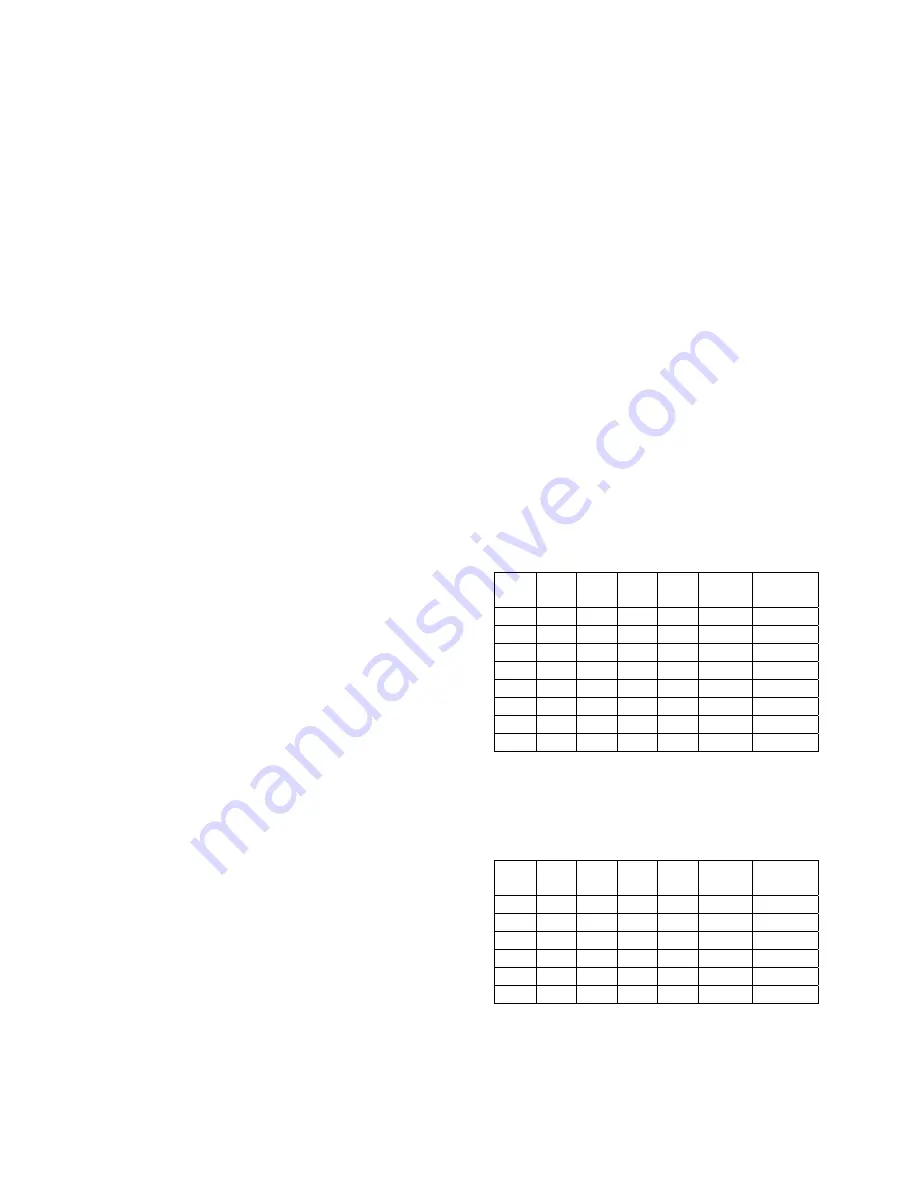
DRIVE SETUP AND ADJUSTMENT
58
Function #132
ARB Damping
Units: -
Range: 0.1 – 10
Default: 2.0
Adjusts damping of the position regulator
when ARB is ON. Increasing this setting will
cause a smoother but slower recovery of
position error. Reducing this setting will let
ARB recover a position error more quickly and
abruptly.
