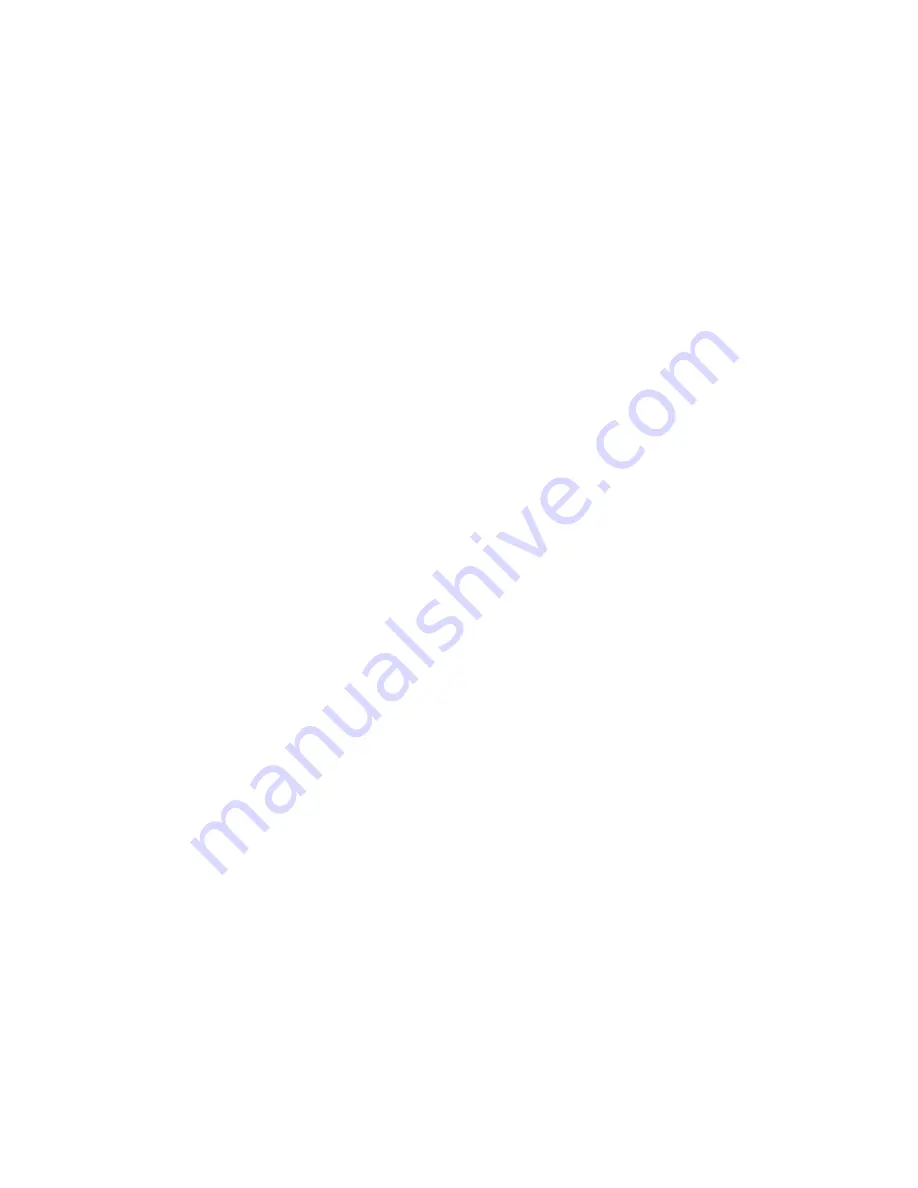
DRIVE SETUP AND ADJUSTMENT
50
Function # 10
Encoder P/R
Units: P/R
Range: 600. – 19,999.
Default: 1024.
This entry sets the per channel pulses per
revolution per the encoder nameplate.
