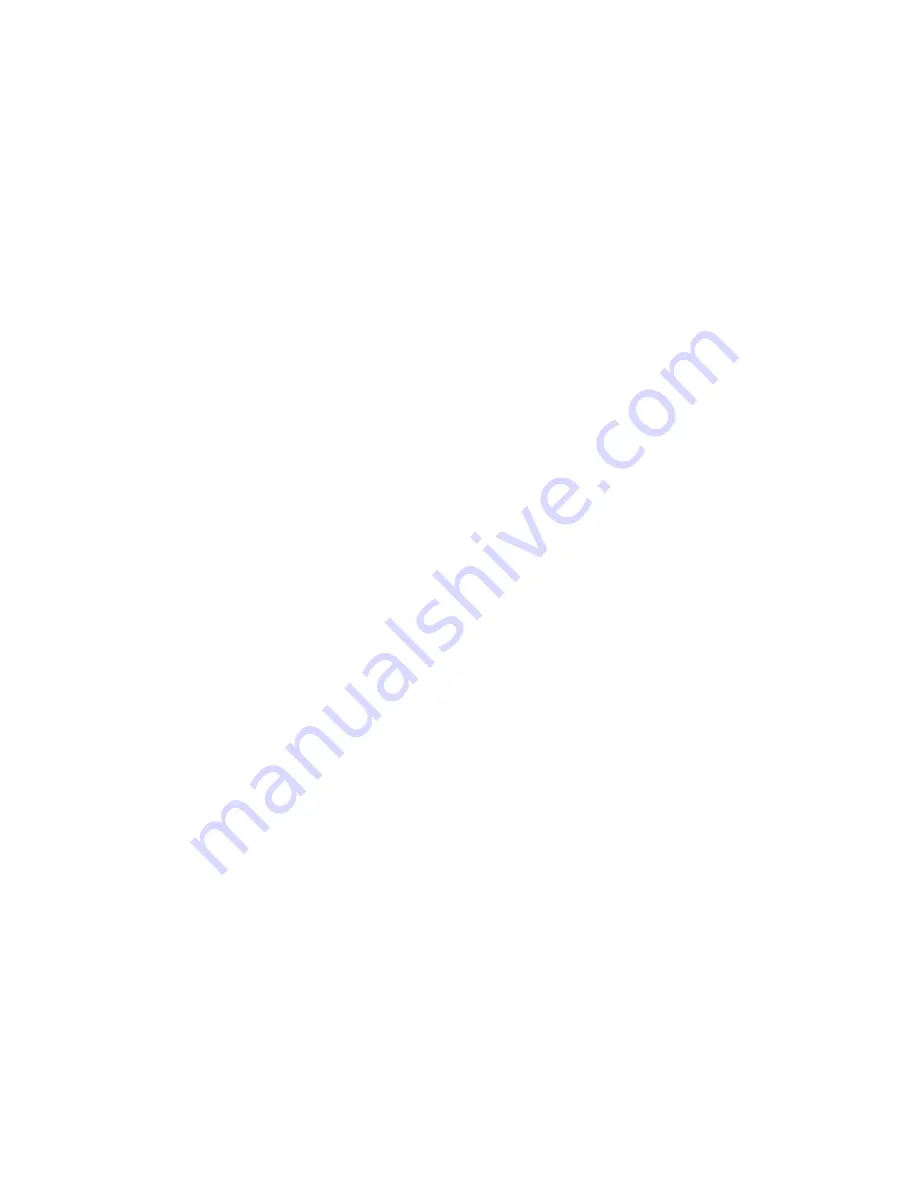
DRIVE SETUP AND ADJUSTMENT
47
There are connection provisions for using a
user supplied voltage source.
Analog Velocity Follower
The elevator car controller provides an analog
velocity reference to the drive at A1TB1-63
and A1TB1-68. The signal may be bi-polar
+/-10 VDC to indicate speed and travel
direction, or a positive only unipolar signal
with the direction of travel selected by logic
commands. See descriptions of function 110
and function 115. In most cases the signal
profile will be adjusted by the car controller for
precise landing positioning. The velocity
reference passes directly to the E-Reg closed
loop velocity controller, except for an internal
rate limiter function 21 to buffer any
unexpected electrical noise. Start and Stop
commands are via 24VDC logic inputs. The
analog velocity reference signal may be
adjusted using function 82 'Gain' or function
86 'Bias'.
