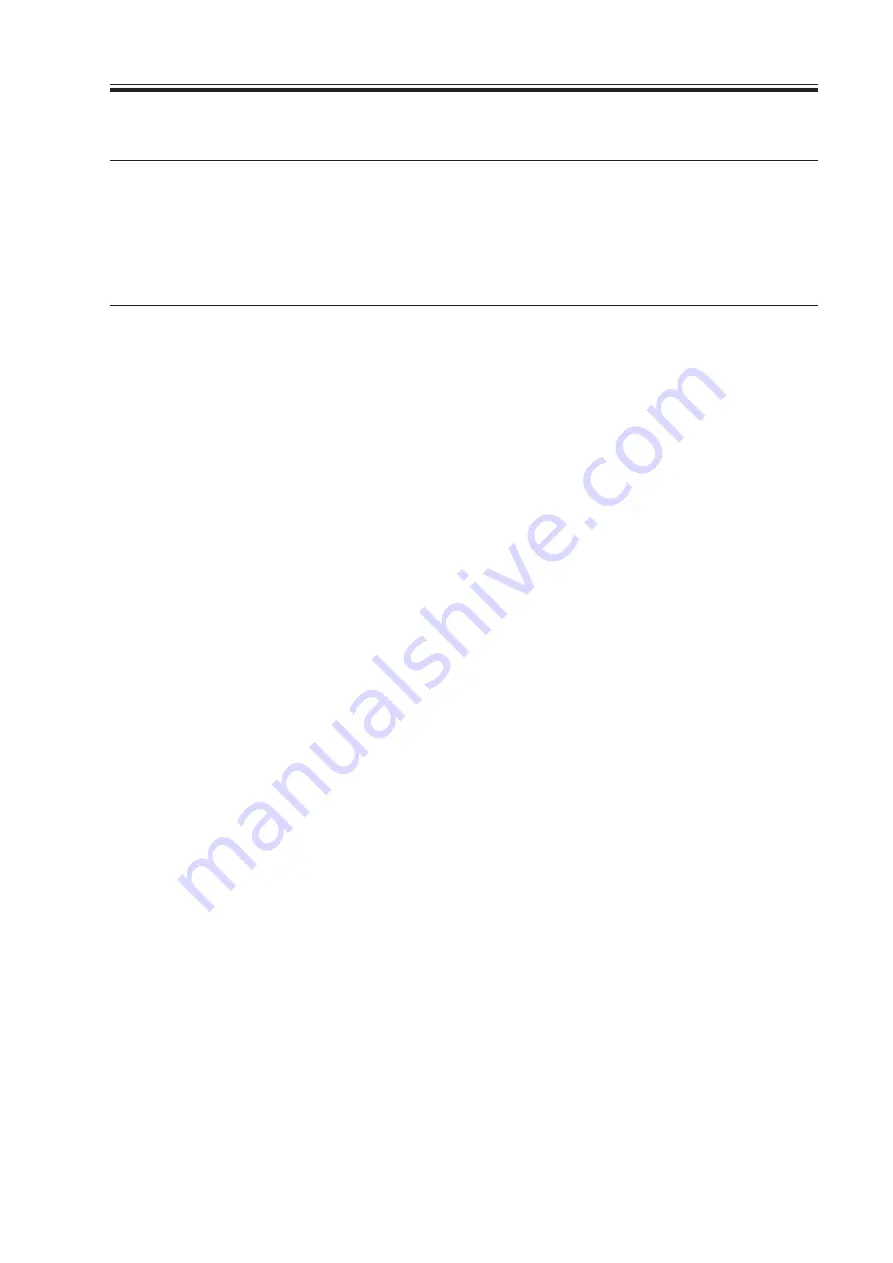
COPYRIGHT © 2000 CANON INC.
2000 2000 2000 2000
CANON iR5000/iR6000 REV.0 JULY 2000
CHAPTER 4 IMAGE FORMATION SYSTEM
4-1 P
1. Outline of Processes
1.1 Outline
The functions and methods used in the machine's image formation system are as follows:
Item
Photosensitive drum
Developing assembly
Pre-exposure
Potential sensor
Wire auto cleaning
Primary charging control
Grid bias control
Developing bias control
Dust-collecting roller bias
control
Pre-transfer charging con-
trol
Transfer charging control
Separation charging control
Function/method
Amorphous silicon (80-mm dia.)