Function # 11
Motor RPM
Units: RPM
Range: 50.0 – 1999.0
Default: 1150
This entry sets the motor speed at rated
elevator contract speed. The motor RPM X
Encoder PPR X Encoder/Motor Ratio is what
will actually be speed regulated. May be used
to compensate for minor sheave diameter
variations. Adjust this setting to obtain the
correct linear speed at 1.0 per unit velocity
reference.
Function # 12
Overspeed %
Units: %
Range: 0.0 – 150.0
Default: 110.0
This entry sets the positive and negative
overspeed trip point of the motor used on the
drive. If the motor speed exceeds this value,
the drive will fault. This value is entered as a
percent of rated motor speed (RPM).
Function # 14
Volt Sense %
Units: %
Range: 0.0 – 100.0
Default: 25.0
This entry sets the minimum armature voltage
where the tach loss and reverse tach
functions will become operative. This
parameter prevents nuisance tach faults at
low speeds and high torque loads. For
example, if the rated motor armature voltage
is 500 Vdc and this input is set at 10%, the
tach loss function will become operative only
when the armature voltage is above 50 Vdc.
This numeric input adjusts the tach loss
sensing function ability to ignore motor IR
drop.
Function # 15
Tach Sense %
Units: %
Range: 0.0 - 100.0
Default: 5.0
This entry sets the percentage of tach
feedback below which a tach loss will be
declared. But this alone will not result in a
tach loss fault being declared. Thus, a tach
loss will be declared when the per unit
armature voltage is above the level that is the
sum of function 14 VOLT SENSE %, and
function 15, TACH SENSE % and the per unit
tach feedback is less than the value entered
for TACH SENSE %. For example, for default
values of 25%, for function 14 and 5%, for
function15, a Tach Loss will be declared when
motor voltage is above 30% (25+5) and the
encoder speed feedback indicates less than
5% speed.
Function # 16
Encoder/Motor Ratio
Units: -
Range: 1.000 - 19.000
Default: 1.000
This is the ratio of encoder RPM to motor
RPM. If friction wheel drive is utilized for the
encoder, the motor sheave diameter divided
by the tach wheel diameter should be entered
here. This value will multiply the encoder
pulses per revolution to obtain proper motor
rpm speed feedback information and
regulation. If the encoder is direct coupled to
the motor shaft, this function must be set to a
value of 1.0.
Function # 17
Rated Car Speed
Units: -
Range: 1.0 – 1,900.0
Default: 400.0
This entry sets the calibration factor for
internal pre-set speeds and car speed display
via function function 600. The units may be
ft/min or m/sec or cm/sec as determined by
the user. However the units used for this
parameter must also be used to set all other
pre-set speeds. When the motor is turning at
rated speed in RPM as programmed in
function 11, then function 600 will display the
number in programmed 17.
Содержание DSD 412
Страница 1: ...DSD 412 DC Elevator Drive Technical Manual CS00407 rev 06...
Страница 6: ...6...
Страница 102: ...MAINTENANCE 102 Figure 24 Connector and E prom Locations...
Страница 103: ...MAINTENANCE 103 Figure 25 Test Point Locations...
Страница 115: ...OUTLINE DRAWING 100A 115 Figure 26 Drive Chassis Outline DSD 412 100 Amp...
Страница 116: ...OUTLINE DRAWING 190A 116 Figure 27 Drive Chassis Outline DSD 412 195 Amp...
Страница 117: ...OUTLINE DRAWING 300A 117 Figure 28 Drive Chasis Outline DSD 412 300 Amp...
Страница 118: ...LAYOUT DRAWING 100A 118 Figure 29 Layout DSD 412 100 Amp A3 A1 A2 A2 L1 NEG GND L2 L3 POS...
Страница 119: ...LAYOUT DRAWING 195A 119 Figure 30 Layout DSD 412 195 Amp A3 A1 A2 A2...
Страница 120: ...LAYOUT DRAWING 300A 120 Figure 31 Layout DSD 412 300 Amp A3 A1 A2 A2...
Страница 121: ......