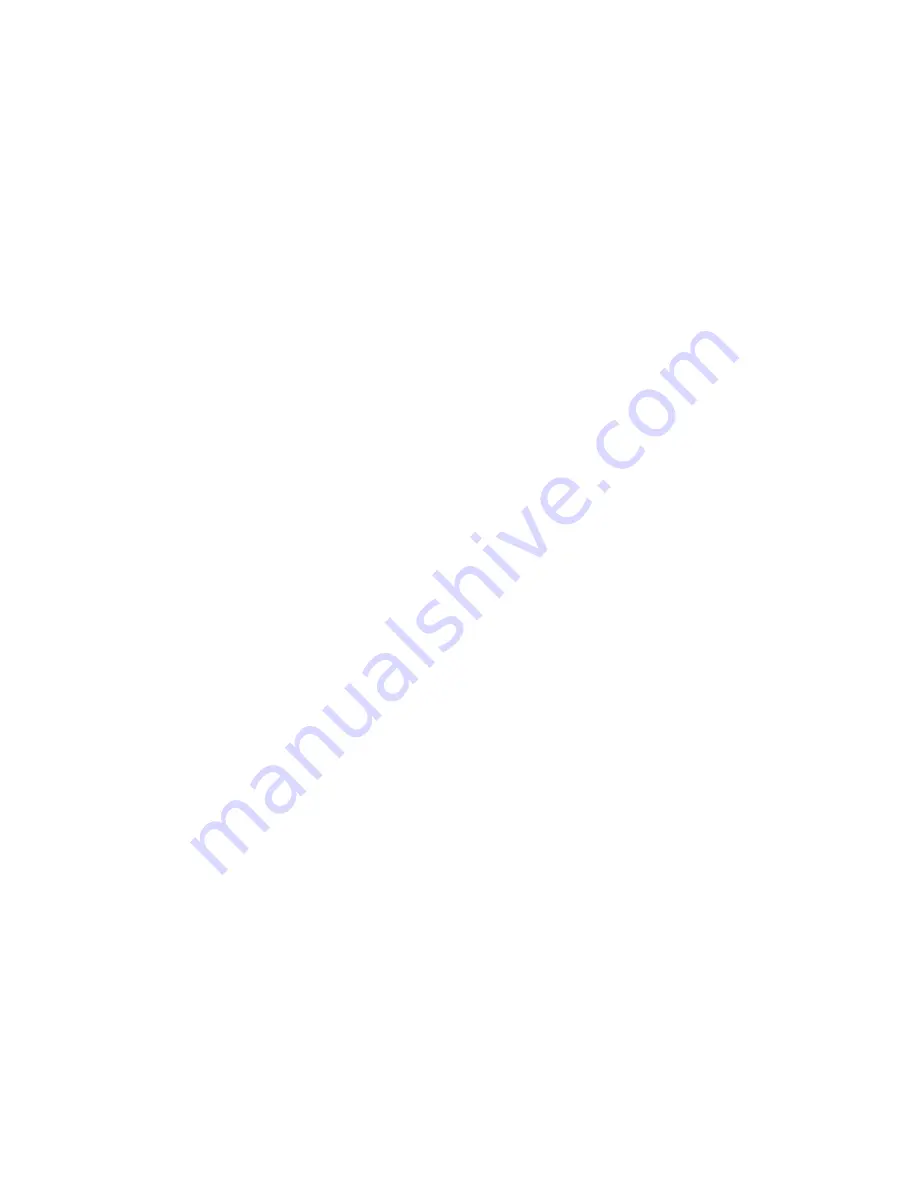
DRIVE SETUP AND ADJUSTMENT
46
Drive Setup &
Adjustments
Software Operating Features
•
The DSD 412 is configured by software to
operate geared and gearless elevators and
lifts. The SA407 Drive Control software
contains desirable feature improvements
from the previous version, SA274. Basic
features include...
•
User choice of operating speed reference
•
External analog reference follower
•
Serial link reference follower
•
Internal reference generator with S-Curve
smoothing, to one of 7 preset speeds (8
speeds including zero)
•
User choice of ft/min or m/sec speed
programming and display units
•
User choice between binary or progressive
relay selected internal preset speeds.
