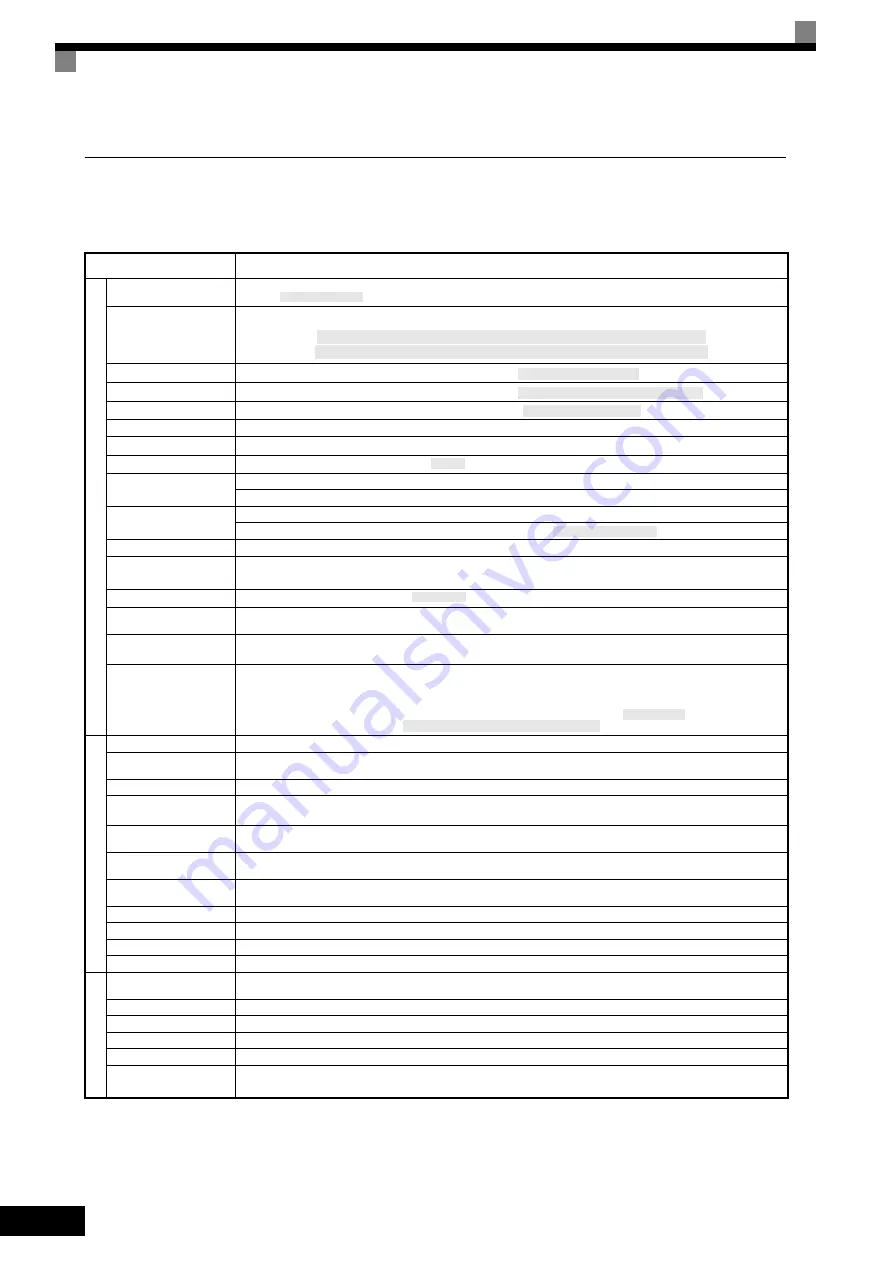
9
-4
Common Specifications
The following specifications apply to both 200 V and 400 V Class Inverters.
* 1. Rotational autotuning must be performed to ensure obtaining the specifications given for flux or open-loop vector control.
* 2. Increase the Inverter capacity if loads exceeding these current values are expected.
* 3. Only VT can be set for 200 V Class 110 kW as well as 400 V Class 220 kW and 300 kW Inverters.
* 4. The speed control accuracy depends on the installation condition and types of motor used. Contact your Yaskawa representative for details.
* 5. When connecting a Braking Resistor or Braking Resistor Unit, set L3-04 (Stall prevention selection during deceleration) to 0 (disabled). Stopping may not be
possible in the specified deceleration time if this function is not disabled.
* 6. Derating is required for applications that use repetitive loads. (Refer to page 10-6 for details.)
