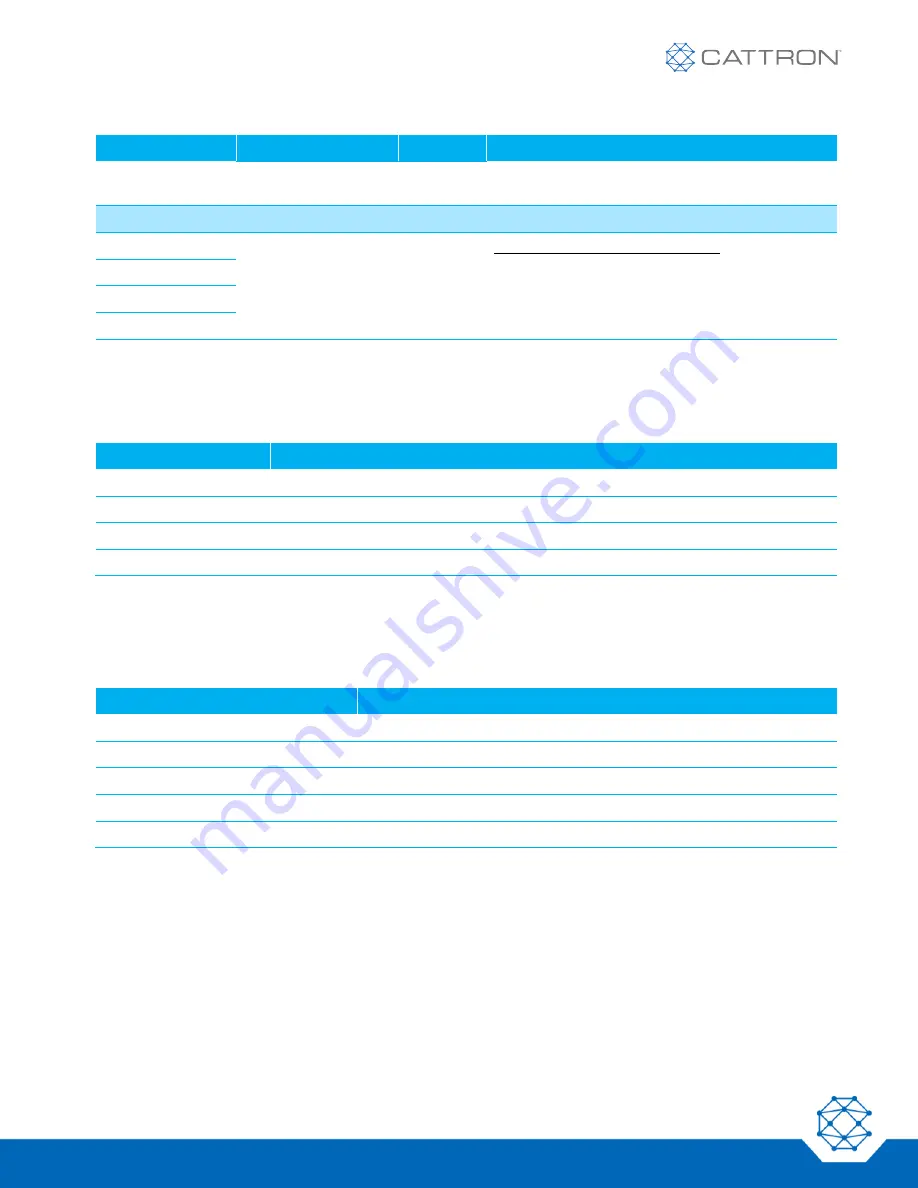
DynaGen
TM
TOUGH Series
TM
TE410 - EN
User Manual
79
9M02-9249-A001-EN
Revision A
Name
Range
Default
Description
Setpoints > High
Failure
(Only applies if Func. Select is set to Fault
Monitor.) Reading at which a failure occurs.
Timers > Trigger Delays Aux Sensors menu:
Aux 1
1 to 45 s
in 1 s increments
5 s
Func. Select is set to fault monitor: Sets the
amount of time to ignore the input for warning and
failure detection purposes. No warnings or failures
will be generated during this time.
Does not apply to other Func. Select modes.
Aux 2
Aux 3
Aux 4
* 1 ~ 600 min for firmware versions below 1.78.
If using
Output on Low
or
Output on High
, one of the switched outputs events must be set to one of the following,
corresponding to the Auxiliary Sensor being configured per the following table.
(Switched I/O > Switched Out A/B/C/D/E/F > Events menus)
Name
Description
Aux Sensor 1
Used by the Auxiliary Sensor 1
Output on Low
or
Output on High
feature.
Aux Sensor 2
Used by the Auxiliary Sensor 2
Output on Low
or
Output on High
feature.
Aux Sensor 3
Used by the Auxiliary Sensor 3
Output on Low
or
Output on High
feature.
Aux Sensor 4
Used by the Auxiliary Sensor 4
Output on Low
or
Output on High
feature.
The display resolution of the auxiliary sensors that are displayed on the screen are different than the resolution
used for the purpose of the comparisons that determine if the start level, stop level, low warning, etc., are in
effect. The resolutions are given in the following table.
Sensor Unit Type
Comparison Resolution
Temperature
1 °F
Pressure
1 PSI
Level
1%
Voltage
0.1 V
Current
1 A
Example:
If the Auxiliary Sensor 1 (Aux 1) is using a temperature sender curve, set to Output on Low, and the
Start Level is set to 130 °F, then the Output will not turn on until the temperature drops to 129 °F since the
resolution for comparisons is 1 °F.
The following tables gives all the possible actions that the auxiliary sensors can perform.
Summary of Contents for DYNAGEN TOUGH Series TE410
Page 1: ...TOUGH SeriesTM TE410 User Manual ...
Page 22: ...DynaGenTM TOUGH SeriesTM TE410 EN User Manual 22 9M02 9249 A001 EN Revision A CT Wiring ...
Page 24: ...DynaGenTM TOUGH SeriesTM TE410 EN User Manual 24 9M02 9249 A001 EN Revision A ...
Page 28: ...DynaGenTM TOUGH SeriesTM TE410 EN User Manual 28 9M02 9249 A001 EN Revision A ...