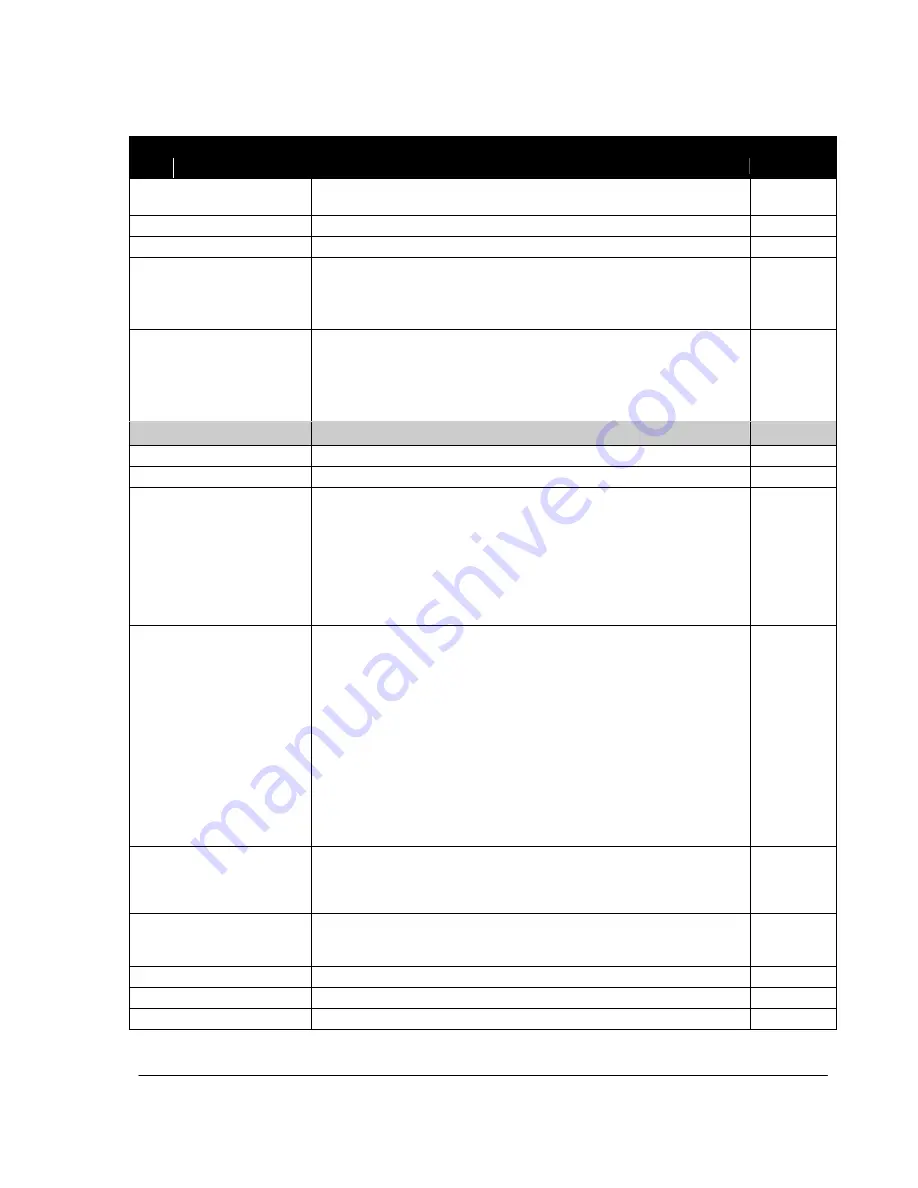
99
Actual signals and parameters
Parameters in the Long parameter mode
Index
Name/Selection
Description
Def
2008
MAXIMUM FREQ
Defines the maximum limit for the drive output frequency.
E: 50.0 Hz /
U: 60.0 Hz
0.0
…500.0 Hz
Maximum frequency. See parameter
2007
MINIMUM FREQ.
2020
BRAKE CHOPPER
Selects the brake chopper control.
0 = INBUILT
0 = INBUILT
Internal brake chopper control.
Note:
Ensure the brake resistor(s) is installed and the overvoltage control is
switched off by setting parameter
2005
OVERVOLT CTRL to selection 0
(DISABLE).
1 = EXTERNAL
External brake chopper control.
Note:
The drive is compatible only with ABB
ACS-BRK-X
brake units.
Note:
Ensure the brake unit is installed and the overvoltage control is
switched off by setting parameter
2005
OVERVOLT CTRL to selection 0
(DISABLE).
21 START/STOP
Start and stop modes of the motor
2101
START FUNCTION
Selects the motor starting method.
1 = AUTO
1 = AUTO
Frequency reference ramps immediately from 0 Hz.
2 = DC MAGN
The drive pre-magnetizes the motor with DC current before the start.
The pre-magnetizing time is defined by parameter
2103
DC MAGN TIME.
Note:
Starting the drive connected to a rotating motor is not possible when 2
(DC MAGN) is selected.
WARNING!
The drive starts after the set pre-magnetizing time has passed
even if the motor magnetization is not completed. In applications where a full
break-away torque is essential, always ensure that the constant magnetizing
time is long enough to allow generation of full magnetization and torque.
4 = TORQ BOOST
Torque boost should be selected if a high break-away torque is required.
The drive pre-magnetizes the motor with DC current before the start.
The pre-magnetizing time is defined by parameter
2103
DC MAGN TIME.
Torque boost is applied at start. Torque boost is stopped when output
frequency exceeds 20 Hz or when it is equal to the reference value. See
parameter
2110
TORQ BOOST CURR.
Note:
Starting the drive connected to a rotating motor is not possible when 4
(TORQ BOOST) is selected.
WARNING!
The drive starts after the set pre-magnetizing time has passed
although the motor magnetization is not completed. In applications where a
full break-away torque is essential, always ensure that the constant
magnetizing time is long enough to allow generation of full magnetization and
torque.
6 = SCAN START
Frequency scanning flying start (starting the drive connected to a rotating
motor). Based on frequency scanning (interval
2008
MAXIMUM
FREQ...
2007
MINIMUM FREQ) to identify the frequency. If frequency
identification fails, DC magnetization is used. See selection 2 (DC MAGN).
7 = SCAN+BOOST
Combines frequency scanning flying start (starting the drive connected to a
rotating motor) and torque boost. See selections 6 (SCAN START) and 4
(TORQ BOOST). If frequency identification fails, torque boost is used.
2102
STOP FUNCTION
Selects the motor stop function.
1 = COAST
1 = COAST
Stop by cutting off the motor power supply. The motor coasts to stop.
2 = RAMP
Stop along a ramp. See parameter group
22 ACCEL/DECEL
.
Summary of Contents for ACS150 series
Page 4: ......
Page 5: ......
Page 15: ...14 Safety ...
Page 19: ...18 Introduction to the manual ...
Page 39: ...38 Planning the electrical installation ...
Page 51: ...50 Installation checklist ...
Page 57: ...56 Start up and control with I O ...
Page 69: ...68 Control panel ...
Page 79: ...78 Application macros ...
Page 160: ...L Q M 0 I II D I II I I ro I m D en m D D Q Q f 3AFE68633931 A 0 Frame size R2 IP20 INEMA 1 ...
Page 161: ...ji 4 I 5 I 6 4 J ...
Page 162: ......
Page 163: ...160 Dimension drawings ...
Page 169: ...166 Appendix Process PID control ...
Page 171: ...168 ...