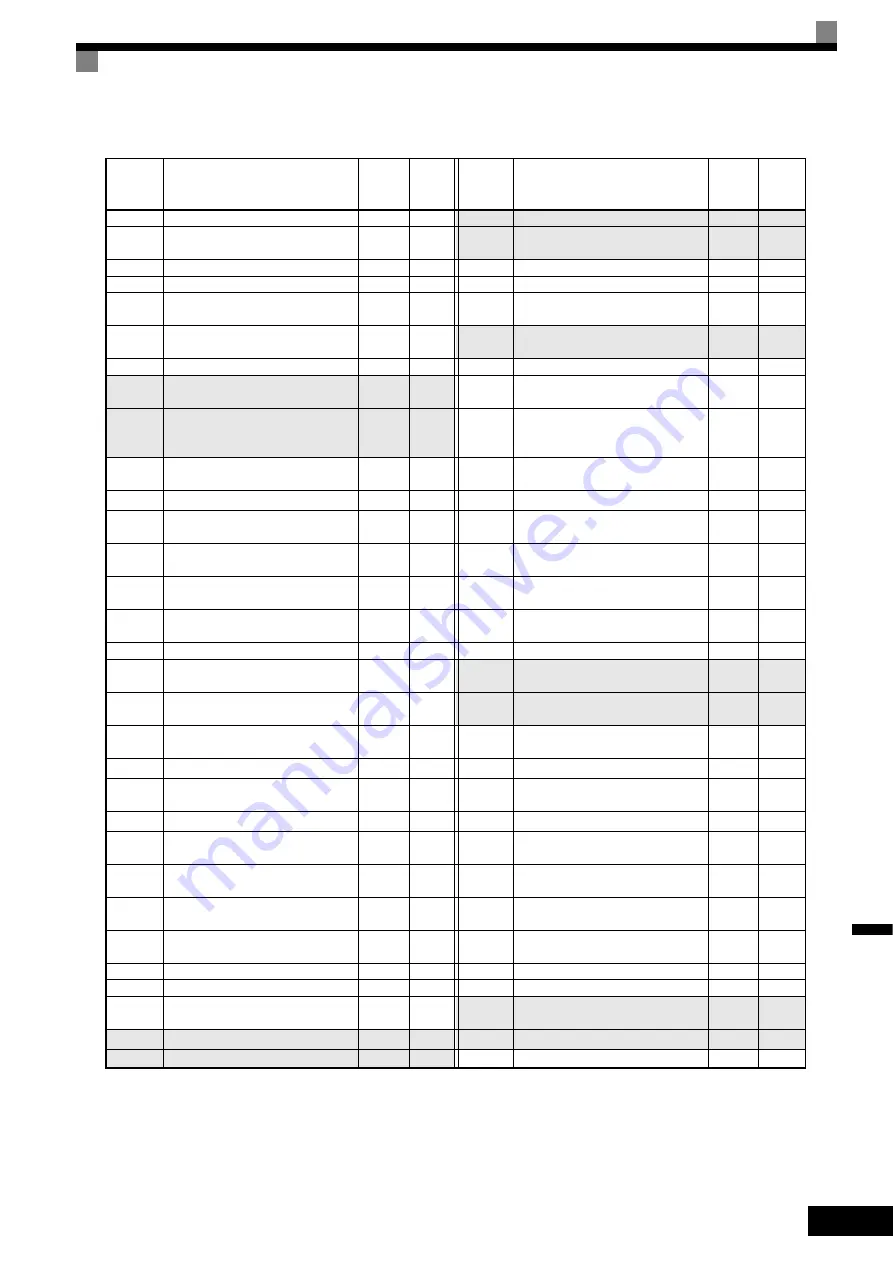
User Constants
10-
35
10
* 1. Not initialized. (Japanese standard specifications: A1-01 = 1, A1-02 = 2)
* 2. The factory setting will change when the control method is changed. The V/f control factory settings are given.
* 3. The factory setting is 1.0 when using flux vector control.
* 4. The factory setting is 2.00 s when Inverter capacity is 55 kW min.
The factory setting will change if the control method is changed. The open-loop vector factory setting is given.
* 5. By setting E2-11 (Motor rated output) the appropriate value will be set.
* 6. The factory setting depends on the Inverter capacity. The values for a 200 V Class Inverter for 0.4 kW are given.
L6-04 Torque detection selection 2
0
N5-03 Feed forward proportional gain
1.0
L6-05 Torque detection level 2
150
N5-04
Response frequency for speed
command
40.00
L6-06 Torque detection time 2
0.1
o1-01
Monitor selection
6
L7-01 Forward drive torque limit
200
o1-02
Monitor selection after power up
1
L7-02 Reverse drive torque limit
200
o1-03
Frequency units of reference set-
ting and monitor
0
L7-03 Forward regenerative torque limit
200
o1-04
Setting unit for frequency con-
stants related to V/f characteristics
0
L7-04 Reverse regenerative torque limit
200
o1-05
LCD brightness adjustment
3
L7-06
Integral time setting for torque
limit
200
o2-01
LOCAL/REMOTE key enable/dis-
able
1
L7-07
Control method selection for
torque limit during acceleration
and deceleration
0
o2-02
STOP key during control circuit
terminal operation
1
L8-01
Protect selection for internal DB
resistor (Type ERF)
0
o2-03
User constant initial value
0
L8-02 Overheat pre-alarm level
95
*6
o2-04
kVA selection
0
*6
L8-03
Operation selection after overheat
pre-alarm
3
o2-05
Frequency reference setting
method selection
0
L8-05
Input open-phase protection selec-
tion
0
o2-06
Operation selection when digital
operator is disconnected
0
L8-07
Output open-phase protection
selection
0
o2-07
Cumulative operation time setting
0
L8-09 Ground protection selection
1
o2-08
Cumulative operation time selec-
tion
0
L8-10 Cooling fan control selection
0
o2-10
Fan operation time setting
0
L8-11
Cooling fan control delay time
60
o2-12
Fault trace/fault history clear func-
tion
0
L8-12 Ambient temperature
45
o2-14
Output power monitor clear selec-
tion
0
L8-15
OL2 characteristics selection at
low speeds
1
o3-01
Copy function selection
0
L8-18 Soft CLA selection
1
*2
o3-02
Read permitted selection
0
N1-01
Hunting-prevention function selec-
tion
1
T1-00 Motor 1/2 selection
1
N1-02 Hunting-prevention gain
1.00
T1-01 Autotuning mode selection
2
*2
N2-01
Speed feedback detection control
(AFR) gain
1.00
T1-02 Motor output power
0.40
*6
N2-02
Speed feedback detection control
(AFR) time constant
50
T1-03 Motor rated voltage
200.0
*9
N2-03
Speed feedback detection control
(AFR) time constant 2
750
T1-04 Motor rated current
1.90
*6
N3-01
High-slip braking deceleration fre-
quency width
5
T1-05 Motor base frequency
60.0
N3-02 High-slip braking current limit
150
T1-06 Number of motor poles
4
N3-03 High-slip braking stop dwell time
1.0
T1-07 Motor base speed
1750
N3-04 High-slip braking OL time
40
T1-08
Number of PG pulses when turn-
ing
600
N5-01 Feed forward control selection
0
T1-09 Motor no-load current
1.20
*6
N5-02 Motor acceleration time
0.178
*6
Table 10.7 User Constants (Continued)
No.
Name
Fac-
tory
Setting
Set-
ting
No.
Name
Fac-
tory
Setting
Set-
ting