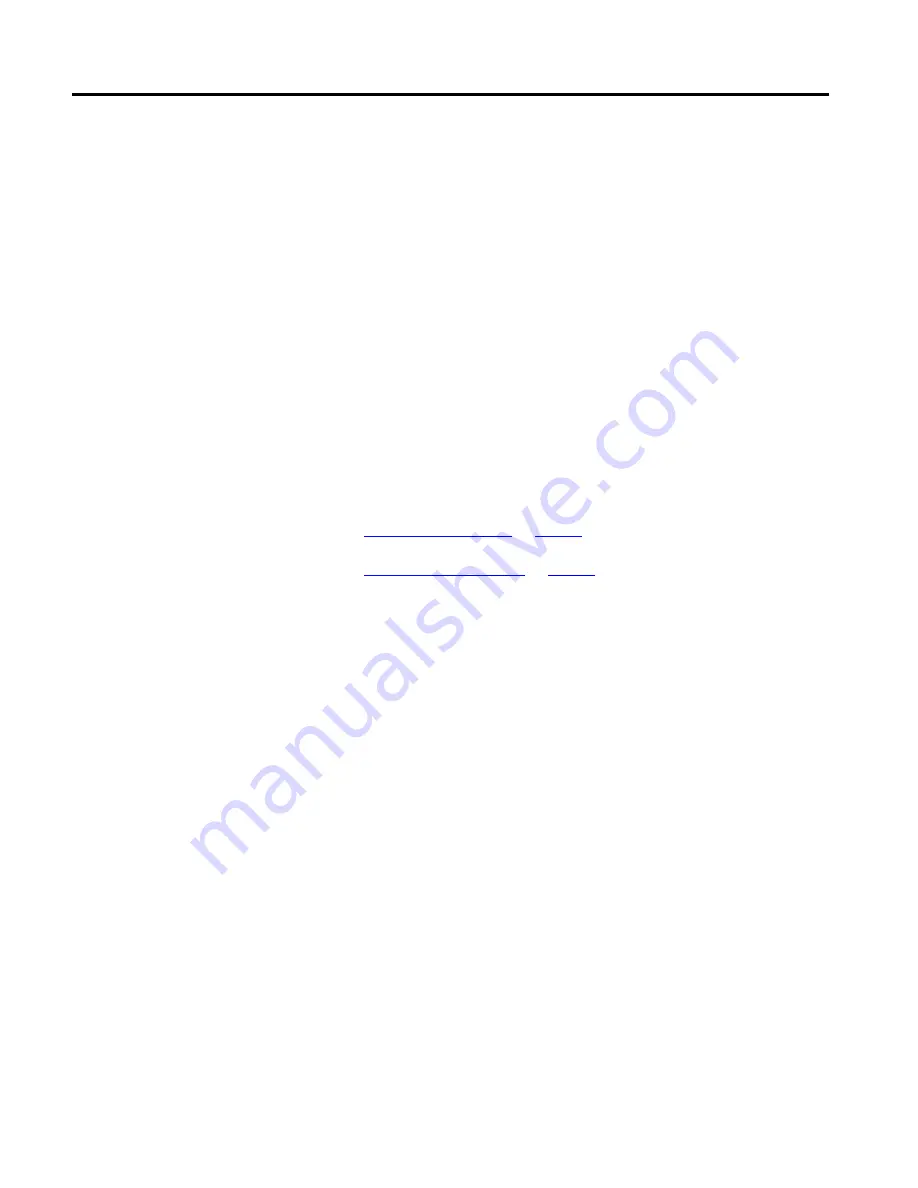
Behavior models used in CIP Motion
Chapter 2
Rockwell Automation Publication MOTION-RM003I-EN-P - February 2018
75
Inertia Observer
The Inertia Observer, when enabled, monitors the acceleration of the axis in
relationship to the torque producing current command, Iq Current Reference,
and estimates the total motor inertia.
The Total Inertia Estimate for the Inertia Observer is fed back to the Kj gain to
provide automatic gain control (AGC) with respect to load inertia. This feature
can be used to compensate for inertia variation without compromising system
performance. The Inertia Observer works on the premise that the motor and load
are not subject to externally applied torques or forces that could impact the
acceleration of the load. By contrast, the Load Observer in the Acceleration
Control behavior model works on the premise that changes in acceleration are due
to externally applied torques/forces on the motor and load. Thus, the operation of
these two observers are mutually exclusive; they should not be enabled at the same
time.
See also
Friction Compensation applies a compensating directional torque or force to the
motor to overcome the effects of friction in the mechanical system, thus
minimizing the amount of control effort required. Individual attributes have been
defined to support compensation for static friction, sliding (Coulomb) friction,
and viscous friction. A compensation window attribute is also provided to
mitigate motor dithering associated with conventional friction compensation
methods
Static Friction Compensation
It is not unusual for an axis to have enough static friction, commonly called
'sticktion', in Position Control applications that even with a significant position
error, the mechanical system refuses to budge. Of course, position integral gain can
be used to generate enough output to the drive to correct the error, but this
approach may not be responsive enough for the application. An alternative is to
use Static Friction Compensation to break the sticktion in the presence of a
non-zero position error. This is done by adding, or subtracting, a fixed torque
level, as determined by the Static Friction Compensation attribute, to the Torque
Reference signal value based on its current sign. This form of friction
compensation is applied only when the axis is static, for example, when there is no
change in the position command.
The Static Friction Compensation value must be just under the value that would
overcome the sticktion. A larger value results in axis 'dither', a phenomena
Friction Compensation