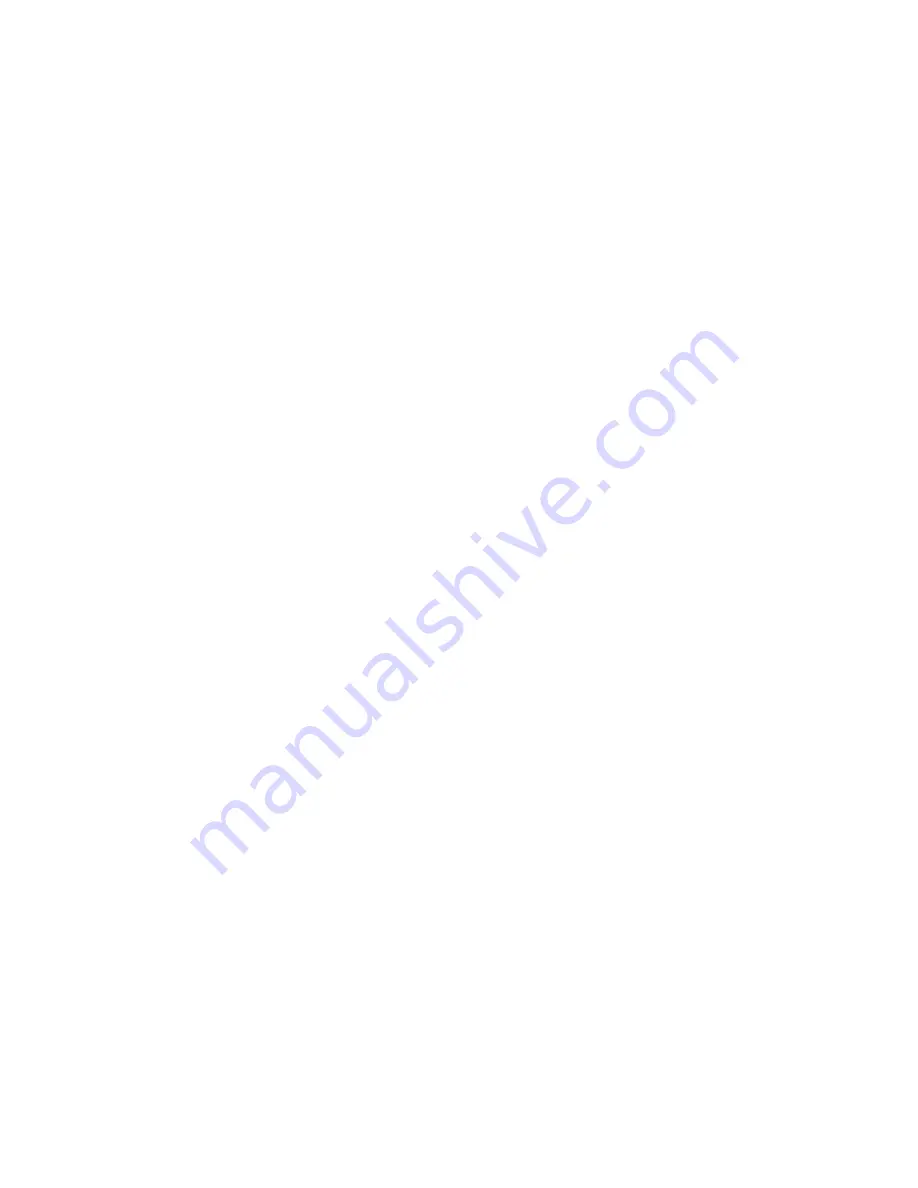
DRIVE SETUP AND ADJUSTMENT
53
Function #64
Low Speed Threshold
Units: %
Range: 0.1 – 100.0
Default: 2.0
This entry sets the speed threshold where the
At-Low-Speed indicator will turn ON and OFF.
