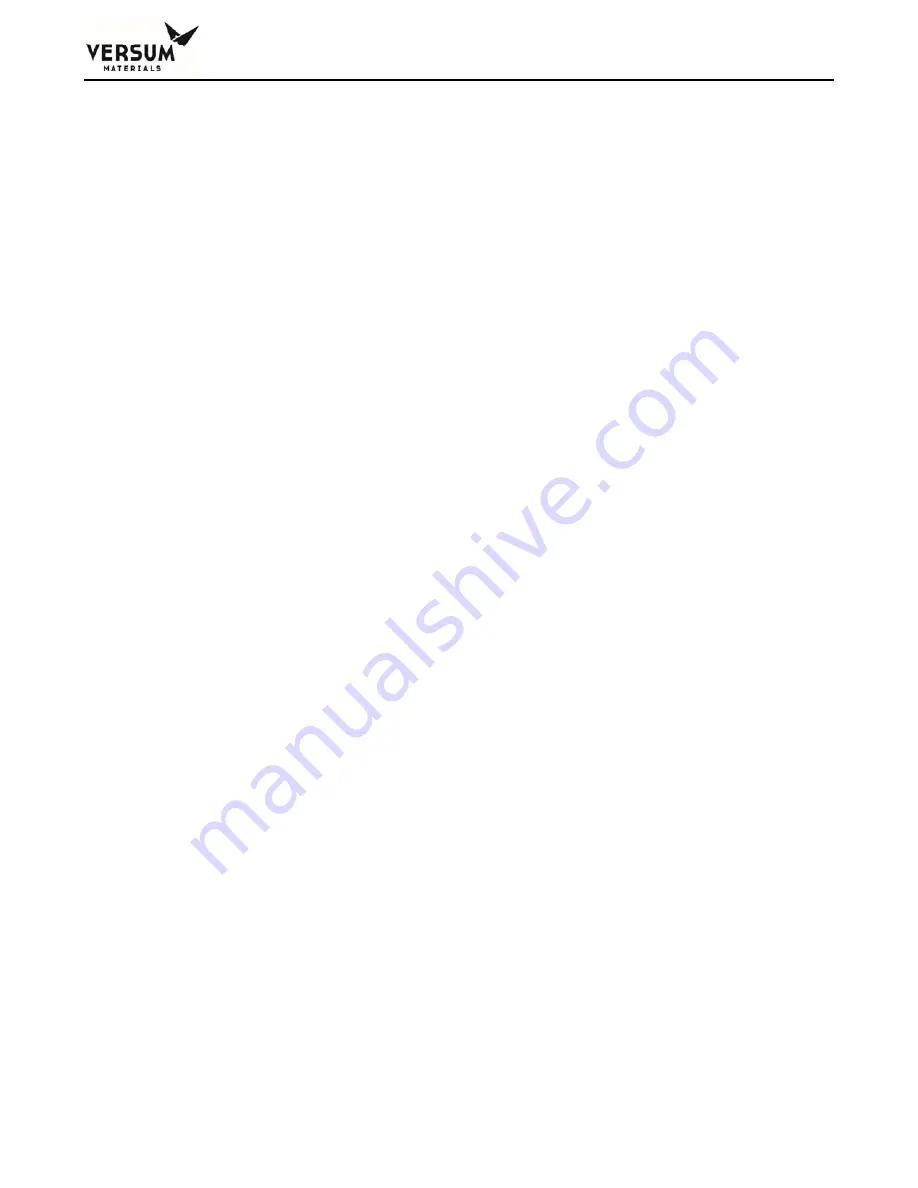
Appendix -
_______________________________________________________________________________________________________________
MNL000450.doc
Revision 0
09/19/2016
© Versum Materials, Inc. as of the revision and date shown. All rights reserved.
Confidential and Proprietary Data
Page APP
-
5
6.6.1
Final cleaning of fittings shall be performed under Class 100 environment.
6.6.2
Fittings shall be flushed with heated DI water ( 60oC) minimum.
6.6.3
Fittings shall be blown dry with heated nitrogen gas
6.7
Packaging
:
6.7.1
Tubing ends shall be sealed with polyethylene caps pressed over polyamide nylon squares
(1.75 mil) after being purged with nitrogen. Polyethylene bags (6 mil) shall then be placed
over each end and taped to the tube a minimum of 3" from the end of the tube, using clean
room tape. The entire tube shall then be closed in a 6 mil polyethylene bag and heat
sealed at both ends.
6.7.2
Fitting ends shall be packaged in a heat sealed nylon bag with a heat sealed polyethylene
bag over the nylon bag in a Class 100 environment.
6.7.3
Pack and ship to prevent damage to double bagging, tubing, and fittings.
6.7.4
Finished components shall be mill and heat traceable and permanently marked for
correspondence to the applicable mill test reports.
6.8
Inspection and Testing:
6.8.1
All tests and inspections required in this section shall be performed for each order unless
otherwise stated in the purchase order. The vendor shall provide a detailed procedure for
each test required in Sections 6.9.1.2 - 6.9.1.10 for VERSUM MATERIALS, INC. review
and acceptance.
6.8.2
One hundred percent (100%) of components shall be visually inspected to assure that
interior surfaces exhibit no macroscopic pitting, staining, or discoloration as can be
detected with the unaided eye.
6.8.3
A statistically valid sample of tubes and fittings shall be measured with calipers and/or
micrometers or by other repeatable methods to verify conformance to the critical
dimensional requirements and monitor process control. Critical dimensions will be
identified in the purchase order. Statistical procedures must be submitted to VERSUM
MATERIALS, INC. for review and approval prior to receipt of material.
6.8.4
All welded fittings shall be inboard helium leak tested to a 1 x 10-9 atm cc/sec gaseous
helium with a mass spectrometer leak detector.
6.8.5
Finished tube and fittings in each lot shall be measured for interior surface finish with a
stylus type measuring device in accordance with ASME B46.1 - 1985. Surface roughness
shall be measured at three locations for each piece tested. Sample quantity for tubing
shall be 10% of tube ends and 1% of middle sections. Sample quantity for fittings shall be
10% of fitting ends. The average of the readings shall not exceed 7 microinch Ra with no
single reading above 10 microinch Ra. Sampling length cutoff shall be 0.030" and traverse
length will be 0.150".