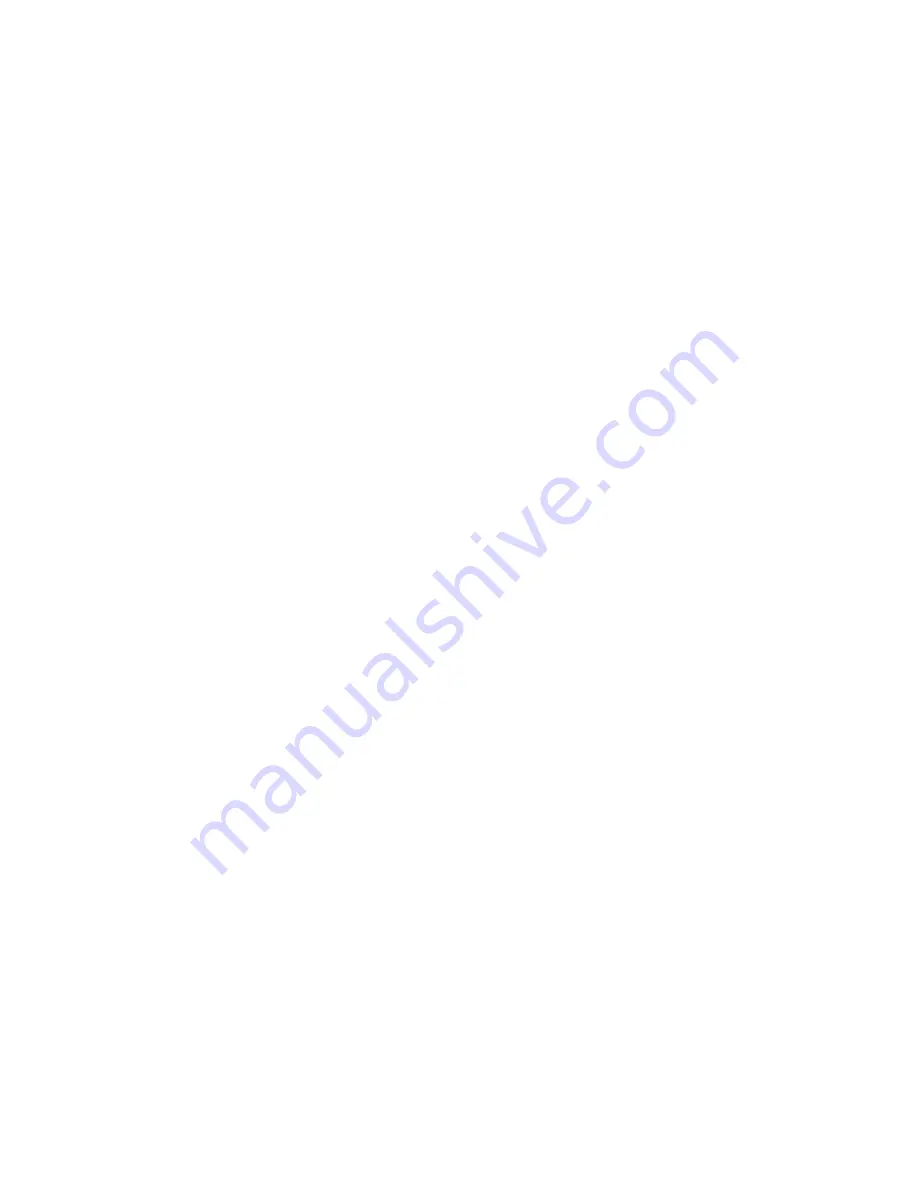
DRIVE SETUP
73
Sticking Brake Detection
A sticking elevator brake can be detected by
observing Speed Error. The unexpected
friction caused by a sticking brake will create
an abnormally large speed error, in order to
get the large motor current necessary for the
drive motor to produce enough torque to pull
through the brake. This cause for motor
current is not the same as that during normal
accel/decel where a change in velocity
command drives the demand for motor
current and torque, but speed/velocity
tracking remains on target. Therefore the
Speed Error detection method will be more
effective than using the Current X Time motor
overload function to detect this equipment
malfunction.
