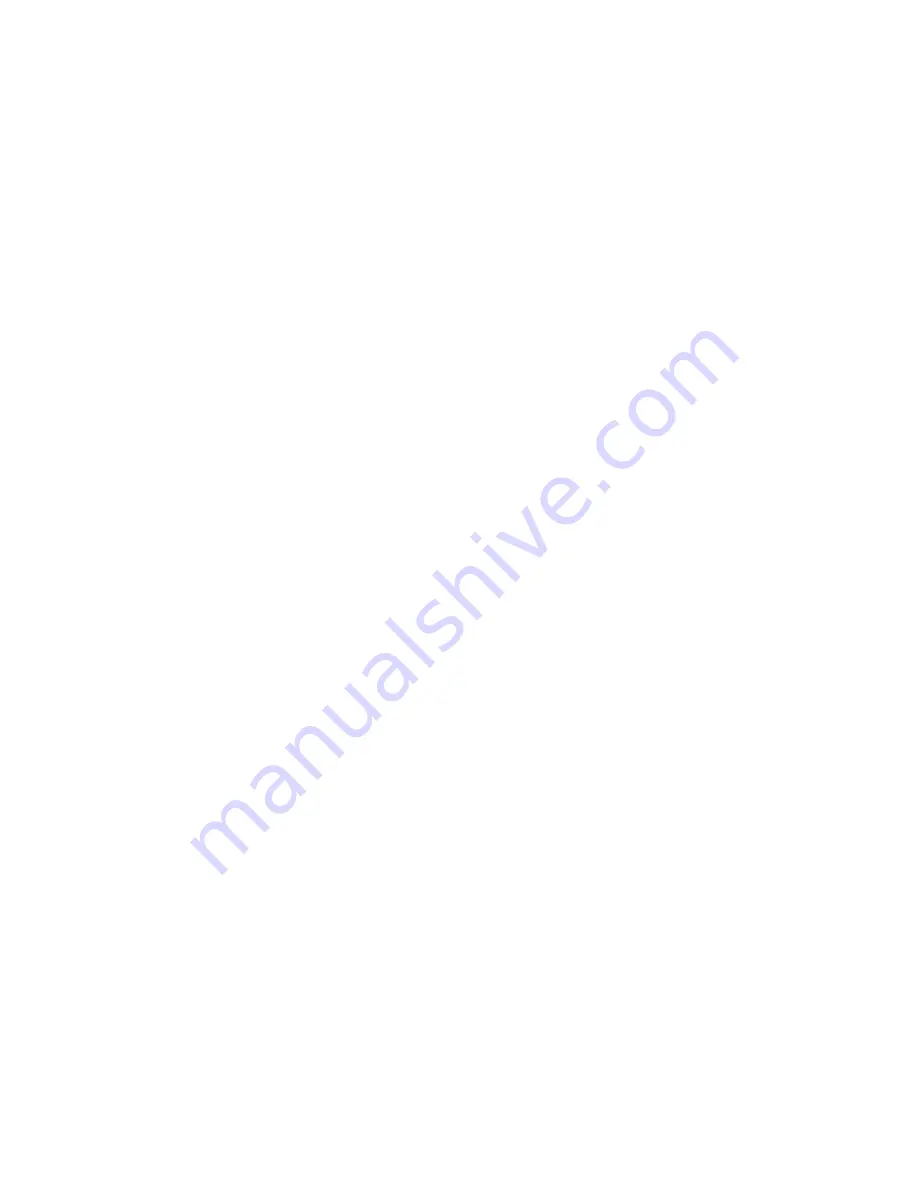
DRIVE SETUP
86
velocity reference is increased to again
be larger than the threshold set by
#133. If #63 is set too high, there may
be a jerk felt as the car comes to rest
and the control switches to the ARB
zero speed / position hold mode. If #63
is set too low, minor disturbances and
movement may delay and possibly
prevent control transfer to the ARB hold
mode because the measured encoder
speed over a relatively short measuring
time appears to not fall below the
threshold value. Set #63 to the lowest
value that yields repeatable results.
