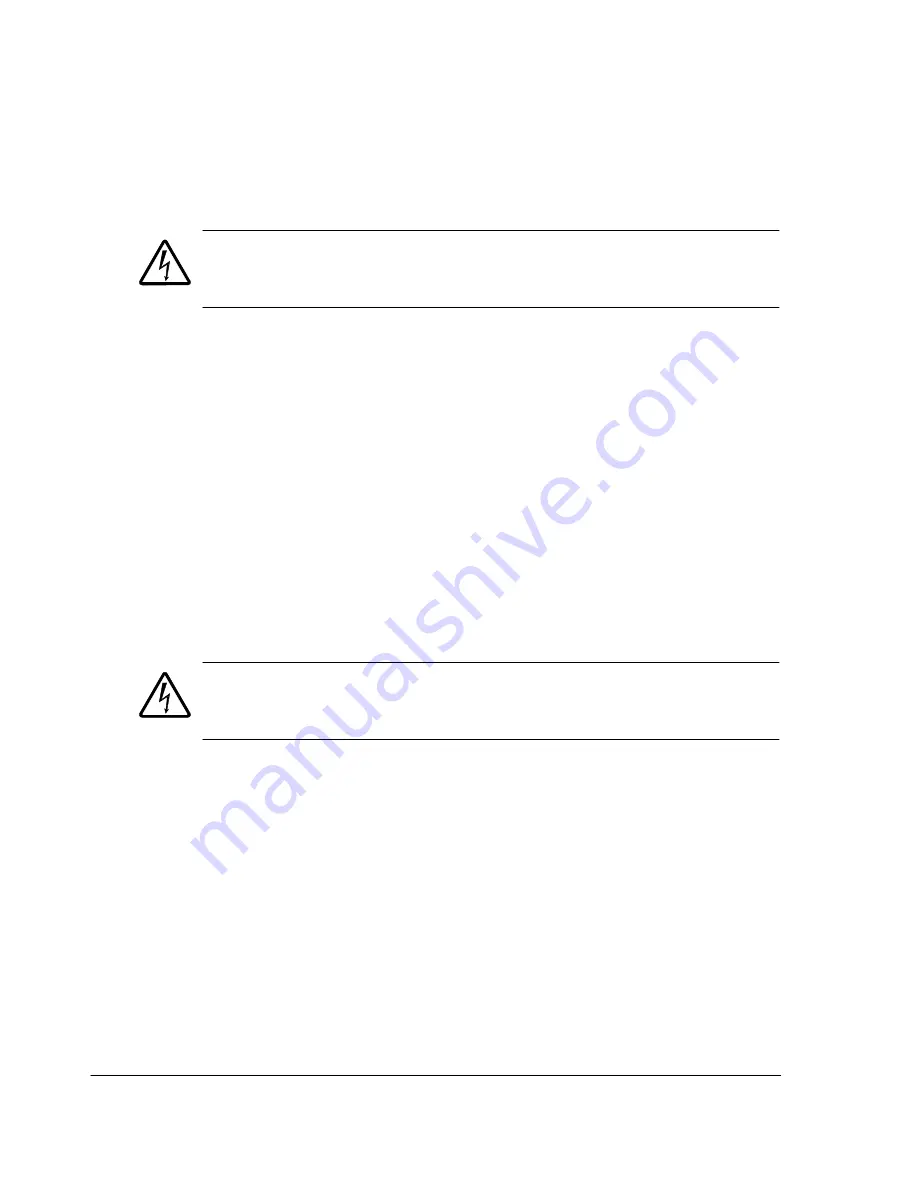
36
Planning the electrical installation
Protecting the drive, motor cable and input power cable against thermal overload
The drive protects itself and the input and motor cables against thermal overload
when the cables are dimensioned according to the nominal current of the drive. No
additional thermal protection devices are needed.
WARNING!
If the drive is connected to multiple motors, a separate thermal overload
switch or a circuit breaker must be used for protecting each cable and motor. These
devices may require a separate fuse to cut off the short-circuit current.
Protecting the motor against thermal overload
According to regulations, the motor must be protected against thermal overload and
the current must be switched off when overload is detected. The drive includes a
motor thermal protection function that protects the motor and switches off the current
when necessary. See parameter
3005
MOT THERM PROT for more information on
the motor thermal protection.
Residual current device (RCD) compatibility
ACS150-01x drives are suitable to be used with residual current devices of Type A,
ACS150-03x drives with residual current devices of Type B. For ACS150-03x drives,
other measures for protection in case of direct or indirect contact, such as separation
from the environment by double or reinforced insulation or isolation from the supply
system by a transformer, can also be applied.
Implementing a bypass connection
WARNING!
Never connect the supply power to the drive output terminals U2, V2
and W2. Power line voltage applied to the output can result in permanent damage to
the drive.
If frequent bypassing is required, employ mechanically connected switches or
contactors to ensure that the motor terminals are not connected to the AC power line
and drive output terminals simultaneously.
Summary of Contents for ACS150 series
Page 4: ......
Page 5: ......
Page 15: ...14 Safety ...
Page 19: ...18 Introduction to the manual ...
Page 39: ...38 Planning the electrical installation ...
Page 51: ...50 Installation checklist ...
Page 57: ...56 Start up and control with I O ...
Page 69: ...68 Control panel ...
Page 79: ...78 Application macros ...
Page 160: ...L Q M 0 I II D I II I I ro I m D en m D D Q Q f 3AFE68633931 A 0 Frame size R2 IP20 INEMA 1 ...
Page 161: ...ji 4 I 5 I 6 4 J ...
Page 162: ......
Page 163: ...160 Dimension drawings ...
Page 169: ...166 Appendix Process PID control ...
Page 171: ...168 ...