•
Selectable input control logic for Run-Up /
Run-Down or Run / Direction relay control
with internal preset speeds.
•
MagneTek exclusive E-Reg, elevator
velocity regulator
•
Simplified analog or serial link Pre-Torque
operation to prevent roll-back on starts
•
Controlled Current Ramp-Down to prevent
elevator brake thumping at stops
•
Internal frequency notch filter to reject rope
resonance interference.
•
Closed loop motor field current regulator
with simplified motor field weakening and
stand-by adjustments
•
Maintainance Armature Voltage Feedback
mode.
•
User selectable choices for relay logic
output, including:
•
Drive OK / No Faults relay
•
Invert/Noninvert Alarms Relay
•
Drive operating, OK to release brake
•
Car above/below speed X threshold
•
Car above/below Zero speed threshold
•
Car Moving Up
•
Car Moving Down
•
Speed Error above/below X threshold for Y
seconds.
•
Drive Standby Power Reduction
•
User selectable analog diagnostic trace
outputs
•
Diagnostic indicator for verifying logic input
and output conditions
•
Analog speed reference zero adjustment
•
Alarm Relay to indicate important but non-
critical conditions
•
Motor or transformer thermostat over-
temperature
•
Motor Over-Load
•
Drive Over-Heating
•
Low Utility Line Input
•
Safety related fault trapping with
diagnostics, including:
•
Motor Over-Current
•
Motor field Malfunction
•
Contactor Failure
•
Severe Utility Line disturbances
•
Encoder Loss
•
Over-Speed Trip
•
User selectable automatic or external
commanded Fault Reset
•
New features have been arranged to be
compatible with present installations of DSD
412 using General Elevator software
SA274. The factory default settings of
software SA407 are such that it will act like
SA274 software. The user must
consciously re-program one or more
selectable features to do otherwise.
•
Several new useful features have been
added for SA407, plus more diagnostic
codes to help pinpoint the cause of
problems when things go wrong during
commissioning. See the appropriate
sections for explanations of Anti-RollBack,
Brake Control, Drive Standby Power
Reduction, and operation with a Uni-Polar
Analog reference. Ramp rates 3 are now
activated by external logic command at
A1TB1-10.
Motor Field Current Control
Motor field current is held at Stand-By amps
function 53 when the elevator is idle. When
the Drive Enable command is given, field
current will rise as fast as possible to the level
programmed in function 50. The drive will not
allow a drive start to occur until motor field
current rises above the threshold level set at
function 32. At high speed, the motor field
current will automatically weaken to the level
set at function 49. If the field current feedback
fails to track the field current reference by
more than 5% for 5 seconds Fault ‘413’ will be
declared. The universal motor field control
module supplied with DSD 412 can operate
motor fields from 0.2 through 40.0 ADC.
Содержание DSD 412
Страница 1: ...DSD 412 DC Elevator Drive Technical Manual CS00407 rev 06...
Страница 6: ...6...
Страница 102: ...MAINTENANCE 102 Figure 24 Connector and E prom Locations...
Страница 103: ...MAINTENANCE 103 Figure 25 Test Point Locations...
Страница 115: ...OUTLINE DRAWING 100A 115 Figure 26 Drive Chassis Outline DSD 412 100 Amp...
Страница 116: ...OUTLINE DRAWING 190A 116 Figure 27 Drive Chassis Outline DSD 412 195 Amp...
Страница 117: ...OUTLINE DRAWING 300A 117 Figure 28 Drive Chasis Outline DSD 412 300 Amp...
Страница 118: ...LAYOUT DRAWING 100A 118 Figure 29 Layout DSD 412 100 Amp A3 A1 A2 A2 L1 NEG GND L2 L3 POS...
Страница 119: ...LAYOUT DRAWING 195A 119 Figure 30 Layout DSD 412 195 Amp A3 A1 A2 A2...
Страница 120: ...LAYOUT DRAWING 300A 120 Figure 31 Layout DSD 412 300 Amp A3 A1 A2 A2...
Страница 121: ......