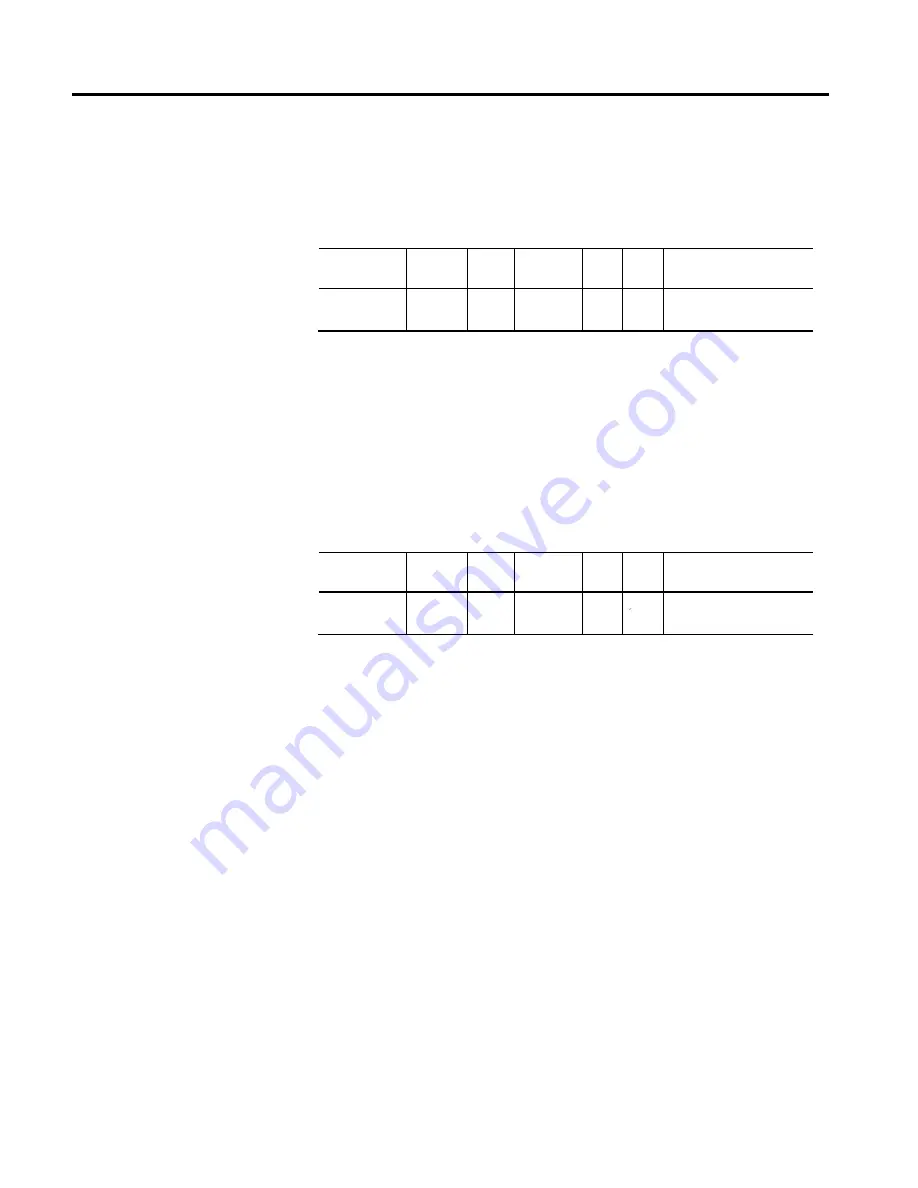
Chapter 4
CIP Axis Attributes
438
Rockwell Automation Publication MOTION-RM003I-EN-P - February 2018
7.
Wait for "Mechanical Brake Release Delay" while brake releases.
8.
Transition to Running (or Testing) state.
Mechanical Brake Engage Delay
Usage
Access
Data
Type
Default
Min
Max
Semantics of Values
Optional - D
Set/SSV
REAL
0
FD
0
10
3
Seconds
When disabling the motion axis using a Category 1 Stopping Action, the
Mechanical Brake Engage Delay value determines the amount of time the device
power structure will remain enabled after the axis has decelerated to standstill.
This attribute allows time for an external mechanical brake to engage. The
configured Stopping Action determines the type of stopping sequence applied. If
supported, a Brake Proving operation is included in the Category 1 stopping
sequence prior to disabling the power structure.
Zero Speed
Usage
Access
Data
Type
Default
Min
Max
Semantics of Values
Optional - D
Set/SSV
REAL
1
FD
0
% Motor Rated
This attribute sets the speed threshold associated with the zero speed criteria of
the stop sequence. Zero Speed is specified as a percent of motor rated speed. When
Zero Speed Time attribute is supported, this attribute sets the speed threshold
where the zero speed timer starts. When the axis speed has been below the Zero
Speed threshold for Zero Speed Time the axis has satisfied the zero speed criteria.
In all but Category 2 stops, this results in action to engage the mechanical brake. If
this attribute is not supported, the zero speed threshold is left to the vendor’s
discretion and typically set to 1% of motor rated speed. Axis speed in the above
description is based on the Velocity Feedback signal, or in the case of a Frequency
Control drive, axis speed is based on Velocity Reference signal.
When supporting a Load Observer, the zero speed criteria is not based on the
Velocity Estimate since that signal can differ considerably from the actual speed of
the motor. When the Load Observer is configured to apply the Velocity Estimate
to the velocity loop summing junction as Velocity Feedback, the zero speed criteria
must be based on the velocity feedback signal input to the Load Observer.