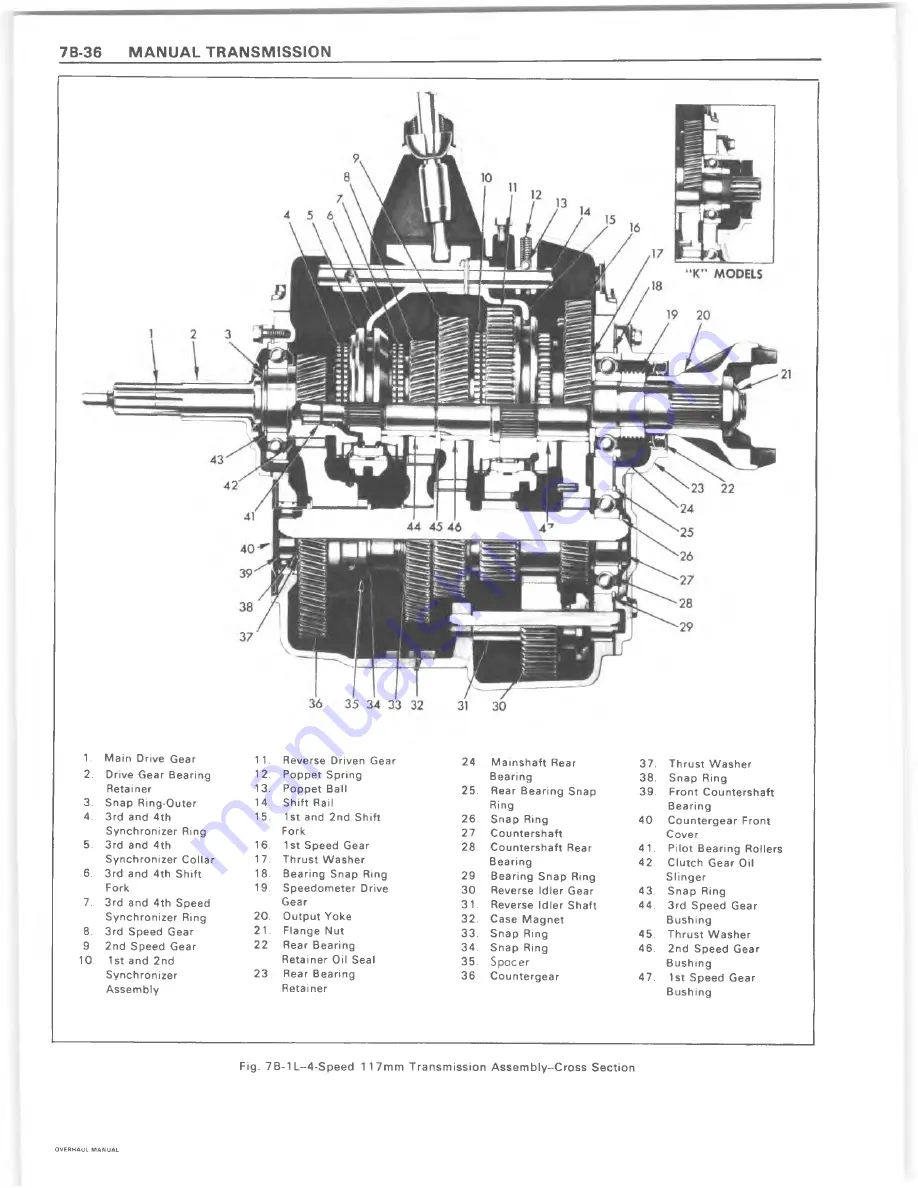
7B-36
M A N U A L T R A N S M IS S IO N
1
.
M a in D riv e G e a r
1
1
.
R e v e rs e D riv e n G e a r
2
.
D riv e G e a r B e a r in g
1 2
.
P o p p e t S p r in g
R e ta in e r
1 3 .
P o p p e t B a ll
3.
S n a p R in g -O u te r
1 4 .
S h ift R ail
4.
3 r d a n d 4 th
1 5 .
1st a n d 2 n d S h ift
S y n c h r o n iz e r R in g
F o rk
5.
3 r d a n d 4 th
1 6 .
1 st S p e e d G e a r
S y n c h r o n iz e r C o lla r
1 7 .
T h r u s t W a s h e r
6
.
3 r d a n d 4 th S h ift
1 8 .
B e a r in g S n a p R in g
F o rk
1 9 .
S p e e d o m e te r D riv e
7.
3 r d a n d 4 th S p e e d
G e a r
S y n c h r o n iz e r R in g
2 0
.
O u tp u t Y o k e
8
.
3 r d S p e e d G e a r
2 1
.
F la n g e N u t
9.
2 n d S p e e d G e a r
2 2
R e a r B e a r in g
10
.
1
st a n d
2
nd
R e ta in e r O il S e a l
S y n c h r o n iz e r
2 3
R e a r B e a r in g
A s s e m b ly
R e ta in e r
2 4
M a in s h a f t R e a r
3 7 .
T h r u s t W a s h e r
B e a r in g
3 8 .
S n a p R in g
2 5 .
R e a r B e a r in g S n a p
3 9 .
F r o n t C o u n te r s h a ft
R ing
B e a r in g
2 6
S n a p R in g
4 0
C o u n t e r g e a r F ro n t
2 7
C o u n te r s h a ft
C o v e r
2 8
C o u n t e r s h a f t R e a r
4 1 .
P ilo t B e a r in g R o lle rs
B e a r in g
4 2 .
C lu tc h G e a r O il
2 9
B e a r in g S n a p R in g
S lin g e r
3 0
R e v e rs e Id le r G e a r
4 3 .
S n a p R in g
3 1 .
R e v e rs e Id le r S h a ft
4 4 .
3 r d S p e e d G e a r
3 2 .
C a s e M a g n e t
B u s h in g
3 3 .
S n a p R in g
4 5 .
T h r u s t W a s h e r
3 4 .
S n a p R in g
4 6 .
2 n d S p e e d G e a r
3 5 .
S p a c e r
B u s h in g
3 6
C o u n t e r g e a r
4 7 .
1 st S p e e d G e a r
B u s h in g
Fig. 7B-1 L--4-Speed 1 17mm T ransm ission A sse m b ly-C ro ss S ection
O V E R H A U L M A N U A L
Summary of Contents for 1977 Monte Carlo
Page 1: ...CHEVROLET ST 333 80...
Page 4: ......
Page 6: ......
Page 50: ......
Page 70: ......
Page 100: ...4B 32 REAR AXLE DIFFERENTIAL Fig 24F lnstalling Pinion Flange OVERHAUL M AN U AL...
Page 126: ......
Page 136: ......
Page 142: ...5 6 BRAKES Fig 5 1 1A Gaging Piston Rod OVERHAUL M AN U AL...
Page 168: ......
Page 248: ......
Page 402: ...7C 6 CLUTCHES Fig 7 C 1 2 E D e p r e s s in g L ever Fig 7 C 1 4 E S ta k in g N u t...
Page 404: ......
Page 414: ......
Page 420: ......
Page 421: ......
Page 422: ......
Page 423: ......
Page 424: ......
Page 427: ......
Page 428: ......