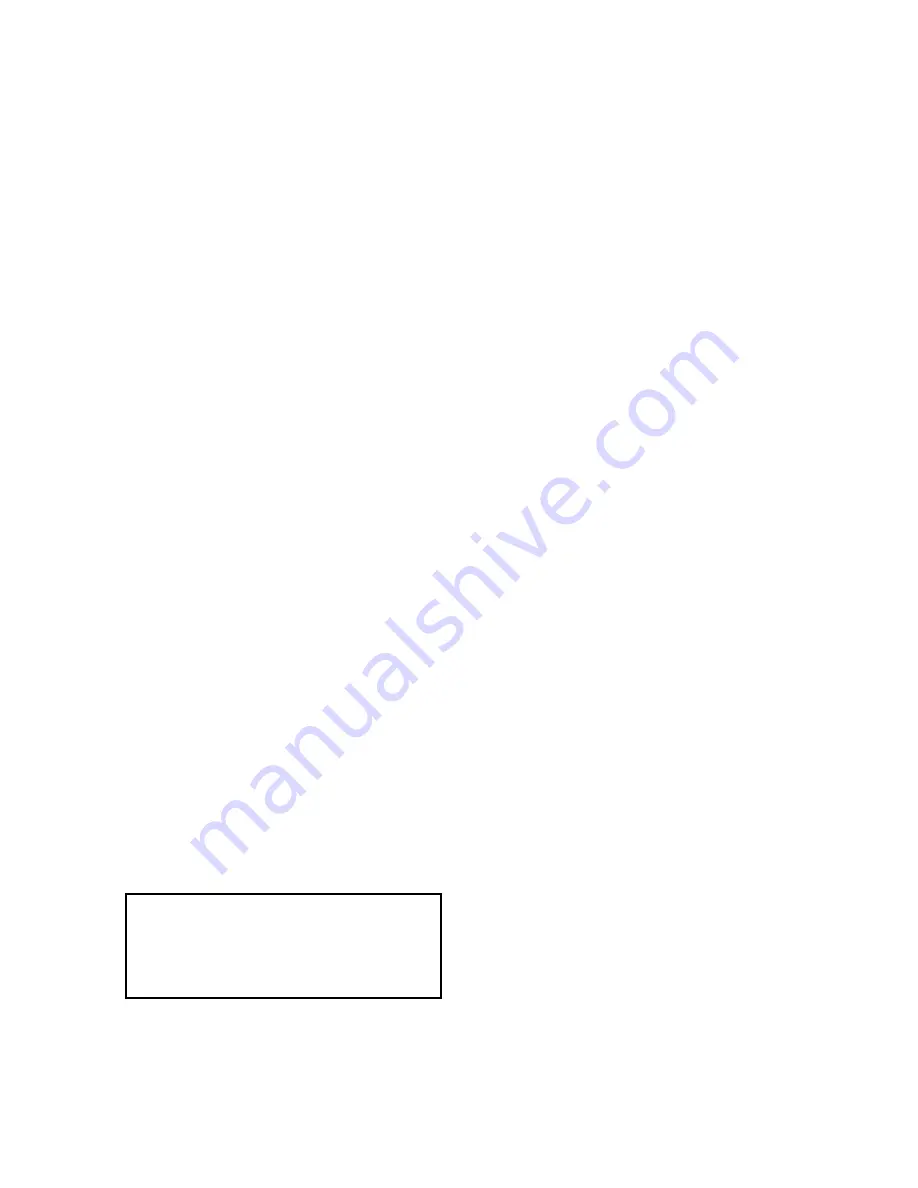
MAINTENANCE
106
Drive Control PCB Replacement.
1. Release the front cover of the drive by
pulling out the four corner fasteners,
approximately 1/4 inch, until they snap;
then remove the cover.
2. Mark each cable and wire to ensure
proper reconnection; before
disconnecting them.
3. Disconnect all cables and wires from the
Drive Control PCB. Remove nine
screws holding the Drive Control PCB
to the swing out door chassis from the
front, and remove the Drive Control PCB
from the power cube.
4. If there is an optional circuit board
attached to the back of the Drive Control
PCB, disconnect the Local I/O cable
from J12 on the Drive Control PCB.