Cleaning method: blade
Developing cylinder (24.5-mm dia.)
Developing method: dry, 1-component, toner projection
Toner: magnetic, negative
Array of 63 LEDs
Turning on/off the Pre-exposure LED Array.
Potential Control
[1] Setting the primary current
[2] Setting the laser output
[3] Setting the developing bias (DC)
[1] Primary charging wire
[2] Pre-transfer charging wire
[3] Transfer charging wire
[4] Separation charging wire
DC constant current control: set by potential control
DC constant voltage control: fixed by varistor
Control value: 850 V (approx.)
AC constant voltage control: on/off control only
Voltage: 1500 Vp-p (approx.)
Frequency: 2.7 kHz (approx.)
DC constant voltage control: set by potential control
Control value: 0 to 600 V (approx.)
DC non-control
Voltage: -1000 V (approx.)
AC constant voltage control: fuzzy by environment sensor
DC constant current control: on/off control only
DC current control: fuzzy control by environment sensor
AC constant voltage control
DC constant current control: fuzzy control by environment
sensor and to suit density of original (drum surface potential)
T04-101-01
Download Free Service Manual at http://printer1.blogspot.com
Summary of Contents for IR5000 - iR B/W Laser
Page 10: ...Download Free Service Manual at http printer1 blogspot com ...
Page 14: ...Download Free Service Manual at http printer1 blogspot com ...
Page 46: ...Download Free Service Manual at http printer1 blogspot com ...
Page 64: ...Download Free Service Manual at http printer1 blogspot com ...
Page 92: ...Download Free Service Manual at http printer1 blogspot com ...
Page 94: ...Download Free Service Manual at http printer1 blogspot com ...
Page 98: ...Download Free Service Manual at http printer1 blogspot com ...
Page 106: ...Download Free Service Manual at http printer1 blogspot com ...
Page 136: ...Download Free Service Manual at http printer1 blogspot com ...
Page 138: ...Download Free Service Manual at http printer1 blogspot com ...
Page 154: ...Download Free Service Manual at http printer1 blogspot com ...
Page 166: ...Download Free Service Manual at http printer1 blogspot com ...
Page 176: ...Download Free Service Manual at http printer1 blogspot com ...
Page 198: ...Download Free Service Manual at http printer1 blogspot com ...
Page 213: ...Download Free Service Manual at http printer1 blogspot com ...
Page 299: ...Download Free Service Manual at http printer1 blogspot com ...
Page 379: ...Download Free Service Manual at http printer1 blogspot com ...
Page 381: ...Download Free Service Manual at http printer1 blogspot com ...
Page 425: ...Download Free Service Manual at http printer1 blogspot com ...
Page 473: ...Download Free Service Manual at http printer1 blogspot com ...
Page 475: ...Download Free Service Manual at http printer1 blogspot com ...
Page 521: ...Download Free Service Manual at http printer1 blogspot com ...
Page 535: ...Download Free Service Manual at http printer1 blogspot com ...
Page 543: ...Download Free Service Manual at http printer1 blogspot com ...
Page 557: ...Download Free Service Manual at http printer1 blogspot com ...
Page 559: ...Download Free Service Manual at http printer1 blogspot com ...
Page 565: ...Download Free Service Manual at http printer1 blogspot com ...
Page 613: ...Download Free Service Manual at http printer1 blogspot com ...
Page 616: ...Download Free Service Manual at http printer1 blogspot com ...
Page 691: ...Download Free Service Manual at http printer1 blogspot com ...
Page 693: ...Download Free Service Manual at http printer1 blogspot com ...
Page 797: ...Download Free Service Manual at http printer1 blogspot com ...
Page 819: ...Download Free Service Manual at http printer1 blogspot com ...
Page 821: ...Download Free Service Manual at http printer1 blogspot com ...
Page 831: ......
Page 837: ......