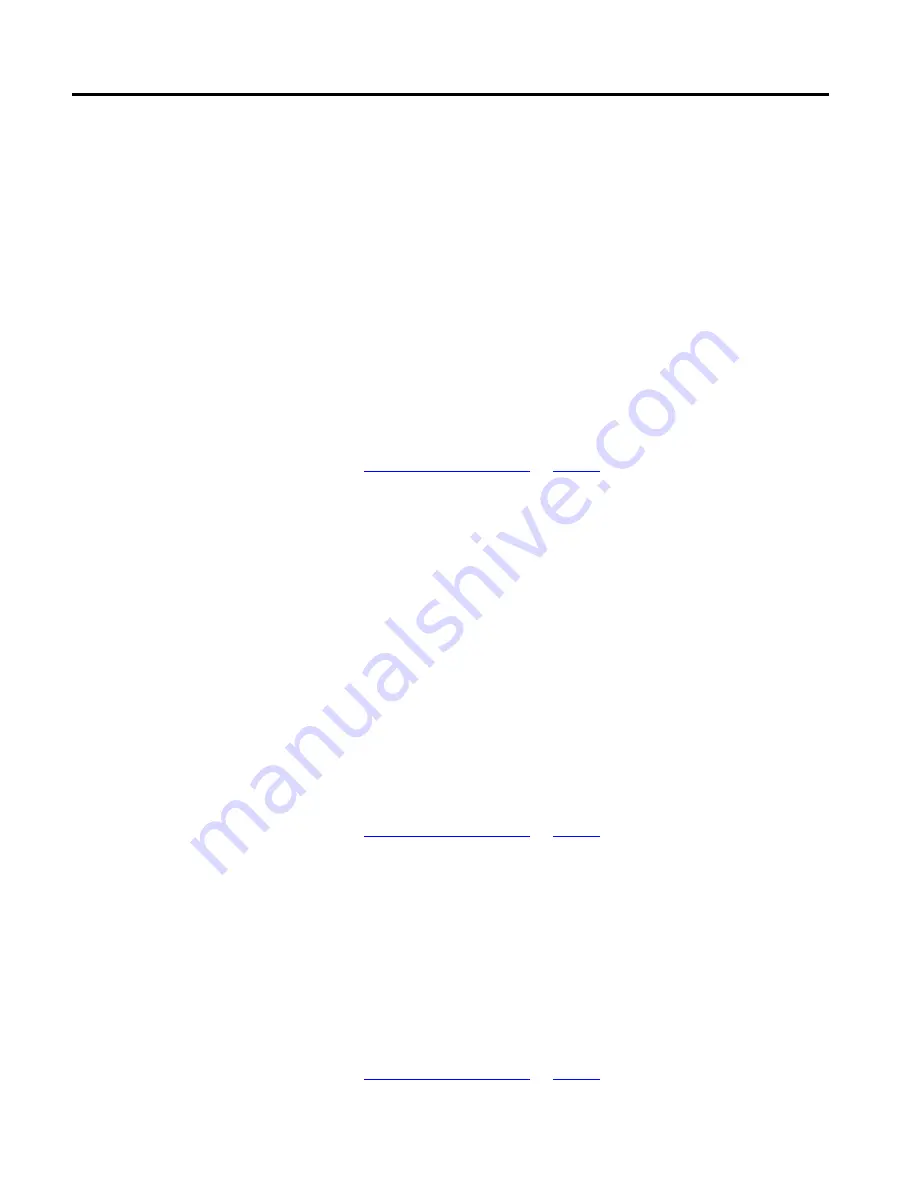
Behavior models used in CIP Motion
Chapter 2
Rockwell Automation Publication MOTION-RM003I-EN-P - February 2018
37
Thermal Limits for the Motor and Drive Inverter. Another possible limit source is
the user-configurable Current Vector Limit attribute.
Some of these limits are conditional and dynamic, such as the Motor and Inverter
Thermal Current Limits derived from the thermal models for these devices. These
limits are active only when the corresponding Motor and Inverter Overload
Action attributes are set to provide current fold-back. The thermal current limits
in this case would decrease as the simulated temperature of the modeled devices
increases. The Bus Regulator Limit is applied only when the motor is regenerating
power onto the DC Bus and is based on the Regenerative Power Limit.
With all these potential current limit sources that could be operative, a Current
Limit Source attribute identifies the source of the active current limit.
See also
The output of each current loop is scaled by the motor inductance to generate a
voltage command to the vector transformation block. It is the job of the vector
transformation block to transform the torque producing, Vq, and flux producing,
Vd, command signals from the rotating synchronous reference frame to the
stationary stator reference frame. The resultant U, V, and W Output Voltage
values are then applied to the motor by Pulse Width Modulation (PWM). The
PWM Frequency is also a configurable attribute.
The magnitude of the Vq, Vd vector is calculated in real time as the total Output
Voltage signal. The maximum Output Voltage signal that can be applied to the
motor is ultimately limited by the DC Bus Voltage and enforced by the Voltage
Vector Limiter. Any attempt to exceed this value results in an Inverter Voltage
Limit condition.
See also
Current feedback signals to the current loop are provided by two or three current
sensors. The signals from these sensors are conditioned and corrected for device
specific offsets to become the U, V, and W Current Feedback signals associated
with the stationary motor stator frame. These three signals are transformed back
to the synchronous reference frame to generate the Iq and Id Current Feedback
signals. The magnitude of the Iq, Id current vector is calculated in real-time and
used as an input to the thermal models for the inverter and motor.
See also
Voltage Output
Current Feedback