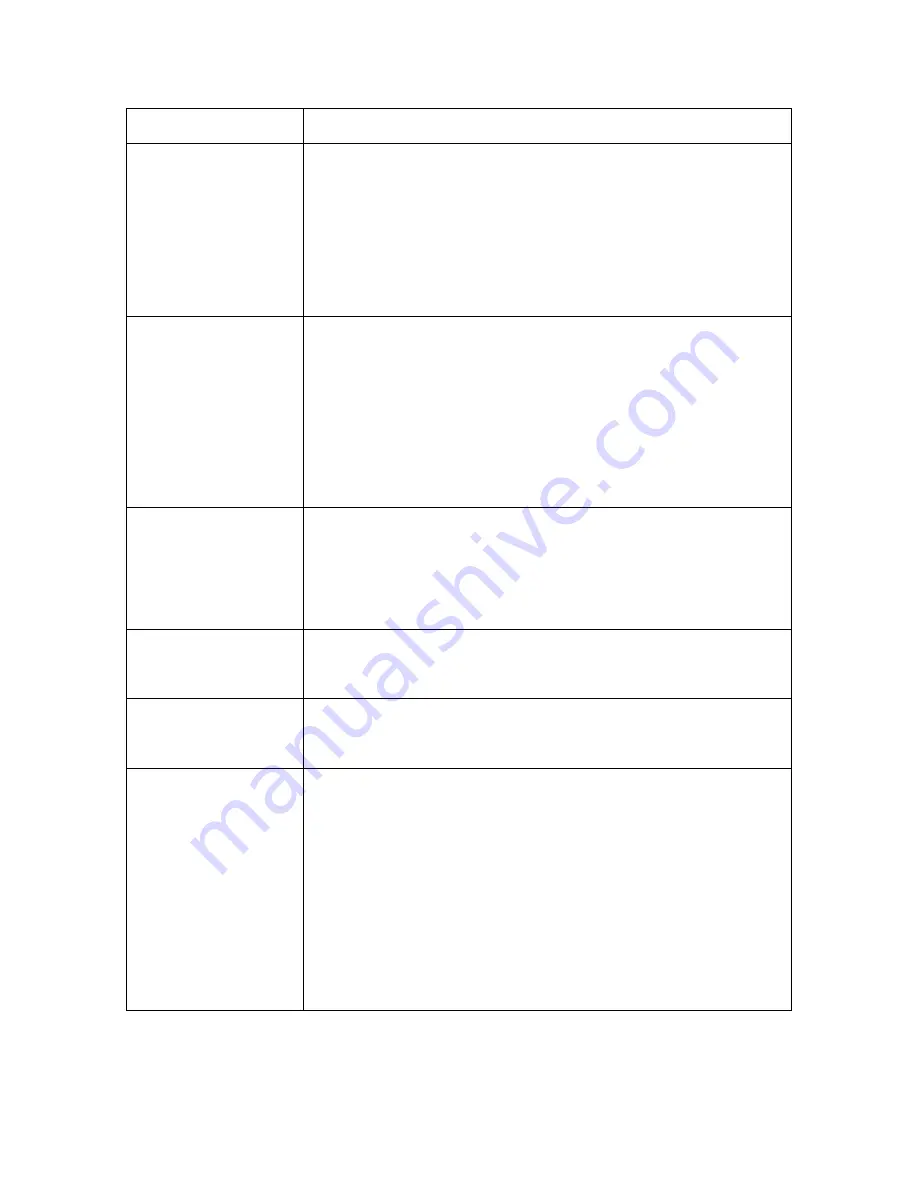
DRIVE FAULTS
90
ERROR/FAULT CODE
PROBABLE CAUSE/ — CORRECTIVE ACTION
407
DCU CEMF FAULT - The
CEMF of the motor exceeded 109% of
measured AC input voltage to the Drive. This is a warning only and
does not cause an automatic drive shut down. – Causes:
3 Phase Input AC Line Voltage drooped or is too low.
CEMF on motor rises above VAC input voltage.
Motor field current set too high. Verify weak field set point #49 Vs
desired motor voltage at top speed.
Check & correct motor field control tuning to prevent CEMF overshoot.
. Review and verify settings for #49, 50, 51, 52, 54, & 55.
408
PCU CEMF FAULT -
The CEMF of the motor exceeded 118% of the
rated VAC input voltage to the Drive. This fault causes a drive shut
down to prevent fuse blowing. – Causes:
3 Phase Input AC Line Voltage is low. Check and correct.
Incorrect motor field current setting or field regulator miss-operation
causing excessive CEMF. Check & correct.
Excessive drive speed overshoot. Correct with velocity regulator
adjustments.
Check and correct motor field control dynamic tuning to prevent CEMF
overshoot. Review and verify settings for #49, 50, 51, 52, 54, & 55.
409 PCU
RESET
— PCU processor was unexpectedly reset. Verify that
correct PCU software and revision level is being used. Possible
problem with main circuit card hardware. Look for external noise
interference. Ensure that equipment and signal grounding connections
are proper. Correct as necessary. If problem remains, replace Drive
Control PCB.
410 SPEED
ERROR TRIP FAULT ---
Indicates that a large speed error
existed for a significant period of time. Look for dragging brake or
weak motor field. See the explanations for #99 & #100.
411
MAX AUTO-RESETS ATTEMPTED ---
Indicates that more than 5
automatic resets were necessary in less than 20 minutes of
accumulated time. See the explanation for #101.
413
FIELD CURRENT TRACKING FAULT ---
Indicates that the
ACTUAL
field current is failing to track the field current
COMMAND
by more
than F192 (Default = 0.05) for 5 seconds.
This is not a shut down
fault
.
1. Check AC voltage on AC1 and AC2 – Typically 1.5 to 2.5 times VAC
(min), where VACmin = VDC/0.9 or (Full Fld Amps * Field
resistance)/0.9
2. Drives not using correct self-tune values and/or field response set
incorrectly.
3. Monitor F620 Fld Trkg Diff, it should be less than F192 "F413
Detection Level". By setting F192 higher it can eliminate this warning,
Caution should be observed prior to doing this, If the proper conditions
exist the data on F620 display should not exceed 0.05PU for over 5
seconds.
Содержание DSD 412
Страница 1: ...DSD 412 DC Elevator Drive Technical Manual CS00407 rev 06...
Страница 6: ...6...
Страница 102: ...MAINTENANCE 102 Figure 24 Connector and E prom Locations...
Страница 103: ...MAINTENANCE 103 Figure 25 Test Point Locations...
Страница 115: ...OUTLINE DRAWING 100A 115 Figure 26 Drive Chassis Outline DSD 412 100 Amp...
Страница 116: ...OUTLINE DRAWING 190A 116 Figure 27 Drive Chassis Outline DSD 412 195 Amp...
Страница 117: ...OUTLINE DRAWING 300A 117 Figure 28 Drive Chasis Outline DSD 412 300 Amp...
Страница 118: ...LAYOUT DRAWING 100A 118 Figure 29 Layout DSD 412 100 Amp A3 A1 A2 A2 L1 NEG GND L2 L3 POS...
Страница 119: ...LAYOUT DRAWING 195A 119 Figure 30 Layout DSD 412 195 Amp A3 A1 A2 A2...
Страница 120: ...LAYOUT DRAWING 300A 120 Figure 31 Layout DSD 412 300 Amp A3 A1 A2 A2...
Страница 121: ......