Then remove the mounting screws
which secure the Local I/O PCB to the
back of the Drive Control PCB. Re-
attach the same Local I/O PCB to the
replacement Drive Control PCB using
the same hardware in reverse order.
Re-attach the J12 cable.
5. Mount the new Drive Control PCB into
the power cube by reversing procedure
in steps 1 through 3. Be sure to re-use
the small diameter flat washers under
the screw heads on the Drive Control
PCB to maintain proper electrical
clearances.
6.
Remove
integrated circuits (ICs) U13,
U14, U39, U40 as appropriate, from the
defective Drive Control PCB. Install into
the same positions on the new board.
Ensure that polarity notch on IC is
aligned with the silk screen notch on the
board. Each IC is marked with the
proper “U” number in the bottom left
hand corner of its label.
7. Perform Start-Up Procedure.
IC Replacement
IMPORTANT
When replacing any printed circuit board
(PCB) or any integrated circuit (IC) in the
DSD drive, proper Electro-static Discharge
(ESD) procedure MUST be followed.
EPROM Replacement
To replace an EPROM (U13, U14, U39,
U40), first check that the new device has the
same “U” number on its label as the
defective device. Remove the existing
device and install the replacement in the
same position. Then perform the Start-Up
Procedure in Drive Start .
NVRAM Replacement
To replace an NVRAM device (U56),
remove the defective device and install the
replacement in the same position. Then
perform the Start-Up Procedure. If you have
kept a record of the parameter settings you
should be able to re-load all parameter
values, save the data and go. If you do not
have a record of the working drive
parameter settings, you must re-enter and
re-tune all parameters by repeating all drive
adjustment procedures.
Testing and Replacement of Power
Components.
Fuse Replacement
Whenever attaching a fuse, wire or bus bar
to another component to achieve an
electrical connection, always apply a thin
coating of electrically conductive joint
compound to all contacting surfaces.
Magnetek recommends using Joint-Al-Z
compound for all bolted electrical power
connections.
Diagnosis of fuses
— The input AC fuses
are checked when power is initially applied
during the Start-Up sequence of the drive,
and again when a PCU DIAGNOSTICS
#998 is performed. The output DC fuse is
checked only when a PCU DIAGNOSTICS
#998 is performed. when running, blown
fuses may cause an F910 or F404.
With
input power disconnected
, the fuses may be
checked with an ohmmeter while still in
place in the circuit. Replace any fuse that
indicates a resistance reading of more than
a fraction of an ohm. Re check that the fuse
is indeed open/blown when removed from
the circuit. Be aware that other circuitry may
cause a low resistance reading to appear
across a blown fuse. If there are doubts
about the fuse being good or bad, remove
connections to at least one end before
measurement. For maximum assurance to
prevent call-backs, Magnetek recommends
replacing all three AC line fuses even when
only one or two are blown.
Содержание DSD 412
Страница 1: ...DSD 412 DC Elevator Drive Technical Manual CS00407 rev 06...
Страница 6: ...6...
Страница 102: ...MAINTENANCE 102 Figure 24 Connector and E prom Locations...
Страница 103: ...MAINTENANCE 103 Figure 25 Test Point Locations...
Страница 115: ...OUTLINE DRAWING 100A 115 Figure 26 Drive Chassis Outline DSD 412 100 Amp...
Страница 116: ...OUTLINE DRAWING 190A 116 Figure 27 Drive Chassis Outline DSD 412 195 Amp...
Страница 117: ...OUTLINE DRAWING 300A 117 Figure 28 Drive Chasis Outline DSD 412 300 Amp...
Страница 118: ...LAYOUT DRAWING 100A 118 Figure 29 Layout DSD 412 100 Amp A3 A1 A2 A2 L1 NEG GND L2 L3 POS...
Страница 119: ...LAYOUT DRAWING 195A 119 Figure 30 Layout DSD 412 195 Amp A3 A1 A2 A2...
Страница 120: ...LAYOUT DRAWING 300A 120 Figure 31 Layout DSD 412 300 Amp A3 A1 A2 A2...
Страница 121: ......