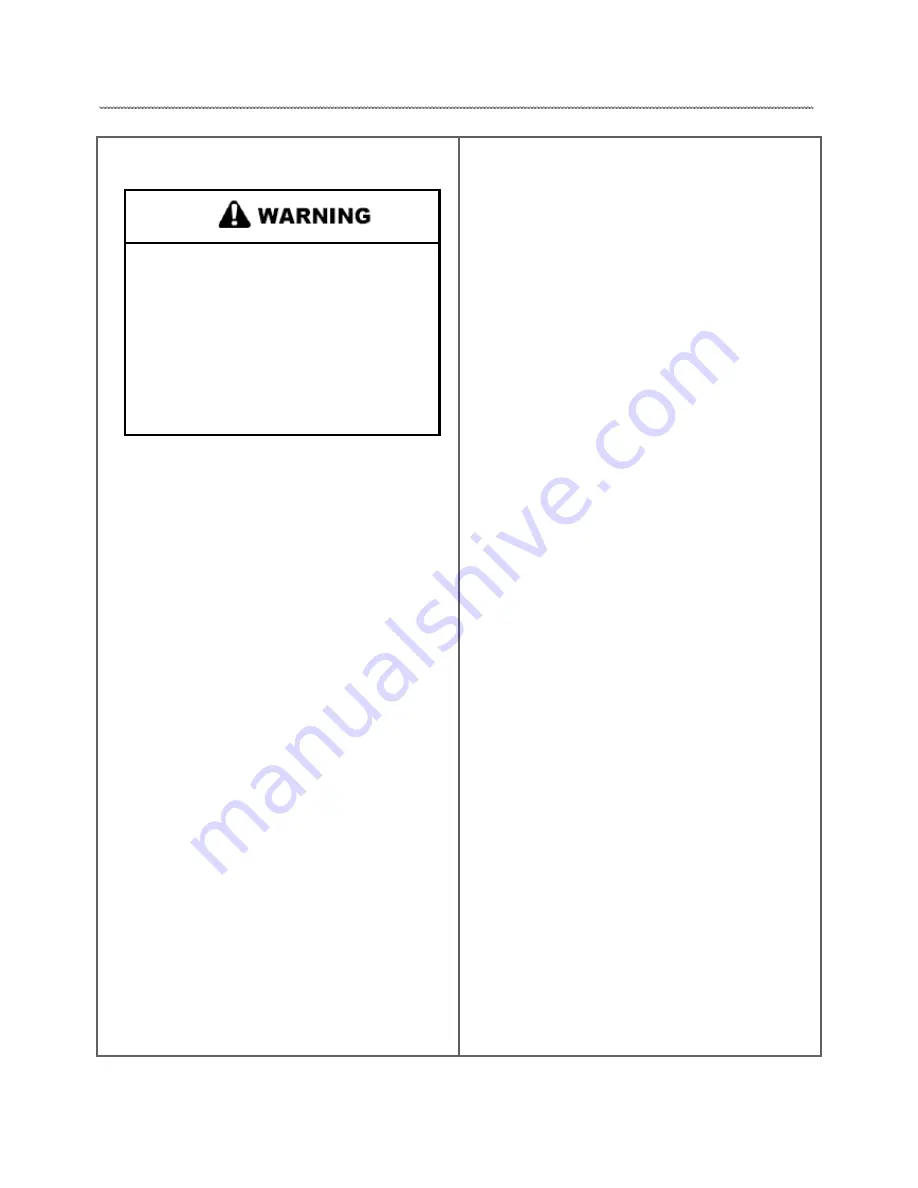
CVT SYSTEM
3-2
CVT SYSTEM
CVT SYSTEM OVERVIEW
Only a certified Aeon Service Dealer technician
who has received the proper training and
understands the procedures outlined in this
manual should perform all CVT maintenance or
repairs. Because of the critical nature and
precision balance incorporated into the CVT
components, it is absolutely essential that no
disassembly or repair be made without factory
authorized special tools and service procedures.
The Continuously Variable Transmission (CVT) consists of
three major assemblies: 1) The Drive Clutch. 2) The Driven
Clutch. 3) The Drive Belt.