Table 9.3 Common Specifications
Model Number
CIMR-F7A
Specification
Control method
Sine wave PWM
, Open-loop vector control, V/f control, V/f with PG control (switched by constant setting)
Torque characteristics
CT selected (low carrier, constant torque applications): 150% /0.5 Hz (Open-loop vector control)
VT selected (high carrier, variable torque applications): 120%/0.5 Hz (Open-loop vector control)
Speed control range
1:100 (Open-loop vector control),
*1
Speed control accuracy
*4
±0.2% (25
°
C ± 10
°
C, Open-loop vector control),
*1
Speed control response
5 Hz (Open-loop vector control),
Torque limits
Provided for vector control only (4 quadrant steps can be changed by constant settings.)
Torque accuracy
*4
±5%
Frequency control range
0.01 to 150 Hz
(CT selected.), 0.01 to 400 Hz (VT selected.)
Frequency accuracy (tem-
perature characteristics)
Digital references: ± 0.01% (-10
°
C to +40
°
C)
Analog references: ±0.1% (25
°
C ±10
°
C)
Frequency setting resolution
Digital references: 0.01 Hz
Analog references: 0.06 Hz/60 Hz (+10 bit)
Output frequency resolution
0.001 Hz
Overload capacity and max-
imum current
*2
CT selected (low carrier, constant torque applications): 150% of rated output current per minute
*3, *6
VT selected (high carrier, variable torque applications): 120% of rated output current per minute
*6
Frequency setting signal
, 0 to 10 V, 4 to 20 mA, pulse train
Acceleration/Deceleration
time
0.01 to 6000.0 s (4 selectable combinations of independent acceleration and deceleration settings)
Braking torque
Approximately 20% (Approximately 125% with Braking Resistor option
*5
, braking transformer built into 200 V and 400 V Class
Inverters for 18.5 kW or less.)
Main control functions
Restarting for momentary power loss, speed searches, overtorque detection, torque limits, 17-speed control (maximum), accelera-
tion/deceleration time changes, S-curve acceleration/deceleration, 3-wire sequence, autotuning (rotational or stationary), dwell
functions, cooling fan ON/OFF control, slip compensation, torque compensation, jump frequencies, upper and lower limits for
frequency references, DC braking for starting and stopping, high-slip braking, PID control (with sleep function), energy-saving
control, MEMOBUS communications (RS-485/422, 19.2 kbps maximum), fault reset,
, function copying,
, etc.
Motor protection
Protection by electronic thermal overload relay.
Instantaneous overcurrent
protection
Stops at approx. 200% of rated output current.
Fuse blown protection
Stops for fuse blown.
Overload protection
CT selected (low carrier, constant torque applications): 150% of rated output current per minute
*3
VT selected (high carrier, variable torque applications): 120% of rated output current per minute
Overvoltage protection
200 Class Inverter: Stops when main-circuit DC voltage is above applox. 410 V.
400 Class Inverter: Stops when main-circuit DC voltage is above applox. 820 V.
Undervoltage protection
200 Class Inverter: Stops when main-circuit DC voltage is below applox. 190 V.
400 Class Inverter: Stops when main-circuit DC voltage is below applox. 380 V.
Momentary power loss
ridethru
Stops for 15 ms or more.
By selecting the momentary power loss method, operation can be continued if power is restored within 2 s.
Cooling fin overheating
Protection by thermistor.
Stall prevention
Stall prevention during acceleration, deceleration, or running.
Grounding protection
Protection by electronic circuits. (Overcurrent level)
Charge indicator
Lit when the main circuit DC voltage is approx. 50 V or more.
Ambient operating tempera-
ture
-10
°
C to 40
°
C (Enclosed wall-mounted type)
10
°
C to 45
°
C (Open chassis type)
Ambient operating humidity
95% max. (with no condensation)
Storage temperature
- 20
°
C to + 60
°
C (short-term temperature during transportation)
Application site
Indoor (no corrosive gas, dust, etc.)
Altitude
1000 m max.
Vibration
10 to 20 Hz: 9.8 m/s
2
20 to 50 Hz: 2.0 m/s
2
C
on
tr
ol
c
har
act
er
ist
ics
Flux vector control
CT selected (low carrier, constant torque applications): 150%/0 min
-1
(Flux vector control)
VT selected (high carrier, variable torque applications): 120%/0 min
-1
(Flux vector control)
1:1000 (Flux vector control)
±0.02% (25
°
C ± 10
°
C, Flux vector control)
40 Hz (Flux vector control)
300 Hz
0.03 Hz/60 Hz (±11 bit)
-10 to +10V
Droop control
torque control, speed/torque control switching
Prot
ect
ive
funct
ions
Env
ironm
ent