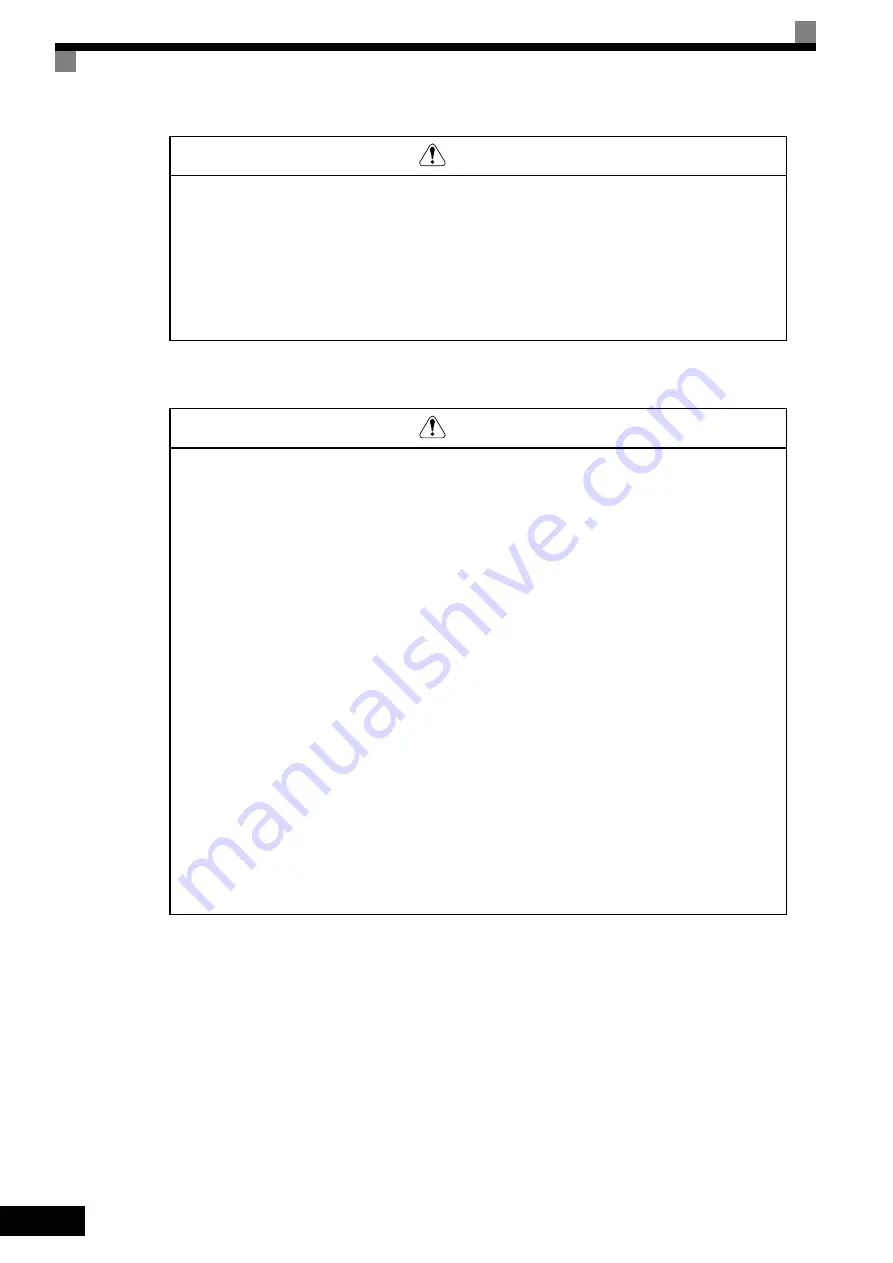
iv
Setting User Constants
• Tighten all terminal screws to the specified tightening torque.
Otherwise, a fire may occur.
• Do not connect AC power to output terminals U, V, and W.
The interior parts of the Inverter will be damaged if voltage is applied to the output terminals.
• Do not connect phase-advancing capacitors or LC/RC noise filters to the output circuits.
The Inverter can be damaged or interior parts burnt if these devices are connected.
• Do not connect electromagnetic switches or magnetic contactors to the output circuits.
If a load is connected while the Inverter is operating, surge current will cause the overcurrent protection circuit inside the
Inverter to operate.
CAUTION
• Disconnect the load (machine, device) from the motor before performing rotational autotuning.
The motor may turn, possibly resulting in injury or damage to equipment. Also, motor constants cannot be correctly set
with the motor attached to a load.
• Stay clear of the motor during rotational autotuning.
The motor repeats running and stopping until autotuning has been completed, possibly resulting in injury.
• In stationary autotuning 1, when the motor is first operated in the drive mode after tuning, the
remaining motor constants E2-02 (Motor rated slip) and E2-03 (Motor no-load current) are set auto-
matically. To perform an operation immediately after stationary autotuning 1, use the following pro-
cedure under the recommended conditions.
(1) Check the values of E2-02 and E2-03 in verify mode or advanced programming mode.
(2) Run the motor once in drive mode under the following conditions.
• The Inverter and the motor are connected.
• The motor shaft is not locked with a mechanical brake or other stopping mechanism (or function).
• A motor-load ratio of 30% or less is maintained.
• A speed of 30% or more of the base frequency set at E1-06 (default = highest frequency) is maintained at
a constant speed for one second or more.
(3) After stopping the motor, check the values of E2-02 and E2-03 again in verify mode or advanced program-
ming mode. If the values of E2-02 and E2-03 differ from the ones before the first operation was carried out,
the settings have been successfully completed. Next, check if the values are suitable or not.
If the values of E2-02 and E2-03 differed greatly from the reference data of the motor in the test report or the instruction
manual (TOE-S616-55.1), hunting, motor vibrations, insufficient motor torque, or an overcurrent may occur because the
motor is operated although the aforementioned conditions have not been fulfilled after stationary autotuning 1. For eleva-
tors, failure to observe this caution may result in the cage falling or injury. If so, perform stationary autotuning 1 again and
run the motor using the aforementioned procedure under the recommended conditions or perform stationary autotuning 2
or rotational autotuning.
Usually the standard setting for E2-02 is 1 Hz to 3 Hz, and that for E2-03 is 30
%
to 65
%
of the rated current for a general-
purpose motor. Generally, the larger the motor capacity is, the smaller the rated slip and the ratio of the no-load current to
the rated current become. Use the data given in
Factory Settings that Change with the Inverter Capacity (o2-04) of Chap-
ter 5 User Constants
as a reference.
CAUTION