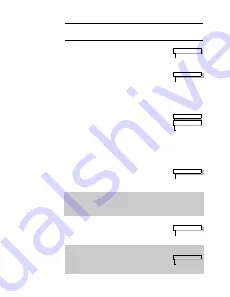
4-10
Operating the Converter
590+ Series DC Digital Converter
Caution
During the following set-up instructions, be ready to STOP the converter should the
motor try to overspeed.
Step 12
Set the Speed Setpoints so that the value of the SPEED
SETPOINT is about 5%, 0.5V at setpoint input (terminal A8).
Perform the next operation with ARM VOLTS FBK selected for
the SPEED FBK SELECT parameter (because it is hard-wired
and therefore the sign will be correct). Select it now.
Slowly increase the MAIN CURR.LIMIT parameter up to a maximum
of about 20%. The motor should begin to rotate if all connections are
made correctly. The motor speed will settle at about 5% of full speed
if the motor is unloaded. Check the feedback from the Tachometer or
Encoder using the appropriate Diagnostic menu.
Now stop the drive. Re-instate your selection for the SPEED FBK SELECT parameter (if
other than ARM VOLTS FBK) and perform the same test again.
If the test was successful perform a PARAMETER SAVE and go to 14. If just direction of
rotation is wrong, go to 13, otherwise check as below.
If 5% speed (approx.) is exceeded and the motor continues to
accelerate a reversed connection is implied, decrease the MAIN
CURR.LIMIT parameter to zero.
Step 12.1
Reversed Connections - Analog Tachogenerator:
Open the main contactor and switch off all supplies, then correct the connections.
If the motor is turning in the correct direction, reverse the tachogenerator
connections only.
If the motor is turning in the wrong direction, reverse the field connections only.
Step
12.2
Reversed Connections - MICROTACH/Encoder:
Open the main contactor.
If the motor is turning in the right direction, change over
the ENCODER SIGN parameter.
If the motor is turning in the wrong direction, switch off all
supplies then reverse the field connections only.
Re-connect the supplies if disconnected and repeat the test from the beginning.
If the motor still runs out of control, check the tachogenerator and the wiring continuity. In the
case of the MICROTACH there are two LED's on the MICROTACH option board, both LED's
should be ON indicating healthy operation of the wiring and tacho. If in doubt about the
operation of the tachogenerator either Analog or MICROTACH during this test, monitor
terminal A7 with respect to signal ground on a meter. This will show if a feedback is present.
Note:
If the drive trips on speed feedback alarm with
tachogenerator feedback of the correct polarity, check the
armature voltage calibration.
Check the SPEED FBK SELECT. This could be set incorrectly
allowing the drive to run open loop.
If the motor does not turn at all when the MAIN CURR.LIMIT is
increased to 20%, check the CURRENT FEEDBACK parameter to
verify that current is flowing into the armature. If no current is
flowing, switch off and check the armature connections.
Is the motor connected to the drive?
Verify that calibration has been carried out correctly.
MMI Menu Map
1
DIAGNOSTICS
SPEED SETPOINT
MMI Menu Map
1
CONFIGURE DRIVE
SPEED FBK SELECT
MMI Menu Map
1
SETUP PARAMETERS
2
CURRENT LOOP
MAIN CURR.LIMIT
MMI Menu Map
1
CONFIGURE DRIVE
ENCODER SIGN
MMI Menu Map
1
CONFIGURE DRIVE
SPEED FBK SELECT
MMI Menu Map
1
DIAGNOSTICS
CURRENT FEEDBACK