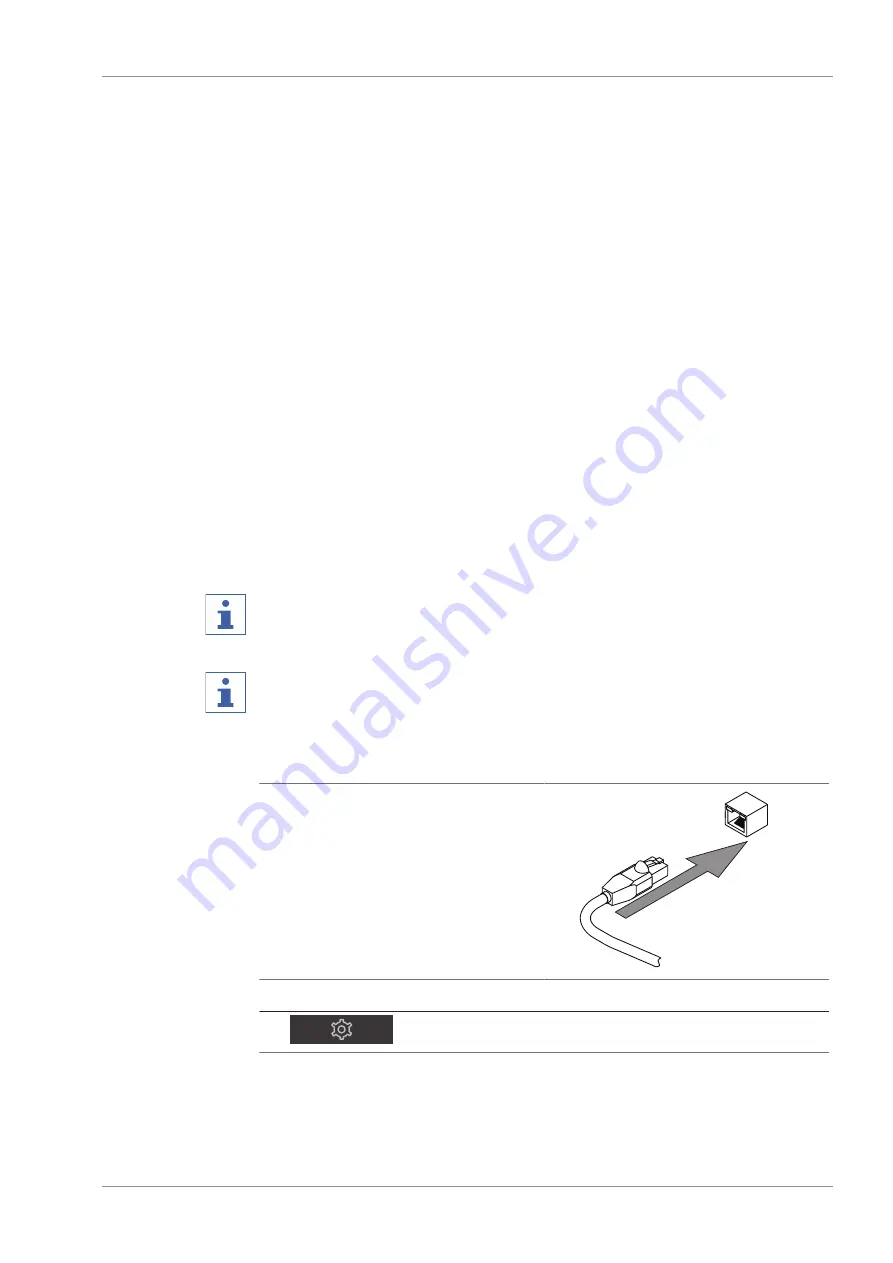
BÜCHI Labortechnik AG
Installation | 5
Operation Manual Interface I-300 Pro
35/102
The laboratory equipment to be evacuated is connected to the vacuum pump and the
VacuBox by means of vacuum tubing. See Chapter 5.2.5 "Overview: setting up vac-
uum tubing connections", page 37.
5.2.1
Connecting communication cables to interface unit
The communication connections between the Interface I-300 Pro, the VacuBox and
the other BUCHI laboratory equipment are established using the standard BUCHI
communication cable (green cable). The corresponding connection sockets are on
the rear panels of the devices and are marked "COM" for identification. Details of the
precise positions of the connection sockets are provided in the operating instructions
for the devices.
For connection options on the Interface I-300 Pro see Chapter 3.5.2 "Rear view",
page 15.
For connection options on the VacuBox see Chapter 3.5.3 "VacuBox (connec-
tions)", page 16.
5.2.2
Establishing LAN connection
Requirements for local network settings
u
The following port has to be enabled in the firewall settings on the internet gate-
way:
TCP (HTTPS) traffics through remote port 443
u
In order to use the BUCHI Cloud a DNS server must be configured on the instru-
ment.
NOTE
If there is no DNS server available enter the IP address for the BUCHI Cloud connec-
tion manually.
NOTE
If there is no DHCP server available enter the IP address, gateway subnet mask and
DNS server manually.
Preparing the instrument for app using
NOTICE! Do not unplug the LAN cable
while the unit is connected to the
BUCHI Cloud Services.
u
Connect the unit to the LAN (local
area network).
u
Restart the unit.
Navigation path
➔
➔
[Settings]
➔
[Network]
u
Navigate to
[Network]
.