereafter the peak torque is measured during a dwell time and is then processed as the tighten-
ing torque of the bolt in the control system. This value is displayed on the Run Screen and can be
output to a printer or transmitted to other system components by data communication. When the
trigger torque is reached the torque curve is recorded and can be viewed and evaluated using
the oscilloscope function.
Sequence 30
Torque Control with Torque and Angle Monitoring
This tightening stage is normally preceded by a fast pre-tightening stage. The transducer inte-
grated into the nutrunner measures the torque and the resolver measures the angle during the
tightening. The values are processed by the control system. When the threshold torque is
reached the angle count starts. When the Turnoff Torque is reached the nutrunner is shut off.
Thereafter the peak torque is measured during a dwell time and is then processed as the tighten-
ing torque of the bolt together with the evaluation of the rundown in the control system. This
value is displayed on the Run Screen and can be output to a printer or transmitted to other sys-
tem components by data communication. When the trigger torque is reached the torque curve is
recorded and can be viewed and evaluated using the oscilloscope function.
Sequence 50
Angle Controlled Tightening with Angle and Torque Monitoring
This tightening sequence is generally preceded by a fast pre-tightening cycle. The transducer
integrated into the nutrunner measures the torque and the resolver measures the angle during
the rundown. The values are processed by the control system. When the Turnoff angle is
reached the nutrunner is shut off. Thereafter the final angle and the peak torque are measured
during a dwell time, and these tightening values for the bolt are then processed together with the
evaluation of the rundown in the control system. These values are displayed on the Run Screen
and can be output to a printer or transmitted to other system components by data communica-
tion. When the trigger torque is reached the torque curve is recorded and can be viewed and
evaluated using the oscilloscope function.
Sequence 41
Angle Controlled Back-off with Angle Monitoring
This fastening sequence is generally used to loosen a bolt a specified number of degrees. The
resolver integrated into the nutrunner measures the angle during the untightening. The value is
processed by the control system. When the Turnoff angle is reached the nutrunner is shut off.
Thereafter the final angle is measured during a dwell time and is then processed as the back-off
angle of the bolt together with the evaluation of the untightening in the control system. This value
is displayed on the Run Screen and can be output to a printer or transmitted to other system
components by data communication. In this stage the oscilloscope function is not supported.
Sequence 41 or Sequence 46
Backoff using Reverse switch/Relax
The Backoff stage is automatically set to Sequence 46 for a tubenut tool and Sequence 41 for all
others. The automatic selection of a tube nut tool depends on a 'T' in the tool model number. That
means, if a 'T' appears in the model number a tube nut tool is expected. This fastening sequence
is selected when the tool is run in the reverse or untighten direction. It is also used to return a