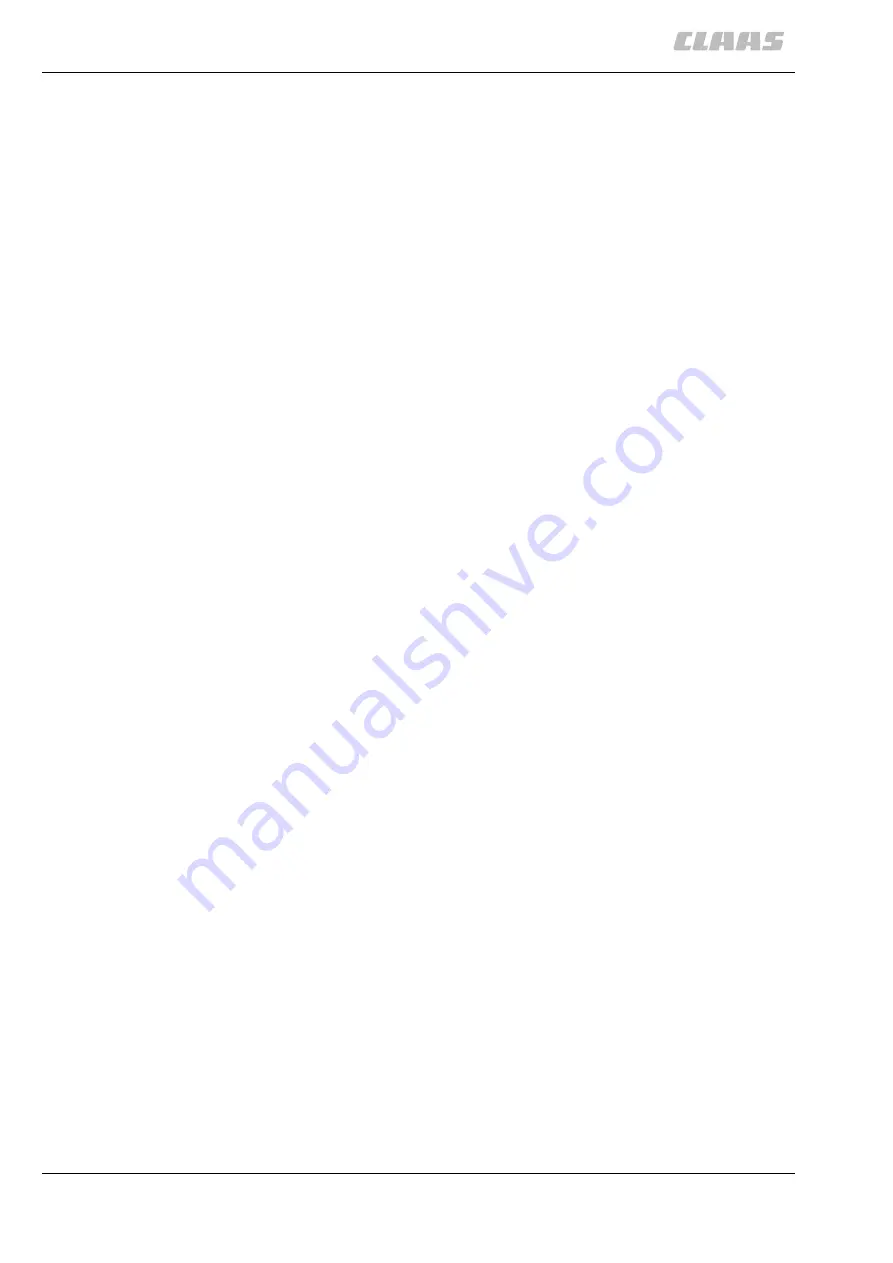
1.3.2
General repair information
Always tighten self-locking bolts with microencapsu-
lated adhesive rapidly to the specified tightening
torque. When removing these bolts, quickly unscrew
them completely. These self-locking bolts must
not
come into contact with sealing compound (e.g.
“Epple 33” or similar products).
In individual cases, bolts with liquid locking compound
can be used instead of self-locking bolts only where
these bolts can be heated up to approx. 200 °C for
removing them. Ensure that the specified quality grade
of bolts (8.8/10.9 or similar grades) is observed here
as well.
Self-locking bolts with microencapsulated adhesive
may be used only where operating temperatures will
not 90 °C max.
These bolts can be subjected to full stress after
24 hours at +20 °C. To speed up the curing time,
heating may be applied (e.g. to 15 minutes at +70 °C).
Liquid locking compound
(e.g. Delo-ML 187 / Loctite 242 or similar types)
Use liquid locking compound only where specified by
the manufacturer.
Correct application:
Metal surfaces where liquid locking compound is to be
applied must be absolutely free from grease. Use the
“Activator” included in the workshop package for
cleaning.
Before applying the liquid locking compound, the metal
surfaces where Activator has been applied must have
dried. Especially in blind holes, no Activator (cleaning
agent) residues are allowed.
When installing bolts, apply the liquid locking
compound only to the internal thread (nut) if possible in
small quantities (drops). In blind holes only wet
approx. 1d (d = nominal diameter of bolt) at the thread
bottom. The same applies to any extra-long female
threads. When applying the liquid locking compound to
the bolt or at the top end of a female thread, the liquid
locking compound will spread over the entire thread
length when screwing the bolt in. As a result, too much
break-away torque is required to remove the bolt –
Danger of breaking!
Threaded assemblies secured with liquid locking
compound can be easily unscrewed by heating them
up to approx. 200 °C.
Correct installation of lock collar bearings
Lock collar bearings are tightened on the shaft by
rotating the eccentric ring over the inside bearing ring.
