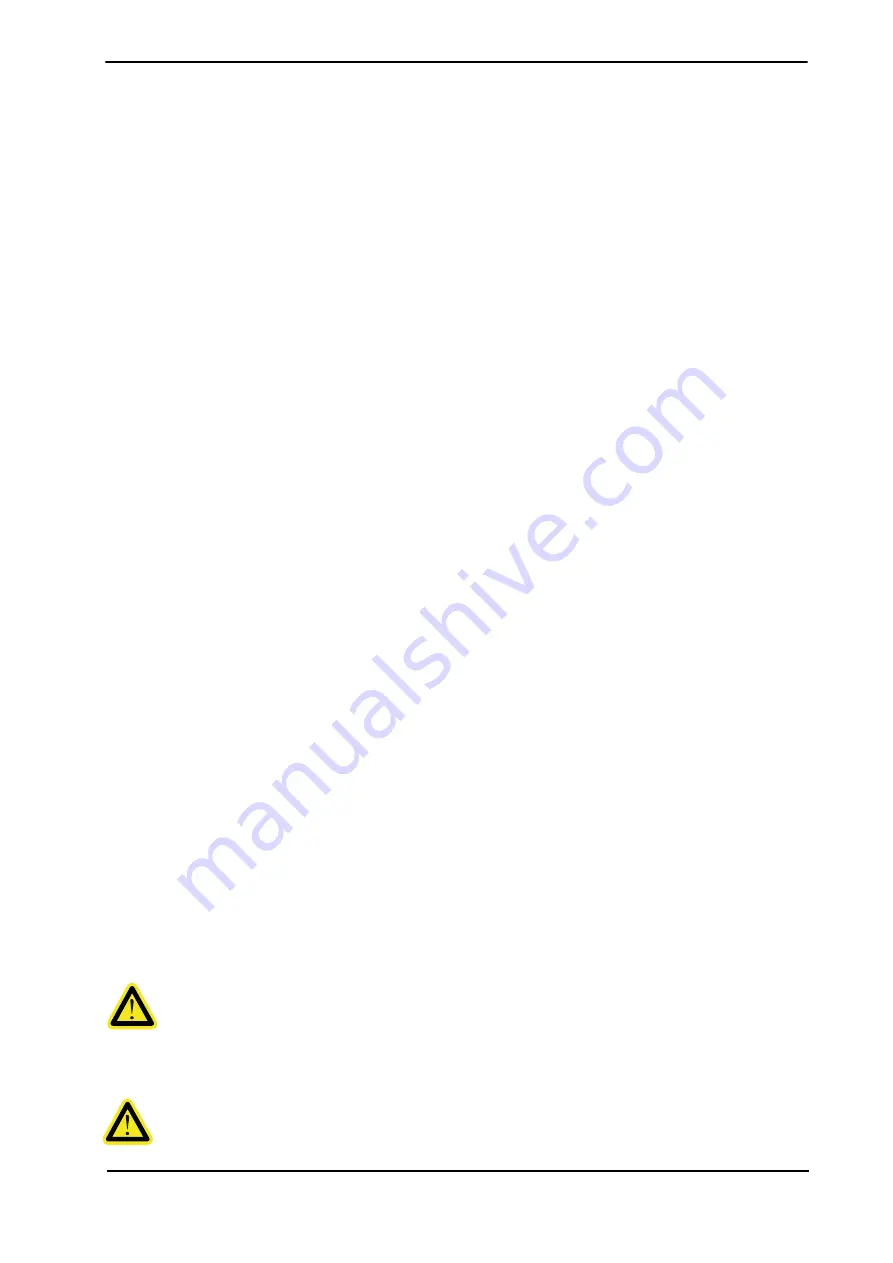
4 Repair
4.1.1 General description
3HAC021111-001 Revision: B
59
4: Repair
4.1: General information
4.1.1 General description
The industrial robot system comprises two separate units: the control cabinet and the manip-
ulator. The IRB 1400 is also available in a suspended version, IRB 1400H. Servicing the
mechanical unit is described in the following sections. Servicing the manipulator is described
in this manual.
When service on the IRB1400H is contemplated, a decision must be made in each particular
case whether the work can be carried out with the manipulator suspended or whether it must
be removed and the work done on the floor.
Lifting and turning the manipulator is described in section Lifting the Manipulator on page
When servicing the manipulator, it is helpful to service the following parts separately:
•
The Electrical System
•
The Motor Units
•
The Mechanical System
The Electrical System is routed through the entire manipulator and is made up of two main
cabling systems; the power cabling and signal cabling. The power cabling feeds the motor
units of the manipulator axes. The signal cabling feeds the various control parameters, such
as axis positions, motor revs, etc.
The AC Motor Units provide the motive power for the various manipulator axes by means of
gears. Mechanical brakes, electrically released, lock the motor units when the robot is inop-
erative for more than 3 minutes during both automatic and manual operation.
The manipulator has 6 axes which makes its movements very flexible.
Axis 1 rotates the manipulator. Axis 2 provides the lower arm’s reciprocating motion. The
lower arm, together with the parallel arm and the parallel bracket, forms a parallelogram
relative to the upper arm. The parallel bracket is mounted on bearings in the parallel arm and
in the upper arm.
Axis 3 raises the upper arm of the manipulator. Axis 4, located on the side of the upper arm,
rotates the upper arm. The wrist is bolted to the tip of the upper arm and includes axes 5 and
6. These axes form a cross and their motors are located at the rear of the upper arm.
Axis 5 is used to tilt and axis 6 to turn. A connection is supplied for various customer tools
on the tip of the wrist in the turn disc. The tool (or manipulator) can be pneumatically con-
trolled by means of an external air supply (optional extra). The signals to/from the tool can
be supplied via internal customer connections (optional extras).
Note that the control cabinet must be switched off during all maintenance work on the manip-
ulator. The accumulator power supply must always be disconnected before performing any
work on the manipulator measurement system (measurement boards, cabling, resolver unit).
When any type of maintenance work is carried out, the calibration position of the manipulator
must be checked before the robot is returned to the operational mode.
Take special care when manually operating the brakes. Make sure also that the safety instruc-
tions described in this manual are followed when starting to operate the robot.
Summary of Contents for IRB 1400
Page 1: ...Product manual Articulated robot IRB 1400 M2004 ...
Page 2: ......
Page 3: ...Product manual 3HAC021111 001 Revision B Articulated robot IRB 1400 M2000 M2004 ...
Page 12: ...0 0 2 Product documentation M2000 10 3HAC021111 001 Revision B ...
Page 132: ...5 Calibration M2000 5 4 1 Post calibration procedure 130 3HAC021111 001 Revision B ...
Page 142: ......
Page 148: ...7 Alternative calibration 7 0 5 Retrieving offset values 146 3HAC021111 001 Revision B ...
Page 170: ...10 Foldouts 10 0 1 Introduction 168 3HAC021111 001 Revision B ...
Page 171: ......
Page 172: ......
Page 173: ......
Page 174: ......
Page 175: ......
Page 176: ......
Page 177: ......
Page 178: ......
Page 179: ......
Page 180: ......
Page 182: ...11 Circuit diagram 11 0 1 Introduction 170 3HAC021111 001 Revision B ...
Page 196: ...Index 184 ...
Page 197: ......