Internal Preset Speed & Profile
Generator
The elevator car controller provides 24VDC
logic input commands to select one of 7 pre-
determined running speeds. The DSD 412
drive generates a smooth S-Curve
acceleration profile to transition between
speed selections. Either of three separately
adjustable ramp times may be selected. The
direction of travel may be determined by
either a single (up/dn) or dual (Run-Up / Run-
Dn) logic commands. There are provisions for
allowing or disallowing non-stop direction
reversals. The internal pre-set speed-
operating mode is selected by setting #110 to
2. The speed sensitivity of pre-set speeds is
altered by #82. Set #82 to 1.00 for proper
calibration.
Serial Link Follower
The elevator car controller provides the
equivalent of an analog reference command
over a digital serial link. The drive returns
operating status conditions and messages.
Primary Start and Stop commands are 24VDC
logic for redundant safety. This operating
mode is selected by setting #110 to 3. The
speed sensitivity of the serial velocity
reference may be adjusted using function 82.
Maintainance mode - Armature Voltage
Feedback
A DC motor with rated field current applied will
produce rated armature voltage when
spinning at rated speed. This will result in
speed regulation in the range of 5%. When in
this mode, operation over base speed will not
be possible as the field weakening is inhibited.
When this mode is enabled it will still be
possible to monitor the feedback from the
encoder although it will not used for speed
regulation. Due to the nature of this mode of
operation the speed regulator gain will be
defaulted at 2 radians to prevent unstable
operation (it shouldn't require to be changed
from this point). A new parameter F#38 was
added for this purpose so it won't be required
to modify the normal speed regulator gains
F#39 and #40, when it switched. See
descriptions for functions 112 and 113 for
setting this mode.
Pre-Torque
When enabled by function 114, the speed
error integrator will be pre-conditioned by the
supplied pre-torque signal before starting E-
Reg. This will cause motor armature current
to begin at a magnitude proportional to the
pre-torque command to prevent elevator
motion or rollback when the elevator brake is
released. The pre-torque signal will be from
either an analog or serial link digital source as
selected by software Mode switch function
110.
Current Ramp-Down
When the DSD 412 drive is told to cease
operation by removal of the Run logic
command, (and after Brake Drop time if that
function is engaged) the armature current
reference ramps down to zero at a constant
rate controlled by function 85. When
armature current ramp-down is complete, the
contactor will be opened. In the event that the
contactor opens unexpectedly, as reported by
the feedback contact at A1TB1-7, or in the
event of a severe drive fault, there will be no
timed delay for current ramp-down.
Содержание DSD 412
Страница 1: ...DSD 412 DC Elevator Drive Technical Manual CS00407 rev 06...
Страница 6: ...6...
Страница 102: ...MAINTENANCE 102 Figure 24 Connector and E prom Locations...
Страница 103: ...MAINTENANCE 103 Figure 25 Test Point Locations...
Страница 115: ...OUTLINE DRAWING 100A 115 Figure 26 Drive Chassis Outline DSD 412 100 Amp...
Страница 116: ...OUTLINE DRAWING 190A 116 Figure 27 Drive Chassis Outline DSD 412 195 Amp...
Страница 117: ...OUTLINE DRAWING 300A 117 Figure 28 Drive Chasis Outline DSD 412 300 Amp...
Страница 118: ...LAYOUT DRAWING 100A 118 Figure 29 Layout DSD 412 100 Amp A3 A1 A2 A2 L1 NEG GND L2 L3 POS...
Страница 119: ...LAYOUT DRAWING 195A 119 Figure 30 Layout DSD 412 195 Amp A3 A1 A2 A2...
Страница 120: ...LAYOUT DRAWING 300A 120 Figure 31 Layout DSD 412 300 Amp A3 A1 A2 A2...
Страница 121: ......