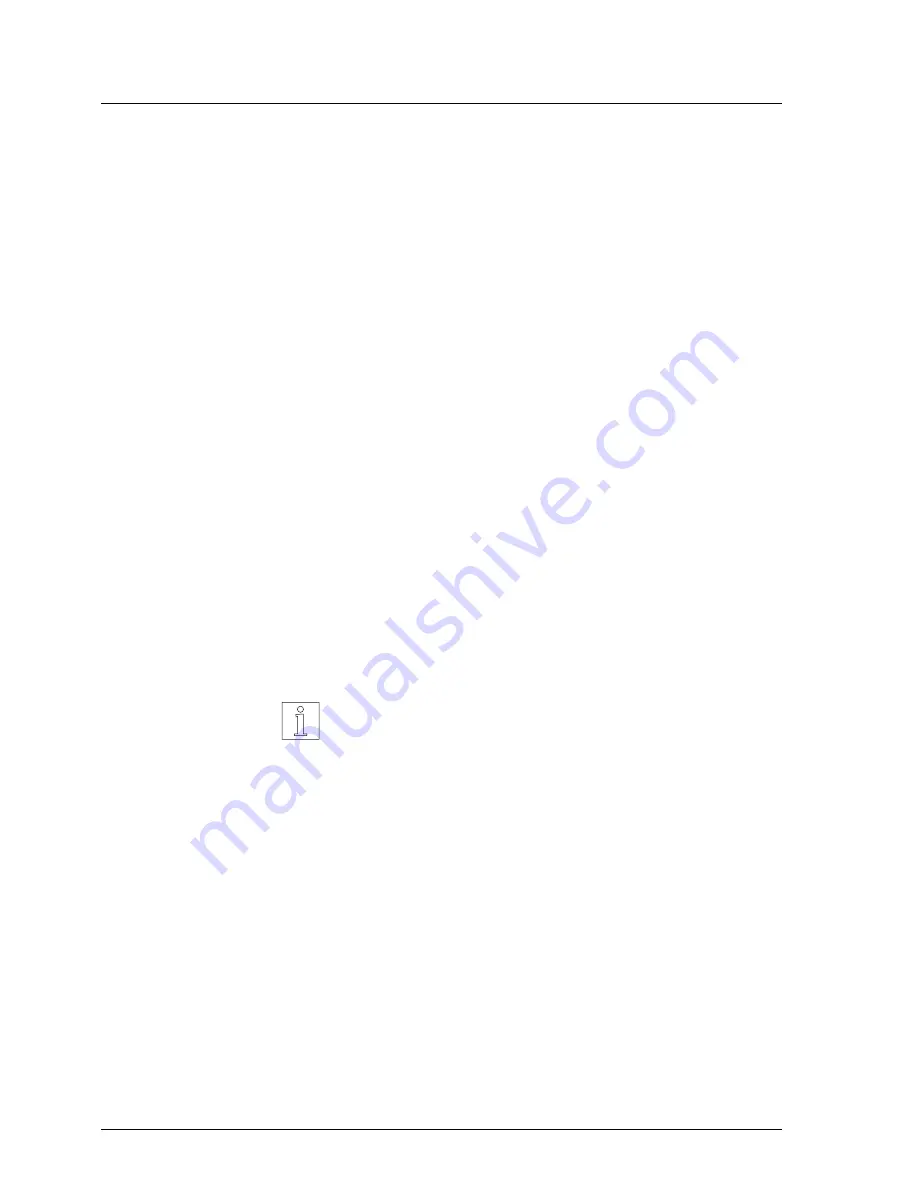
All field bus interfaces are opto-isolated and have an internal leakage
resistance towards ground of 1 Mohm.
Field bus interfaces
Interbus-S slave interface (IBS option)
Two-line remote bus
4 data words
Transmission rate
500 kbauds
Distance to adjacent station
400 m max.
Profibus-DP slave interface (PBDP option)
The transmission rate is set by the master (12 Mbauds max.).
Line length
see Profibus-DP specifications
CAN-Bus interface (CAN option)
Transmission rate
10 kbauds to 500 kbauds
Line length
at 10 kbauds
7000 m max.
at 125 kbauds
570 m max.
at 500 kbauds
80 m max.
SUCONET slave interface (RS 485 HS option)
Bus interface
RS 485 HS
Bus cable
Shielded twisted-pair cable
Transmission speed
187.5 kbauds and 375 kbauds
NOTE
The BERGER LAHR controller automatically adjusts to the baud rate
of the master; it is therefore not necessary to set it on the unit.
ANOZ (option)
Analog interface
Internal leakage resistance towards ground
1 Mohm
Electrical characteristics of the analog input
1 signal input, opto-isolated
±
10 V
Precision
±
0.25%,
±
25 mV
A/D converter resolution
3700 steps min.
Input resistance
>10 kohms
Electrical characteristics of the analog output
1 signal output, opto-isolated,
10 V
short-circuit protected
(30 mA max.)
Precision
±
0.5%,
±
50 mV
D/A converter resolution
200 steps min.
General description
1-14
WDP3-01X Ident. no.: 00441109760