Prior to installation, apply semi-fluid lubricant of
NLGI class 00 (e.g. CLAAS semi-fluid lubricant EP 00)
to the inside ring and the shaft to make bearing
removal easier during future repairs.
Always fasten the eccentric ring moderately in the
direction of rotation of the shaft and lock by means of a
set screw. To remove the bearing, loosen the eccentric
ring in opposite direction of rotation of the shaft.
Correct installation of adapter sleeve bearings
Adapter sleeve bearings do not require a specially
machined bearing seat. They may be mounted on any
drawn or scalped shaft. This is an advantage because
it allows the shaft to be axially moved as required to
obtain correct alignment.
Always install adapter sleeve bearings according to
the conical inside ring. Clean the taper lock adapter
sleeve and the shaft and check that the sleeve nut
runs easily so the taper lock adapter sleeve will not
turn on the shaft when tightening.
Tightening the bearing:
First tighten the sleeve nut to the point where the taper
lock adapter sleeve has no more play and is under
slight preload. Now tighten the nut by approx. 90° and
continue turning until the next nearest slot fits the tab.
Secure sleeve nut with the tab.
Loosening the bearing:
Bend up the tab which secures the sleeve nut and first
back off the nut a few turns only (the thread must still
fully grip). Loosen the taper lock adapter sleeve with a
sharp blow, using a block-ended tube.
Ferrule fittings on hydraulic lines
When pre-assembling the unit and for pre-assembled
factory-delivered ferrule fittings, the following applies:
installation is in the associated, well-oiled threaded
joint with half a turn of the union nut beyond the point
where resistance is felt.
Pre-assembly:
1. Cut off the tube at right angles. Do not use a pipe
cutter! This will slant the tube wall, causing heavy
inside and outside burrs. Slightly deburr the tube
end on the inside and outside (do not chamfer!)
and clean it. In case of tube bends, the straight
tube end up to where the bending radius starts
must be at least twice the height of the union nut.
2. Push the union nut and the ferrule on the tube.
3. Push the tube against the stop in the union and
tighten union nut until the ferrule grips the tube
(the tube must not rotate with the nut). This point
can be felt because increase power is needed
from here.
Summary of Contents for LEXION 480
Page 1: ...REPAIR MANUAL LEXION 480...
Page 2: ...R e a d a n d f o l l o w s a f e t y i n s t r u c t i o n s...
Page 14: ...0 1 12 RHB LEXION 480 188 678 1 Contents...
Page 15: ...1 General information...
Page 16: ......
Page 20: ...1 1 4 RHB LEXION 480 188 678 1 General...
Page 24: ...1 2 4 RHB LEXION 480 188 678 1 Safety Rules...
Page 38: ...1 6 4 RHB LEXION 480 188 678 1 Sectional view of machine...
Page 41: ...2 Operator s platform...
Page 42: ......
Page 74: ...2 1 32 RHB LEXION 480 188 678 1 Air conditioner...
Page 98: ...2 5 2 RHB LEXION 480 188 678 1 Engine electric system...
Page 99: ...3 Threshing mechanism...
Page 100: ......
Page 138: ...3 1 38 RHB LEXION 480 188 678 1 Feed rake conveyor...
Page 238: ...3 6 24 RHB LEXION 480 188 678 1 Axial rotors...
Page 239: ...4 Cleaning unit...
Page 240: ......
Page 246: ...4 1 6 RHB LEXION 480 188 678 1 Return pan...
Page 295: ...5 Grain delivery...
Page 296: ......
Page 373: ...6 Straw discharge...
Page 374: ......
Page 390: ...6 1 16 RHB LEXION 480 188 678 1 Straw chopper...
Page 397: ...188 678 1 RHB LEXION 480 6 2 7 Uni spreader 23...
Page 402: ...6 2 12 RHB LEXION 480 188 678 1 Uni spreader...
Page 403: ...7 Drives...
Page 404: ......
Page 408: ...7 1 4 RHB LEXION 480 188 678 1 Drive diagram...
Page 444: ...7 2 36 RHB LEXION 480 188 678 1 Left hand drive belts...
Page 542: ...7 4 66 RHB LEXION 480 188 678 1 Cutterbar drive...
Page 556: ...7 5 14 RHB LEXION 480 188 678 1 Left hand threshing mechanism drive...
Page 580: ...7 6 24 RHB LEXION 480 188 678 1 Right hand threshing mechanism drive...
Page 594: ...7 7 14 RHB LEXION 480 188 678 1 Threshing drum reduction gearbox...
Page 634: ...7 11 12 RHB LEXION 480 188 678 1 Straw spreader drive...
Page 644: ...7 13 8 RHB LEXION 480 188 678 1 Sieve pan drive...
Page 708: ...7 15 22 RHB LEXION 480 188 678 1 Axial rotor drive...
Page 730: ...7 16 22 RHB LEXION 480 188 678 1 Engine output...
Page 736: ...7 17 6 RHB LEXION 480 188 678 1 Rotary screen drive...
Page 766: ...7 18 30 RHB LEXION 480 188 678 1 Final drives...
Page 818: ...7 21 20 RHB LEXION 480 188 678 1 Steering axle...
Page 819: ...8 Machine body...
Page 820: ......
Page 839: ...9 Hydraulic system...
Page 840: ......
Page 848: ...9 2 4 RHB LEXION 480 188 678 1 Maintenance...
Page 866: ...9 4 10 RHB LEXION 480 188 678 1 Hydrostatic fixed displacement motors...
Page 902: ...9 5 36 RHB LEXION 480 188 678 1 Hydraulic cylinders High pressure hydraulic circuit...
Page 981: ...10 Engine...
Page 982: ......
Page 1003: ...11 Index...
Page 1004: ......
Page 1016: ...11 1 12 RHB LEXION 480 188 678 1 Index...