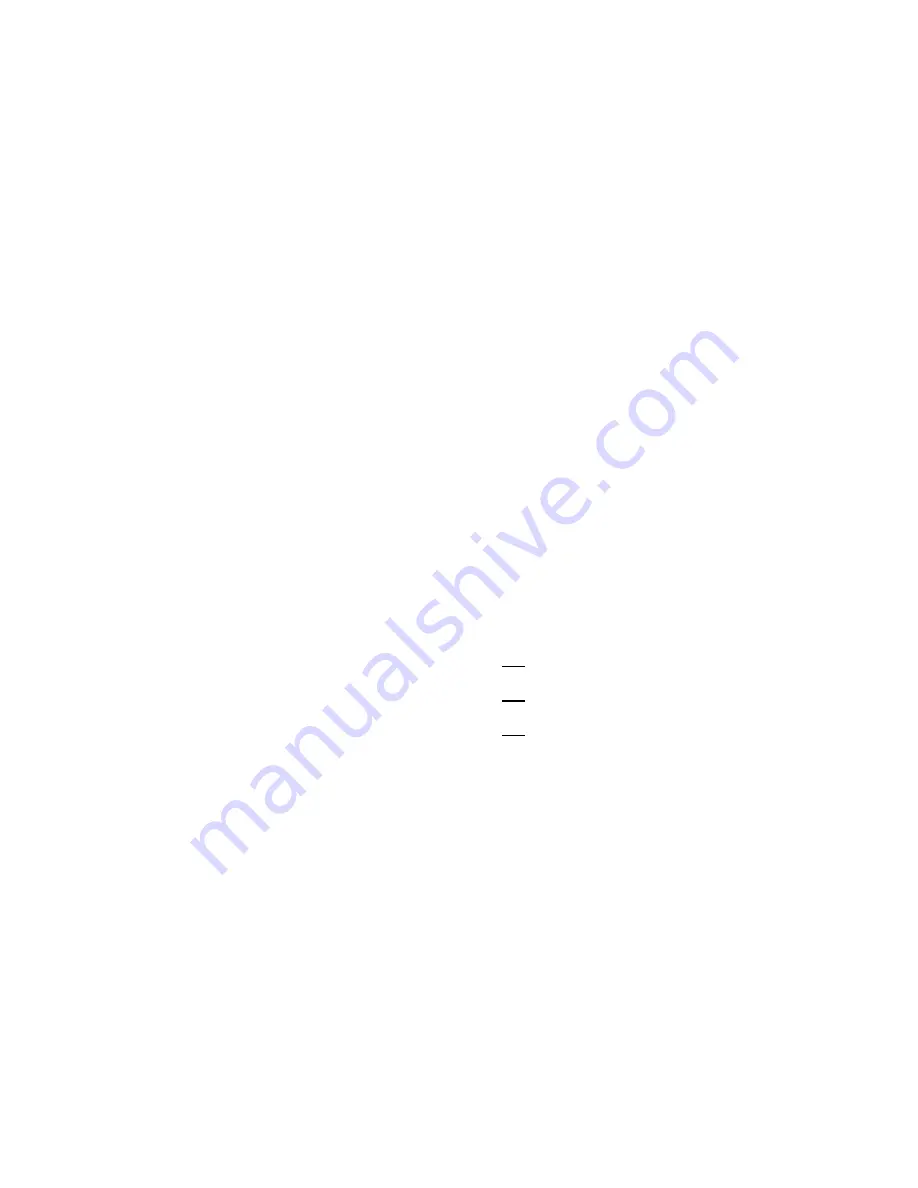
DRIVE SETUP AND ADJUSTMENT
57
Function #114
Pre-Torque Enable
Units: logic
Range: 0 (Off) – 1 (On)
Default: 0 (Off)
Setting this value to 1, on, enables the pre-
torque function to operate. The pre-torque
value from the analog pre-torque input will be
multiplied by function 87 and used to pre-
stress the velocity error integrator to that
armature current per unit value upon starting.