If it is desired that detection of a sticking
brake should cause an automatic shutdown
of the drive.
See the explanation for function
parameter settings #99 and #100. Set
#99 to 2 seconds. Set #100 to 10% or
lower as necessary to cause the
function to trip off with drive shutdown
Fault F410 when the brake does stick,
but not so sensitive that normal accel or
decel causes an F410 shut-down.
Verify by test that empty car down or full
payload weight up will not cause
nuisance trips.
If it is desired that a sticking brake be
detected, but not cause an automatic drive
shutdown....
See the explanation for programmable
logic output type ‘H’ or ‘I’ using
parameter adjustments #120 and #121.
Follow the directions for parameters
#183-187 to program either function ‘H’
or ‘I’ to activate or deactivate a logic
output. Set #120 for a detection time of
2 seconds. Set #121 to 10% or lower
as necessary to cause the function to
operate when the brake does stick, but
not so sensitive that normal accel or
decel operation causes false detections.
Verify by test that empty car down or full
payload weight up will not cause
nuisance trips.
Start – Stop Timing
A typical elevator run sequence is shown in Figure
19: Elevator Start - Stop Timing A descriptive
explanation is given below.
Start Sequence – Mode 2, internal pre-set speeds
1. Close Drive & Field Enable – Sets field current
reference to Full Field, enables drive to
operate. This contact must be held closed
during entire elevator run, including armature
current ramp down. Opening of this contact
will disable the drive and cause the loop
contactor to be dropped immediately.
2. Close Safety-Chain circuit. – Must be closed
for drive to start. Must remain closed during
entire elevator run. Otherwise, an F405 fault
will result.
3. Select desired direction and speed – May be
done before or after drive is told to Run.
4. Close Hardware Run (or Run-Up or Run-Down
contact) – Causes LPR to pick when field
current is greater than setting #32. LPR picks
contactor, which closes Loop Confirm – Drive
will begin running by pre-loading the speed
error integrator with the available pre-torque
signal, if enabled at Function #114. Logic
Output Selection ‘C’, Run Engaged, will
become energized to indicate that the drive
has control of motor speed. Speed will begin
to accelerate toward desired speed, if not set
at zero. If contactor fails to pick, F402. If
motor armature circuit is not closed before
Loop Confirm closes, an F98 or F901 may
occur.
5. Release brake - Timing of actual brake
release must be coordinated with starting the
drive and/or changing the target speed. The
drive must be running and be either pre-
torqued, or starting to accelerate, or have ARB
engaged to prevent rollback.
6. A new target speed and or direction may be
selected before or after the drive is started.
When speed rises above the setting of #64,
the Low Speed logic indicator will turn off.
(Output function ‘F’)
Содержание DSD 412
Страница 1: ...DSD 412 DC Elevator Drive Technical Manual CS00407 rev 06...
Страница 6: ...6...
Страница 102: ...MAINTENANCE 102 Figure 24 Connector and E prom Locations...
Страница 103: ...MAINTENANCE 103 Figure 25 Test Point Locations...
Страница 115: ...OUTLINE DRAWING 100A 115 Figure 26 Drive Chassis Outline DSD 412 100 Amp...
Страница 116: ...OUTLINE DRAWING 190A 116 Figure 27 Drive Chassis Outline DSD 412 195 Amp...
Страница 117: ...OUTLINE DRAWING 300A 117 Figure 28 Drive Chasis Outline DSD 412 300 Amp...
Страница 118: ...LAYOUT DRAWING 100A 118 Figure 29 Layout DSD 412 100 Amp A3 A1 A2 A2 L1 NEG GND L2 L3 POS...
Страница 119: ...LAYOUT DRAWING 195A 119 Figure 30 Layout DSD 412 195 Amp A3 A1 A2 A2...
Страница 120: ...LAYOUT DRAWING 300A 120 Figure 31 Layout DSD 412 300 Amp A3 A1 A2 A2...
Страница 121: ......