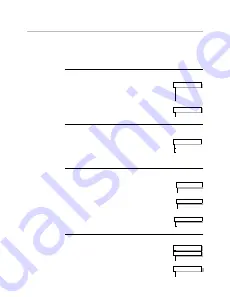
Operating the Converter
4-7
590+ Series DC Digital Converter
Initial Start-up Routine
Complete steps 1 to 18, including steps 16 and 17 as appropriate.
Note:
This routine assumes that the Converter’s control terminals are wired as shown in the
Minimum Connection Requirements drawings in Chapter 3. The field is “Enabled” and is
in Voltage Control (default settings).
IMPORTANT:
Do not change any of the previously made calibration settings once the main contactor is
energised.
Step 1
Normally, the setpoint ramp input at control terminal A4 is the speed reference source.
Use the Operator Station to display the value of the ANIN 3 (A4).
Vary the setpoint potentiometer and observe the input voltage display
change.
Additional Setpoint Inputs may also appear at ANIN 1 (A2) and ANIN
2 (A3). Check these if present.
The sum of all the setpoints is given by the value of the SPEED
SETPOINT parameter, and is also output at terminal A8.
Step 2
Use the Operator Station to check the external current clamp settings (refer to Chapter
6: “Programming Your Application” - ANALOG INPUTS for setting details):
x
If using a single external clamp, C6 low (0V):
Check that ANIN 5 (A6) is +10V or is adjustable up to
+10V.
x
If using dual external clamps, C6 high (+24V):
Check the ANIN 5 (A6) is at +10V or is adjustable up to +10V and that ANIN 4 (A5)
is at -10V or is adjustable up to -10V.
Step 3
If possible, check the speed feedback by rotating the shaft manually in the forward
direction.
x
Analog Tachogenerator:
The voltage at G3 (DC Tach Input) should go positive.
x
MICROTACH/Encoder
The ENCODER parameter should give a positive reading.
Also check the SPEED FEEDBACK parameter is reading a positive
value. If there is no feedback signal from the Microtach, verify that
both LEDs on the Microtach Option Board are illuminated. If either
LED is extinguished, check that 24V is applied to the Microtach and
all ancillary products, and that the fibre optic transmission length is not exceeded.
Step 4
Scroll through the SETUP PARAMETERS menu and take a note of the MAIN CURR.
LIMIT parameter’s value. You will need this later.
Set the MAIN CURR. LIMIT parameter to 0.00%.
Select the correct setting for the SPEED FBK SELECT.
Note:
Save any parameters that have been changed. Refer to Chapter
5: “The Operator Station” - How to Save, Restore and Copy your
Settings.
MMI Menu Map
1
DIAGNOSTICS
ANIN 1 (A2)
ANIN 2 (A3)
ANIN 3 (A4)
MMI Menu Map
1
DIAGNOSTICS
SPEED SETPOINT
MMI Menu Map
1
DIAGNOSTICS
ANIN 4 (A5)
ANIN 5 (A6)
MMI Menu Map
1
DIAGNOSTICS
TACH INPUT (B2)
MMI Menu Map
1
DIAGNOSTICS
ENCODER
MMI Menu Map
1
DIAGNOSTICS
SPEED FEEDBACK
MMI Menu Map
1
SETUP PARAMETERS
2
CURRENT LOOP
MAIN CURR. LIMIT
MMI Menu Map
1
CONFIGURE DRIVE
SPEED FBK SELECT