Using Drive Stand-By Power Reduction
(DSPR)
Elevators often sit idle for many hours during
a 24-hour day. Even though the DSD 412
drive can be set up to reduce motor field
current to a stand-by level, a significant
amount of power is continually lost by
having the 3-phase main power transformer
energized and cooling fans running. Now it
is possible to set a timer so that when the
elevator has not been used for a length of
time, an external contactor can disconnect
the main transformer and turn cooling fans
off. When car controller logic recognizes
that a new elevator call has been placed and
asserts the Drive and Field Enable contact
at TB1-9, the drive will re-enable the 3-
phase primary power, resynchronize to the
power line and restart cooling fans. While 3-
phase power is OFF motor field current will
be zero amperes, regardless of the setting
of Standby Amps set at #53.
The DSPR feature is programmable by
selection of output option L on relay K4.
See table 4.2.3. The time delay before
power is turned OFF is adjusted at #88,
DSPR Delay. This timer is held in reset
whenever the drive is enabled, and timing
for a delayed shutdown whenever the drive
is at rest and the Enable control line is
inactive. If the DSPR delay time value at
#88 is set to zero (0), the timing function is
defeated and power will remain continuously
ON. A pilot relay must be added to panel
wiring to operate a primary power contactor.
115 VAC control power to the drive must
remain ON for this feature to be operative.
Refer to installation diagrams supplied in
Section 2 at Figure(s) 2.1 for all suggested
electrical connections. Normal operation of
DSPR when power is first applied or when a
Dive Fault Reset is performed is that Relay
K4 will be de-energized, or will become de-
energized, turning main power OFF. It will
then energize/re-energize to turn 3-phase
power ON. Setting DSPR delay at #88 to
zero will not change that part of the
operation.
If DSPR is not wanted, or other external
logic prevents the 3-phase power from
actually turning OFF, the drive will not care
and continue to respond normally, except
that motor field current will go to zero during
a DSPR time-out. However, external relay
logic must not turn 3-phase power OFF
unexpectedly, or the drive will declare an
F406, F903 or F904.
NOTE:
PCU software in EPROM sockets
U13 & U14 must be labeled SA0404
(displayed by function #690), AND the
software in sockets U39 & U40 (displayed
by function #697) must be labeled SA0407
for the DSPR feature to be available.
Using Elevator Brake Controls
Two relay control outputs are provided
(Brake Lift, Brake Pick) by programmable
output selection functions #186 and #183.
Three timers are provided, Brake Pick #89,
Brake Drop #90, Must Stop #91. Suggested
wiring is shown in Figure 10: Drive Brake
Control Feature. Operation is as follows:
Elevator Start with Brake Control:
1. The drive is started by activating first the
ENABLE then RUN command lines.
The contactor will pick (pull in), and
when acknowledge, the drive will start
the current and velocity regulator by
priming it to provide pre-torque armature
current (if enabled). The internal
velocity reference will always start at
zero.
2. Once Start is confirmed, the Brake Lift
and Brake Pick lines will both become
active. This will apply full voltage to the
brake coil and cause the brake to lift.
3. The Brake Pick output will deactivate at
the end of Brake Pick time #89, and
release the internal velocity reference
clamp so that the drive can begin
acceleration. The Brake Lift output will
Содержание DSD 412
Страница 1: ...DSD 412 DC Elevator Drive Technical Manual CS00407 rev 06...
Страница 6: ...6...
Страница 102: ...MAINTENANCE 102 Figure 24 Connector and E prom Locations...
Страница 103: ...MAINTENANCE 103 Figure 25 Test Point Locations...
Страница 115: ...OUTLINE DRAWING 100A 115 Figure 26 Drive Chassis Outline DSD 412 100 Amp...
Страница 116: ...OUTLINE DRAWING 190A 116 Figure 27 Drive Chassis Outline DSD 412 195 Amp...
Страница 117: ...OUTLINE DRAWING 300A 117 Figure 28 Drive Chasis Outline DSD 412 300 Amp...
Страница 118: ...LAYOUT DRAWING 100A 118 Figure 29 Layout DSD 412 100 Amp A3 A1 A2 A2 L1 NEG GND L2 L3 POS...
Страница 119: ...LAYOUT DRAWING 195A 119 Figure 30 Layout DSD 412 195 Amp A3 A1 A2 A2...
Страница 120: ...LAYOUT DRAWING 300A 120 Figure 31 Layout DSD 412 300 Amp A3 A1 A2 A2...
Страница 121: ......