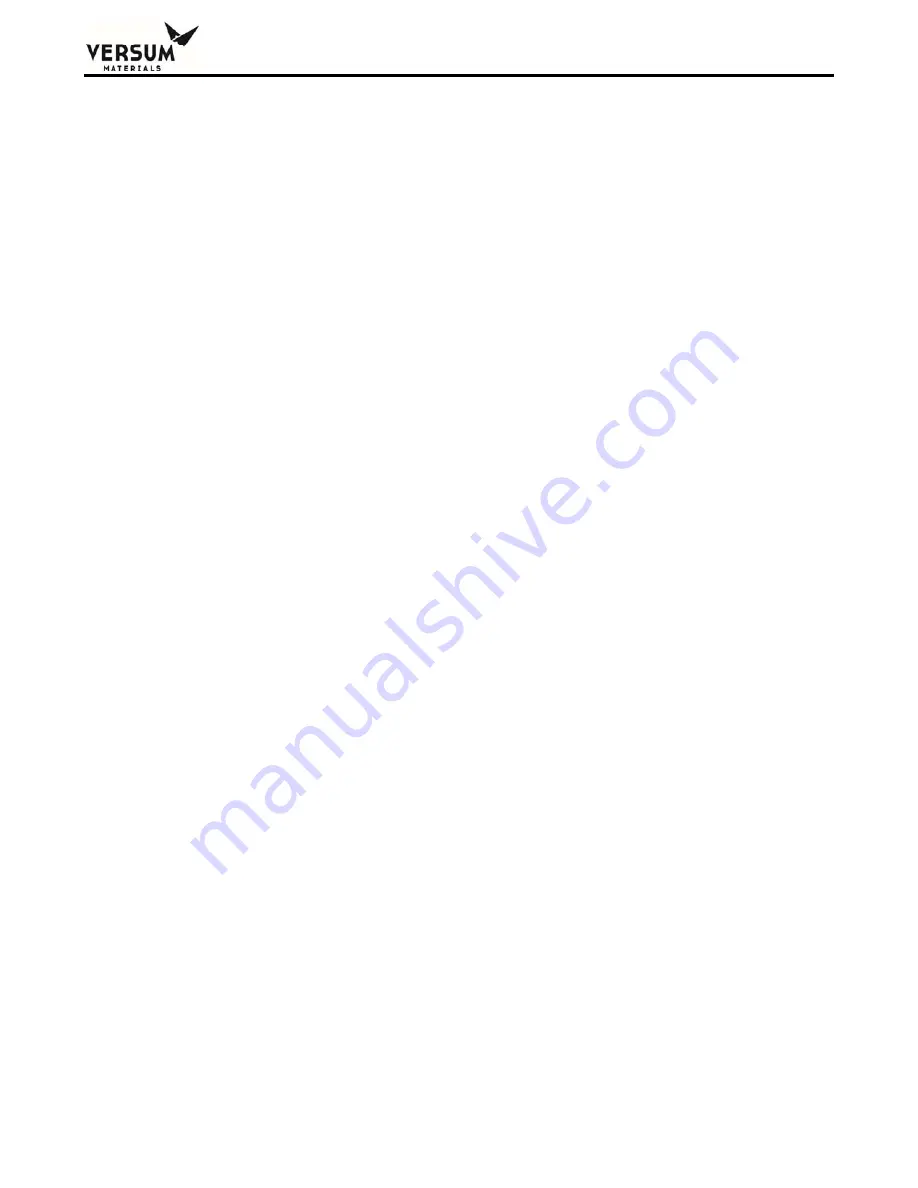
_______________________________________________________________________________________________________________
MNL000446.doc
Revision 00
09/19/2016
© Versum Materials, Inc. as of the revision and date shown. All rights reserved.
Confidential and Proprietary Data
Page
-
23
This option starts the Line purge sequence for the selected Branch. This operation is
used to reduce the amount of hazardous process gas in the Line to safe levels prior to
maintenance or other activities.
The purge sequence tests for adequate purge pressure and vacuum, then initiates a series
of purge cycles of the Line process piping to reduce process gas concentration to safe
levels.
The number of purge cycles depends on the type of process gas. Minimum values are
built into the sequence. Cycles may be increased (See System Configuration in Section
8.8 of this manual), but not reduced below the minimum.
Flow Purge (Optional Process Line Purge)
This purge sequence consists of flowing purge gas continuously through the Line and
downstream process line. The gas is vented through a vent valve at the tool or through
the tool itself. This purge process is used to reduce the concentration of hazardous gas
to safe levels to allow maintenance to be performed on the process line.
The customer must establish a purge time to reach a safe level that is based on the flow rate,
line length and type of gas. The vented gas should be monitored for residual hazardous gas
concentration before maintenance is performed.
Line purging can also be performed using Manual Mode.
Rough Line Evacuation (Optional Process Line Purge)
This option starts a purge and evacuation sequence for both the selected Branch and the
process line to the tool isolation valves. The purpose of this sequence is to remove the
major portion
of the hazardous process gas from the Distribution System Branch
and
downstream process line
through the vent system of the Distribution System. It does not
reduce the concentration of hazardous gas to safe levels for maintenance activities