This can be used to indicate when the
elevator is moving below the door pre-opening
speed. See programmable output function F
or M at functions 183 through 187. The
adjustment value is percent of rated maximum
speed as set by function 17. Hysteresis is
5% of the set value.
Function # 80
Over-Speed Test
Units: LOGIC
Range: 0 (Off) – 1 (On)
Default: 0 (OFF)
This is a logic input that is used to activate an
over-speed multiplier value, (function 81).
When running the test increase F#12 to
prevent the drive from faulting on Overspeed
(Fault 97).
Function # 81
Over-Speed Mult
Units: —
Range: 1.00 – 1.50
Default: 1.00
This is the value of speed reference multiplier
that will be used to run an elevator over-speed
test when function 80 is ON. This function
also multiplies function 82.
Function # 82
Reference Mult iplier
Units: —
Range: 0.500 – 2.000
Default: 1.000
This value is a multiplier for external analog or
serial link velocity references. It may be used
to adjust the actual calibration of the reference
signals or to cause the elevator to run at a
different speed from a +/-10 volt analog or
other full-scale serial reference command.
The elevator will run at Rated Speed (function
11 and function 17) from an analog reference
of 10V, when function 82 is set to 1.000, and
function 80 is 'OFF'.
Function # 83
Motor Ovld Tout
Units: SEC
Range: 2.0 – 500.0
Default: 48.0
This value shapes the motor overload time-
out curve.
Function # 84
Motor Overload Level
Units: PU
Range: 0.50 – 2.00
Default: 1.15
This value sets the threshold level where the
motor overload function will begin to operate.
Sustained motor current above this value will
eventually cause an overload trip according to
the time set in #83.
Function # 85
I Decay Ramp
Units: SEC
Range: 0.01 – 2.500
Default: 0.200
This value controls the rate of decay of motor
armature current during normal elevator
stops. This helps to prevent brake ‘thumping’
when the drive is shut down and the brake is
required to hold the car. The drive Run logic
command must remain active until the
elevator comes to a stop and the mechanical
brake is set. Armature current ramp-down will
begin after the RUN command is removed
from the drive. When the ramp-down is
complete, the contactor will be told to open.
NOTE: The Drive Enable command must
remain ON and the elevator Safety-Chain
must remain closed until after the contactor
actually opens for this feature to work
properly.
Function # 86
Analog Speed Ref Zero
Units: PU
Range: -0.02 – 0.02
Default: 0.00
At zero speed if the motor is creeping it may
be necessary to adjust this parameter to
compensate. Adjust this parameter until
motion is stopped at zero speed. After
adjusting the low end of the profile it may also
be necessary to adjust the reference at the
top end of the profile. Refer to function 82 to
set the speed reference gain.
Содержание DSD 412
Страница 1: ...DSD 412 DC Elevator Drive Technical Manual CS00407 rev 06...
Страница 6: ...6...
Страница 102: ...MAINTENANCE 102 Figure 24 Connector and E prom Locations...
Страница 103: ...MAINTENANCE 103 Figure 25 Test Point Locations...
Страница 115: ...OUTLINE DRAWING 100A 115 Figure 26 Drive Chassis Outline DSD 412 100 Amp...
Страница 116: ...OUTLINE DRAWING 190A 116 Figure 27 Drive Chassis Outline DSD 412 195 Amp...
Страница 117: ...OUTLINE DRAWING 300A 117 Figure 28 Drive Chasis Outline DSD 412 300 Amp...
Страница 118: ...LAYOUT DRAWING 100A 118 Figure 29 Layout DSD 412 100 Amp A3 A1 A2 A2 L1 NEG GND L2 L3 POS...
Страница 119: ...LAYOUT DRAWING 195A 119 Figure 30 Layout DSD 412 195 Amp A3 A1 A2 A2...
Страница 120: ...LAYOUT DRAWING 300A 120 Figure 31 Layout DSD 412 300 Amp A3 A1 A2 A2...
Страница 121: ......