The internal components of the drive clutch and driven clutch
control engagement (initial vehicle movement), clutch up shift
and backshift. During the development of an Aeon ATV, the
CVT system is matched first to the engine power curve; then to
average riding conditions and the vehicle’s intended usage.
Therefore, modifications or variations of components at
random are never recommended. Proper clutch setup and
careful inspection of existing components must be the primary
objective when troubleshooting and tuning.
CVT MAINTENANCE / INSPECTION
Under normal operation the CVT system will provide years of
trouble free operation. Periodic inspection and maintenance is
required to keep the system operating at peak performance.
The following list of items should be inspected and maintained
to ensure maximum performance and service life of CVT
components. See “CVT Overheating / Diagnosis” on page 3.4
for more information.
1. Drive clutch rollers and bushings. Driven clutch rollers,
pins, and spring.
2. Clutch sheave faces. Clean and inspect for wear.
3. CVT system sealing. The CVT system is air cooled by fins
on the drive clutch. The fins create a low-pressure area around
the drive clutch. The clutch cover must be sealed to ensure
water and other contaminants entering the CVT area.
DRIVE CLUTCH OPERATION
CVT drive clutch primarily sense engine RPM. The major
components, which controls shifting function, are the shift
centrifugal weights (rollers) inside the moveable sheave.
Whenever engine RPM is increased, centrifugal force is
created, causing the rollers to push against the cam plate and
force the moveable sheave toward the drive belt. This motion
pinches the drive belt between the spinning sheaves and causes
it to rotate, which in turn rotates the driven clutch. If belt speed
is sufficient, centrifugal friction shoes on the driven clutch
overcome their return spring pressure and swing outward
against the transmission drive hub, and the vehicle (if in gear)
begins to move. At lower RPM, the drive belt rotates low in
the drive clutch sheaves. As engine RPM increases, centrifugal
force causes the drive belt to be forced upward on drive clutch
sheaves, changing the ratio of the drive to driven clutch from
low to high.
DRIVEN CLUTCH OPERATION
Driven clutches primarily sense torque, but also react to RPM,
applying and retracting the friction shoes according to the
forces applied to it from the drive belt, while at the same time
reacting to the torque at the transmission input shaft. If the
torque resistance at the transmission input shaft is greater than
the load from the drive belt, the drive belt is kept at the outer
diameter of the driven clutch sheaves (low ratio). As engine
RPM and horsepower increase, the load from the drive belt
increases, resulting in the belt rotating up toward the outer
diameter of the drive clutch sheaves and downward into the
sheaves of the driven clutch. This action, which increases the
driven clutch speed, is called up shifting. Should the throttle
setting remain the same and the vehicle is subjected to a
heavier load, the torque sensing driven clutch will close,
forcing the drive belt back up toward the outer diameter of the
driven clutch. This also forces the belt downward into the
sheaves of the drive clutch. This action, which decreases the
driven clutch speed, called back shifting. In situations where
loads vary and throttle settings are constant, the drive and
driven clutches are continually shifting to maintain optimum
engine RPM. At full throttle a perfectly matched CVT system
should hold engine RPM at the peak of the power curve. This
RPM should be maintained during clutch up shift and
backshift. In this respect, the CVT system is similar to a power
governor. Rather than vary throttle position, as a conventional
governor does, the CVT system changes engine load
requirements by either up shifting or back shifting.
Summary of Contents for AT56-69E
Page 35: ...MAINTENANCE 2 25 ...
Page 45: ...CVT SYSTEM 3 4 CVT EXPLODED VIEW ...
Page 56: ...ENGINE 4 3 ENGINE ILLUSTRATION ENGINE EXPLODED VIEW ...
Page 57: ...ENGINE 4 4 ...
Page 58: ...ENGINE 4 5 COOLING SYSTEM EXPLODED VIEW ...
Page 59: ...ENGINE 4 6 OIL FLOW DIAGRAM ...
Page 125: ...FUEL AND CARBURETOR 6 15 FUEL TANK SYSTEM ...
Page 135: ...BODY SUSPENSION STEERING 7 6 SUSPENSION ...
Page 142: ...BODY SUSPENSION STEERING 7 13 STEERING ...
Page 151: ...BRAKES 8 6 FRONT BRAKE EXPLODED VIEW MASTER CYLINDER ...
Page 196: ...ELECTRICAL 9 31 WIRE DIAGRAM ...