Function #133
ARB Speed Threshold
Units: %
Range: 0.0 – 10% (of rated speed)
Default: 0.0%
Determines the reference speed where ARB
will be turned OFF and E-Reg will be engaged
when the drive is started, if function 130 is set
to 1 or 2. This setting should be as low as
possible to prevent regulator transfer bumps
when starting, but it must be set high enough
to remain engaged during re-leveling or to
ignore a small analog zero reference offset
when using an external analog signal
reference.
Function #150
Binary/Progressive Pre-Set Speed Select
Units: logic
Max: 1 (BINARY)
Min: 0 (PROGRESSIVE)
Default: 1 (BINARY)
Determines the method for selecting pre-set
speeds from external relay logic applied to
A1TB1-11, 12, 52, 53 and 54)
Function #151 through #157
Pre-Set Speeds 1 through 7
Units: -
Range: 0.0 – 1900.0
Default: 0.0
These function values specify the elevator car
speed for each individual pre-set speed
setting. The units must agree with that set for
Rated Car Speed in function 17. [If feet per
minute is used at function 17, then the units
for function 151through 157 shall also be feet
per minute.] No value for function 151through
157 should be larger than that for function 17.
All values are positive numbers. The selected
reference speed and direction will be
determined by the setting of function 110,
115, 150, and 24V relay logic inputs. It is
certainly possible to connect the selection of
one or more pre-set speed logic input control
lines to also activate a different Ramp Rate #2
or #3. See also the Decel Rate Latch,
function 116. With careful thinking, one can
obtain many specific combinations of pre-set
speeds and Ramp Rates with a minimum of
relay contacts.
Note 1: Switch select inputs S0-S4 are 24V
logic input signals available on A1TB1 with
the following assignments:
S0
=
A1TB1-11
S1
=
A1TB1-53
S2
=
A1TB1-12
S3
=A1
TB1-54
S4
=
A1TB1-52
Note 2: For S0 – S4...
+18 - 24VDC (ON) = 1
<5VDC (OFF) = 0
Note 3: Connecting A1TB1-10 to A1TB1-11
will automatically select Ramp #3 with
selection of pre-set speed #1.
BINARY Preset Speed Operation
(#150) = 1 = ON
S4 S3 S2 S1 S0 SPD
#
ADJ
(#nn)
X X 0 0 0
ZERO NONE
X X 0 0 1 1 (151)
X X 0 1 0 2 (152)
X X 0 1 1 3 (153)
X X 1 0 0 4 (154)
X X 1 0 1 5 (155)
X X 1 1 0 6 (156)
X X 1 1 1 7 (157)
Table 5: Binary Preset Speed Select
PROGRESSIVE Preset Speeds
(#150) = 0 = OFF
S4 S3 S2 S1 S0 SPD
#
ADJ
(#nn)
0 0 0 0 0
ZERO NONE
0 0 0 0 1 1 (151)
0 0 0 1 0 2 (152)
0 0 1 1 0 3 (153)
0 1 1 1 0 4 (154)
1 1 1 1 0 5 (155)
Table 6: Progressive Preset Speed
Operation
Содержание DSD 412
Страница 1: ...DSD 412 DC Elevator Drive Technical Manual CS00407 rev 06...
Страница 6: ...6...
Страница 102: ...MAINTENANCE 102 Figure 24 Connector and E prom Locations...
Страница 103: ...MAINTENANCE 103 Figure 25 Test Point Locations...
Страница 115: ...OUTLINE DRAWING 100A 115 Figure 26 Drive Chassis Outline DSD 412 100 Amp...
Страница 116: ...OUTLINE DRAWING 190A 116 Figure 27 Drive Chassis Outline DSD 412 195 Amp...
Страница 117: ...OUTLINE DRAWING 300A 117 Figure 28 Drive Chasis Outline DSD 412 300 Amp...
Страница 118: ...LAYOUT DRAWING 100A 118 Figure 29 Layout DSD 412 100 Amp A3 A1 A2 A2 L1 NEG GND L2 L3 POS...
Страница 119: ...LAYOUT DRAWING 195A 119 Figure 30 Layout DSD 412 195 Amp A3 A1 A2 A2...
Страница 120: ...LAYOUT DRAWING 300A 120 Figure 31 Layout DSD 412 300 Amp A3 A1 A2 A2...
Страница 121: ......