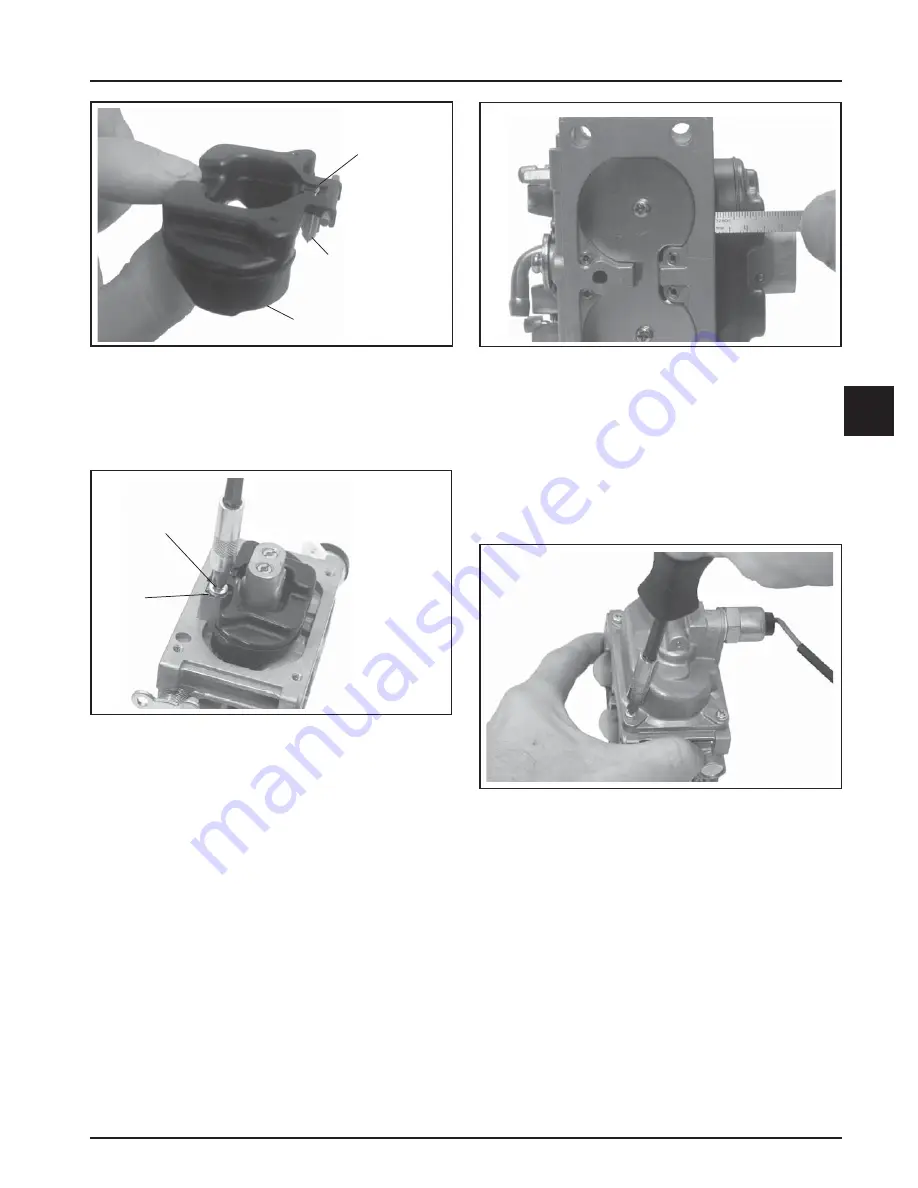
5.9
Section 5
Fuel System and Governor
5
Figure 5-16. Checking Float Height.
NOTE: Be sure to measure from the casting surface,
not the rubber gasket, if still a
tt
ached.
9. When the proper
fl
oat height is obtained,
carefully reinstall the fuel bowl onto the
carburetor, using new O-rings. Secure with
the four original screws. Torque the screws to
2.5 ± 0.3 N·m (22 ± 3 in. lb.)
. See Figure 5-17.
Figure 5-17. Installing Fuel Bowl.
10. Install the carburetor and reassemble the engine
as outlined in Section 10
Reassembly
.
Clip
Inlet
Needle
Float
Figure 5-14. Float and Inlet Needle Details.
6. Install the
fl
oat and inlet needle down into the
seat and carburetor body. Install the new pivot
pin through the
fl
oat hinge and secure with the
new retaining screw. See Figure 5-15.
Retaining
Screw
Pivot
Pin
Figure 5-15. Installing Float Assembly.
7. Hold the carburetor body so the
fl
oat assembly
hangs vertically and rests lightly against the
fuel inlet needle. The inlet needle should be
fully seated but the center pin of the needle (on
retainer clip end) should not be depressed. Check
the
fl
oat height adjustment.
NOTE: The inlet needle center pin is spring loaded.
Make sure the
fl
oat rests against the fuel inlet
needle without depressing the center pin.
8. The correct
fl
oat height se
tt
ing is
17 mm
(0.669 in.) ± 1.5 mm (0.059 in.)
, measured from
the
fl
oat bo
tt
om to the body of the carburetor.
See Figure 5-16. Replace the
fl
oat if the height
is di
ff
erent than speci
fi
ed.
DO NOT
a
tt
empt to
adjust by bending
fl
oat tab.
Содержание Comand Pro CH1000
Страница 1: ...SERVICE MANUAL HORIZONTAL CRANKSHAFT CH940 CH1000...
Страница 2: ......
Страница 4: ......
Страница 30: ...4 4 Section 4 Air Cleaner and Air Intake System...
Страница 52: ...6 6 Section 6 Lubrication System...
Страница 96: ...8 16 Section 8 Disassembly...
Страница 110: ...Section 9 Inspection and Reconditioning 9 14...
Страница 140: ...10 30 Section 10 Reassembly...
Страница 141: ......