If function 110 is set to 3 for serial link
control, the pre-torque reference input will be
from the serial link message. The adjusted
pre-torque value used at the start of an
elevator run may be viewed during the run via
function 603...If pre-torque is not used, leave
this function set to 0, 'OFF'.
Function #115
Run-Up/Run-Down Select
Units: logic
Range 0 (Off) – 1 (On)
Default: 0 (Off)
This function selects how the drive will
determine the RUN Direction when REF-
MODE function 110 is set for internal pre-set
speeds. When this is set to 0 (OFF)
24V relay logic input A1TB1-8 will be a
Hardware RUN command. A1TB1-50 will be
the UP (Logic low or OFF), or Down (+24V
or ON) command. When this is set to 1 (ON)
24 V relay logic input at A1TB1-8 will be a
Run-Up command A1TB1-50 will be a Run-
Down command. If REF-MODE function 110
is set to 1 or 3 for following bi-directional
external analog or serial link velocity
commands, the polarity of that signal will
always be followed. In that case, either
A1TB1-8 or A1TB1-50 may be used as a
Hardware Run command input (but not both).
Function #116
Decel Rate Latch
Units: logic
Range 0 (Off) – 1 (On)
Default: 0 (Off)
When set, this control bit causes the decel
ramp rate active at the start of decel to remain
in effect until the decel sequence is
completed. This function will momentarily
override logic input commands at A1TB1-10
and A1TB1-51.
Function #120
Speed Error Detect
Units: SEC
Range: 0.0 – 5.0
Default: 0.5
This value sets the time sensitivity of the
Speed- Error-is-Low detector. This is a useful
indicator to tell when/if the drive is following
the velocity reference properly. Exceeding
the set limits of this detector does not shut the
drive down. The detector results can be sent
to a logic output. See also, function 99, 100,
121 and the description of logic outputs 183
through 187.
Function #121
Speed Error Threshold
Units: %
Range: 0.0 – 15.0
Default: 2.0
See function 120. This value sets the
magnitude sensitivity of the Speed-Error-is-
Low Detector. Units are a percent of rated
speed function 17.
Function #130
ARB Mode
Units: -
Range: 0 – 2
Default: 0
This selects between 3 possible Anti-Rollback
operating modes.
"0"
to disable all Anti-Rollback features. Only
E-Reg will be engaged
"1"
to enable Anti-Rollback when the drive is
started.
"2"
to enable Anti-Rollback when starting the
drive and when the velocity again comes to a
stop at the next landing.
Function #131
ARB Bandwidth
Units: RAD
Range: 1 – 30
Default 6.
Determines the gain of the velocity and
position regulator when ARB is ON. This is
the unity gain crossover frequency in
Radians/sec. Increasing this setting will
cause the position loop to respond faster with
less accumulated position error.
Содержание DSD 412
Страница 1: ...DSD 412 DC Elevator Drive Technical Manual CS00407 rev 06...
Страница 6: ...6...
Страница 102: ...MAINTENANCE 102 Figure 24 Connector and E prom Locations...
Страница 103: ...MAINTENANCE 103 Figure 25 Test Point Locations...
Страница 115: ...OUTLINE DRAWING 100A 115 Figure 26 Drive Chassis Outline DSD 412 100 Amp...
Страница 116: ...OUTLINE DRAWING 190A 116 Figure 27 Drive Chassis Outline DSD 412 195 Amp...
Страница 117: ...OUTLINE DRAWING 300A 117 Figure 28 Drive Chasis Outline DSD 412 300 Amp...
Страница 118: ...LAYOUT DRAWING 100A 118 Figure 29 Layout DSD 412 100 Amp A3 A1 A2 A2 L1 NEG GND L2 L3 POS...
Страница 119: ...LAYOUT DRAWING 195A 119 Figure 30 Layout DSD 412 195 Amp A3 A1 A2 A2...
Страница 120: ...LAYOUT DRAWING 300A 120 Figure 31 Layout DSD 412 300 Amp A3 A1 A2 A2...
Страница 121: ......