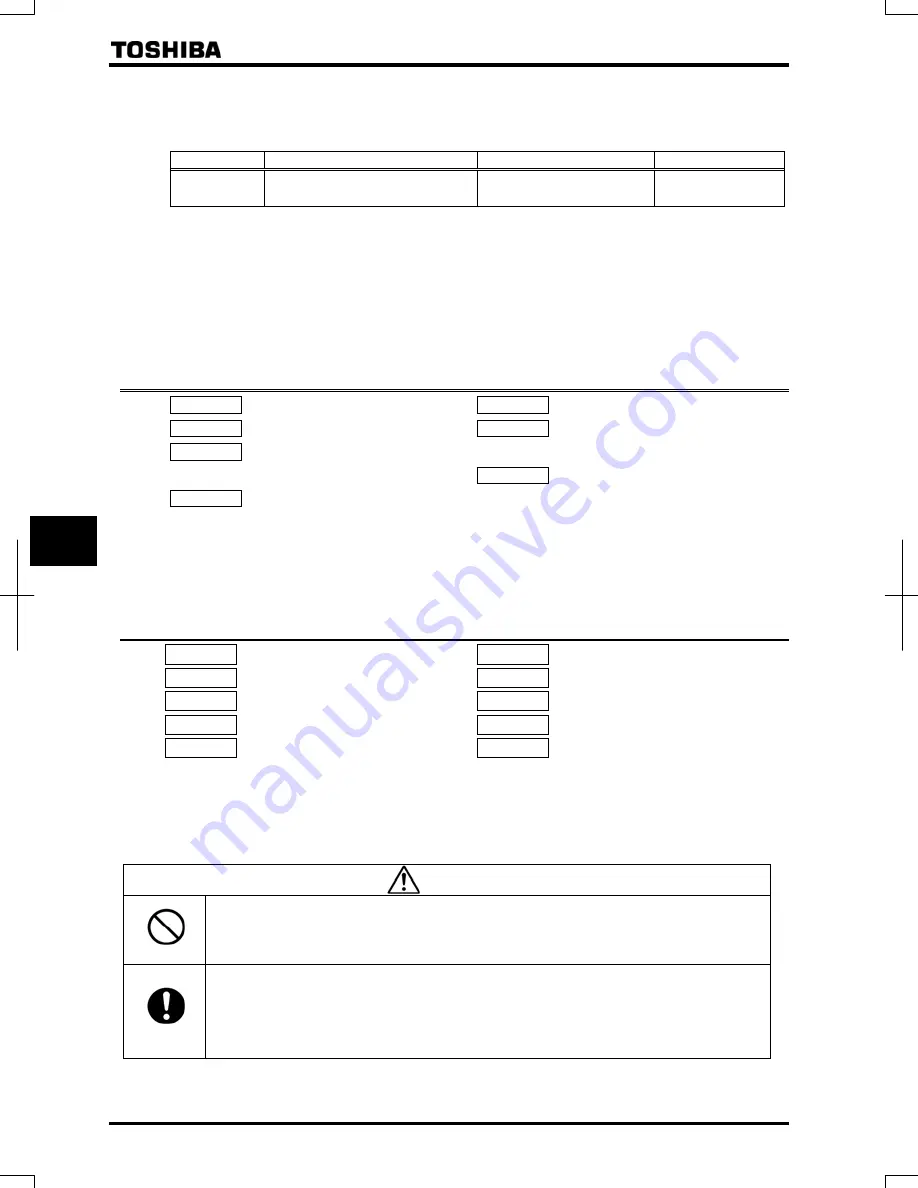
E6581442
F-38
6
The characteristic of the feedback value can also be reversed by means of a signal from an external device.
Example: To use the S3 terminal as a PID normal/reverse characteristic switching signal input terminal
Title
Function
Adjustment range
Default setting
Input terminal function selection7(S3)
~
(positive logic)
(negative logic)
6) Setting the time elapsed before PID control starts
You can specify a waiting time for PID control to prevent the inverter from starting PID control before the control
system becomes stable, for example, after start-up.
The inverter ignores feedback input signals, carries out operation at the frequency determined by the value of
processing for the time specified by
f369
and enters the PID control mode after a lapse of the specified time.
6.21
Stop position control function
: V/f control mode selection
:
PID control switching
: PID control feedback control
signal selection
: Proportional (P) gain
: Number of PG input pulses
: Selection of number of PG
input phases
: Simple positioning
completion range
For details, see Instruction Manual (E6581319) specified in Section 6.41.
6.22
Setting motor constants
: Auto-tuning 1
: Slip frequency gain
: Auto-tuning 2
: Motor rated capacity (motor nameplate)
: Motor rated current(motor nameplate)
: Motor rated rotational speed (motor nameplate)
: Motor constant 1 (torque boost)
: Motor constant 2 (no-load current)
: Motor constant 3 (leak inductance)
: Motor constant 4 (rated slip)
When selecting automatic torque boost and vector control (i.e., when setting the parameter
to
,
,
,
or
.
By default,
is set to
(v/f constant control)), be sure to set every parameter concerned in accordance with the
flowchart on the next page.
Warning
Prohibited
The inverter is tuned automatically (auto-tuning
=
) when the inverter is started for the first time
after setup. During auto-tuning, which takes about 3 minutes from several seconds as each model, the
motor is energized, although it is standing still.
Mandatory
Provide cranes and hoists with sufficient circuit protection such as mechanical braking.
Without sufficient circuit protection, the resulting insufficient motor torque during tuning could create a risk
of machine stalling/falling.
Be sure to set every parameter concerned in accordance with the flowchart on the next page. Failure to
do this may cause the inverter not to control the motor properly, and therefore cause the motor not to
deliver the desired performance.
Содержание TOSVERT VF-AS1 Series
Страница 238: ...E6581442 I 7 9 ...
Страница 261: ...E6581442 J 13 10 VFAS1 4200KPC 4280KPC VFAS1 4355KPC 4400KPC 4500KPC ...
Страница 321: ...E6581442 M 3 13 Continued overleaf ...