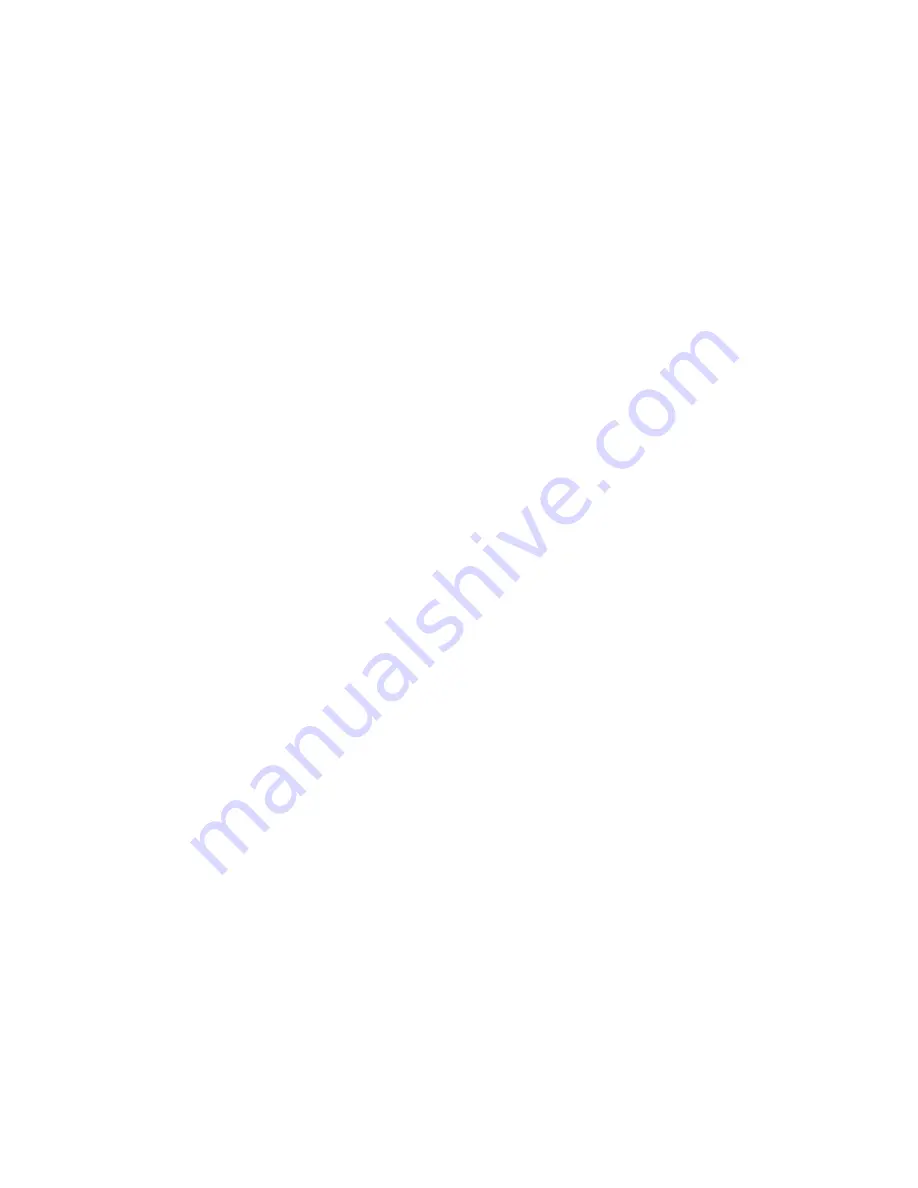
DRIVE SETUP AND ADJUSTMENT
60
elevator speed. Effective only when logic
input A1TB1-10 is active. Selecting this ramp
rate will override Rates 1 or 2.
Function #179
Decel #3 Time
Units: SEC
Range: 0.50 – 15.00
Default 5.00
Total deceleration time in seconds for S-curve
ramp #3 from rated speed to zero speed.
Effective only when logic input A1TB1-10 is
active. Selecting this ramp rate will override
Rates 1 or 2.
Function #180
Accel #3 %S
Units: %
Range: 0.1 – 100.0
Default: 25.0
The percent of time that will be spent in the
controlled jerk or S-portion of the timed ramp
curve during ramped acceleration #3. A
percent S of 0.1% corresponds to almost all
linear acceleration. A percent S of 100% will
make the S-curve #3 smooth with no linear
acceleration portion.
Function #181
Decel #3 %S
Units: %
Range: 0.1 – 100.0
Default: 25.0
The percent of time that will be spent in the
controlled jerk or S-portion of the timed ramp
curve during ramped deceleration #3. A
percent S of 0.1% corresponds to almost all
linear deceleration. A percent S of 100% will
make the S-curve #1 smooth with no linear
deceleration portion.
Function #182
Invert Alarm Relay
Units: logic
Range: 0 (Off) – 1 (On)
Default: 0 (OFF)
Alarms are classified as non-critical faults
detected by the DSD 412 that pose no
immediate need to stop operation. The Alarm
output relay K2 (on the Drive Control PCB,
A1) is reserved for non-critical fault
indications. It has a normally open contact
wired to A1TB1-38 and 39). With function 182
set to 0 (OFF), the default, relay K2 will pick-
up, closing the contact on the occurrence of a
non-critical fault. With function 182 set to a 1
(ON), the relay will be picked-up during
normal operating conditions and drop out on
the occurrence of a non-critical fault or Alarm.
Alarms are presently identified as drive over-
temperature or thermistor failure, motor or
transformer thermostat over-temperature, and
motor overload trip. Other conditions may be
selectable to be alarms or critical faults.
Содержание DSD 412
Страница 1: ...DSD 412 DC Elevator Drive Technical Manual CS00407 rev 06...
Страница 6: ...6...
Страница 102: ...MAINTENANCE 102 Figure 24 Connector and E prom Locations...
Страница 103: ...MAINTENANCE 103 Figure 25 Test Point Locations...
Страница 115: ...OUTLINE DRAWING 100A 115 Figure 26 Drive Chassis Outline DSD 412 100 Amp...
Страница 116: ...OUTLINE DRAWING 190A 116 Figure 27 Drive Chassis Outline DSD 412 195 Amp...
Страница 117: ...OUTLINE DRAWING 300A 117 Figure 28 Drive Chasis Outline DSD 412 300 Amp...
Страница 118: ...LAYOUT DRAWING 100A 118 Figure 29 Layout DSD 412 100 Amp A3 A1 A2 A2 L1 NEG GND L2 L3 POS...
Страница 119: ...LAYOUT DRAWING 195A 119 Figure 30 Layout DSD 412 195 Amp A3 A1 A2 A2...
Страница 120: ...LAYOUT DRAWING 300A 120 Figure 31 Layout DSD 412 300 Amp A3 A1 A2 A2...
Страница 121: ......