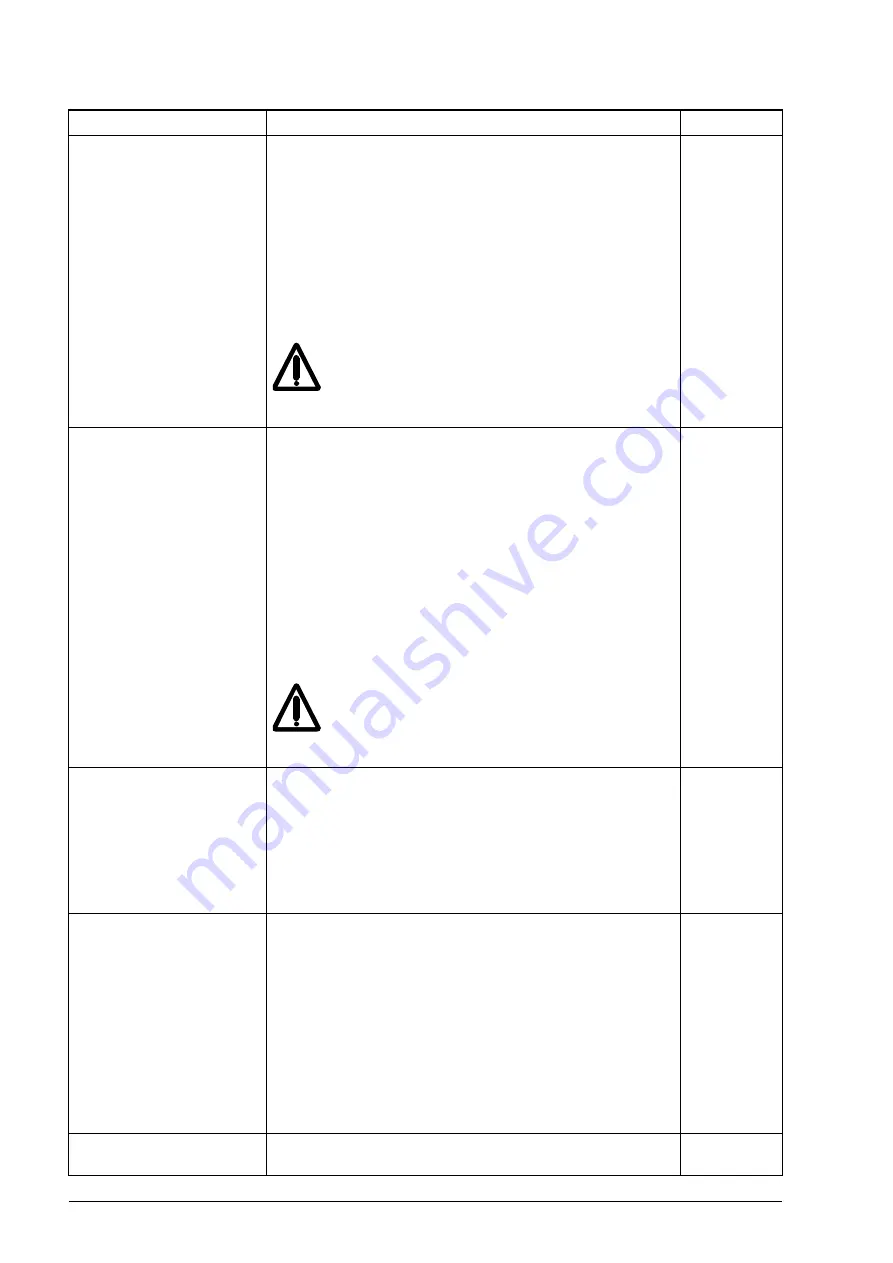
202 Parameters
Normal
Normal ID run. Guarantees the best possible control
accuracy. The ID run takes about 90 seconds. This mode
should be selected whenever it is possible.
Notes:
• The driven machinery must be de-coupled from the motor
with Normal ID run, if the load torque is higher than 20%,
or if the machinery is not able to withstand the nominal
torque transient during the ID run.
• Check the direction of rotation of the motor before starting
the ID run. During the run, the motor will rotate in the
forward direction.
WARNING!
The motor will run at up to
approximately 50…100% of the nominal speed
during the ID run. ENSURE THAT IT IS SAFE TO
RUN THE MOTOR BEFORE PERFORMING THE
ID RUN!
1
Reduced
Reduced ID Run. This mode should be selected instead of
the Normal ID Run if
• mechanical losses are higher than 20% (i.e. the motor
cannot be de-coupled from the driven equipment), or if
• flux reduction is not allowed while the motor is running (i.e.
in case of a motor with an integrated brake supplied from
the motor terminals).
With Reduced ID run, the control in the field weakening area
or at high torques is not necessarily as accurate as with the
Normal ID run. Reduced ID run is completed faster than the
Normal ID Run (< 90 seconds).
Note:
Check the direction of rotation of the motor before
starting the ID run. During the run, the motor will rotate in the
forward direction.
WARNING!
The motor will run at up to
approximately 50…100% of the nominal speed
during the ID run. ENSURE THAT IT IS SAFE TO
RUN THE MOTOR BEFORE PERFORMING THE
ID RUN!
2
Standstill
Standstill ID run. The motor is injected with DC current. With
an asynchronous motor, the motor shaft is not rotating (with
permanent magnet motor the shaft can rotate < 0.5
revolution).
Note:
This mode should be selected only if the
or
ID run is not possible due to the restrictions caused
by the connected mechanics (e.g. with lift or crane
applications).
3
Autophasing
During autophasing, the start angle of the motor is
determined. Note that other motor model values are not
updated. See also parameter
Notes:
• Autophasing can only be selected after the Normal/
Reduced/Standstill ID run has been performed once.
Autophasing is used when an absolute encoder has been
added/changed to a permanent magnet motor and there is
no need to perform the Normal/Reduced/Standstill ID run
again.
• During Autophasing, the motor shaft must NOT be locked
and the load torque must be < 5%.
4
Cur meas cal
Current offset and gain measurement calibration. The
calibration will be performed at next start.
5
No.
Name/Value
Description
FbEq
Summary of Contents for ACS850 series
Page 1: ...ACS850 Firmware Manual ACS850 Standard Control Program...
Page 2: ......
Page 4: ......
Page 24: ...24 Start up...
Page 28: ...28 Control locations and operating modes...
Page 252: ...252 Fieldbus control...