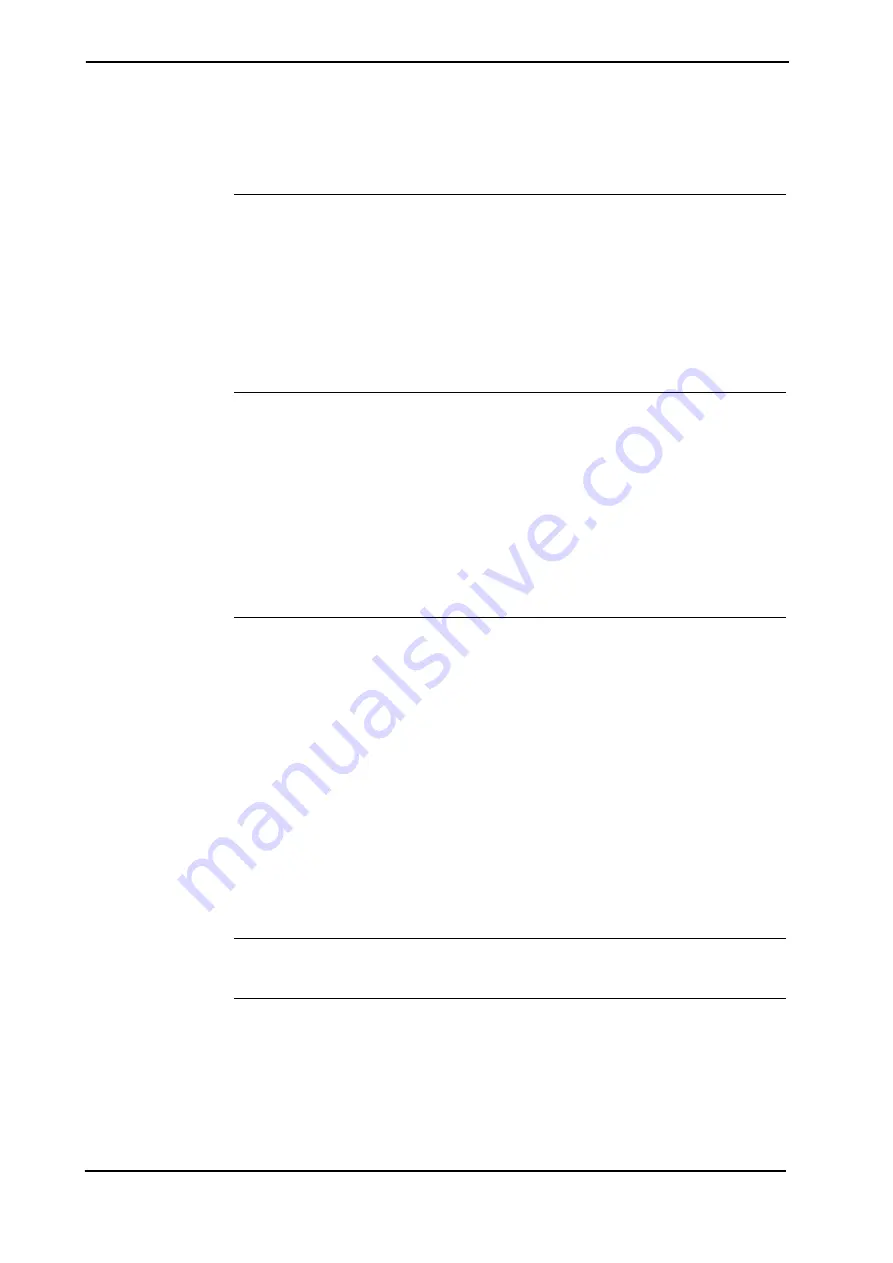
4 Repair
4.1.4 Fitting new Bearings and Seals
62
3HAC021111-001 Revision: B
4.1.4 Fitting new Bearings and Seals
Bearings
1. Do not unwrap new bearings until just before assembly, in order to prevent dust
and grit getting into the bearing.
2. Make sure that all parts of the bearing are free from burr dust, grinding dust and
any other contamination. Cast parts must be free from foundry sand.
3. Bearing rings, races and roller parts must not under any circumstances be sub-
jected to direct impact. The roller parts must not be subjected to any pressure that
is created during the assembly.
Tapered Bearings
1. The bearing should be tightened gradually until the recommended pre-tensioning
is attained.
2. The roller parts must be rotated a specified number of turns both before
pre-tensioning and during pre-tensioning.
3. The above procedure must be carried out to enable the roller parts to slot into the
correct position with respect to the racer flange.
4. It is important to position the bearings correctly, because this directly affects the
service life of the bearing.
Greasing
Bearings
1. Bearings must be greased after they are fitted. Extreme cleanliness is necessary
throughout. High quality lubricating grease, such as Shell Alvania WR2
(ABB’s art. No. 3537-1), should be used.
2. Grooved ball bearings should be greased on both sides.
3. Tapered roller bearings and axial needle bearings should be greased when they
are split.
4. Normally the bearings should not be completely filled with grease. However, if
there is space on both sides of the bearing, it can be filled completely with grease
when it is fitted, as surplus grease will be released from the bearing on start up.
5. 70-80% of the available volume of the bearing must be filled with grease during
operation.
6. Make sure that the grease is handled and stored correctly, to avoid contamination.
Seals
The most common cause of leakage is incorrect mounting.
Rotating Seals
1. The seal surfaces must be protected during transportation and assembly.
2. The seals must either be kept in their original packages or be protected well.
3. The seal surfaces must be inspected before mounting. If the seal is scratched or
damaged in such a way that it may cause leakage in the future, it must be
replaced.
Summary of Contents for IRB 1400
Page 1: ...Product manual Articulated robot IRB 1400 M2004 ...
Page 2: ......
Page 3: ...Product manual 3HAC021111 001 Revision B Articulated robot IRB 1400 M2000 M2004 ...
Page 12: ...0 0 2 Product documentation M2000 10 3HAC021111 001 Revision B ...
Page 132: ...5 Calibration M2000 5 4 1 Post calibration procedure 130 3HAC021111 001 Revision B ...
Page 142: ......
Page 148: ...7 Alternative calibration 7 0 5 Retrieving offset values 146 3HAC021111 001 Revision B ...
Page 170: ...10 Foldouts 10 0 1 Introduction 168 3HAC021111 001 Revision B ...
Page 171: ......
Page 172: ......
Page 173: ......
Page 174: ......
Page 175: ......
Page 176: ......
Page 177: ......
Page 178: ......
Page 179: ......
Page 180: ......
Page 182: ...11 Circuit diagram 11 0 1 Introduction 170 3HAC021111 001 Revision B ...
Page 196: ...Index 184 ...
Page 197: ......